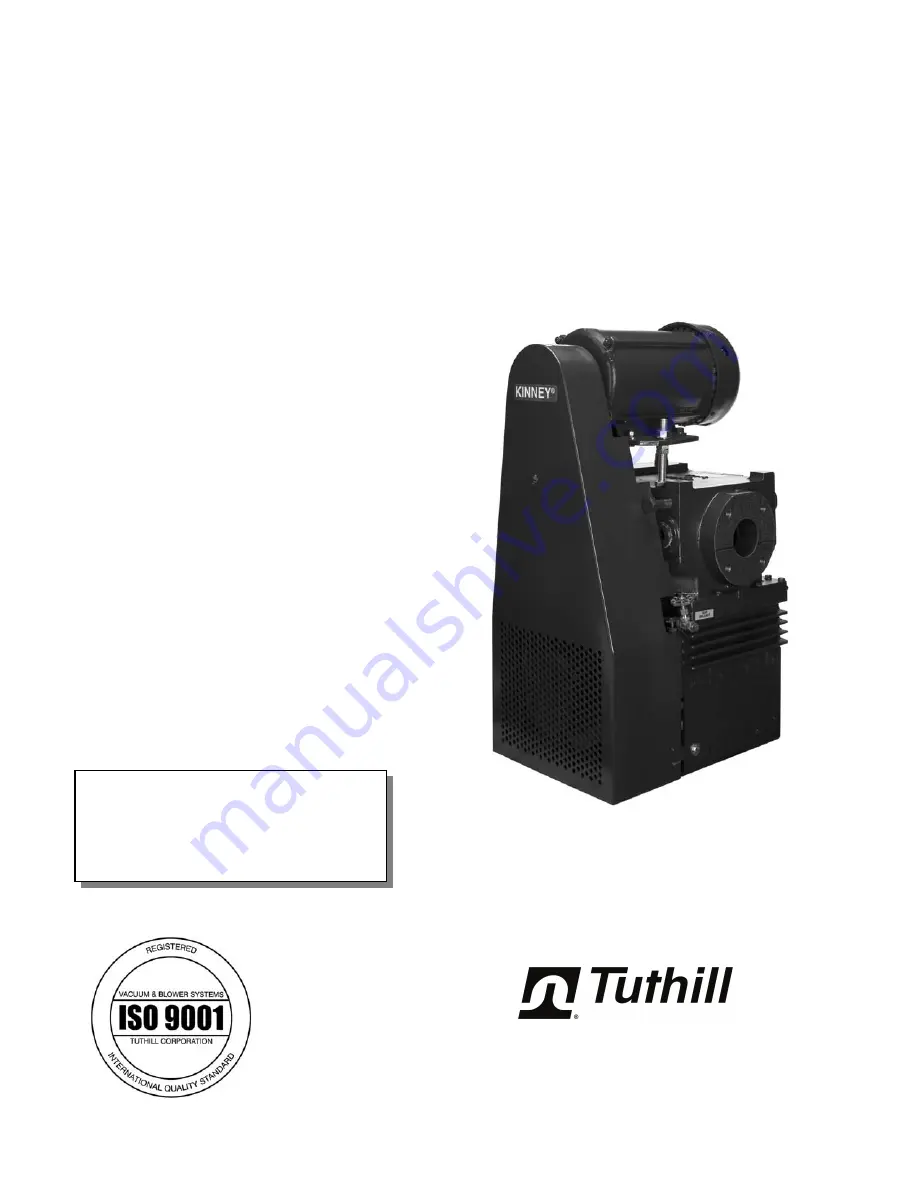
Two Stage, Triplex Rotary Piston Pumps
KTC-60
KTC-112
Models
INSTALLATION
OPERATION
MAINTENANCE
REPAIR
MANUAL
WARNING
DO NOT OPERATE BEFORE
READING MANUAL.
02/2006
ADVANCING THE STANDARDS IN VACUUM TECHNOLOGY
4840 West Kearney Street
Springfield, Missouri USA 65803-8702
Tel 417 865-8715 800 825-6937 Fax 417 865-2950
E-mail: [email protected]
tuthillvacuumblower.com
KINNEY
®
KTC
™
SERIES
Manual 1845-2
Summary of Contents for KTC SERIES
Page 18: ...18 KTC 60 KTC 112 Exploded View ...
Page 22: ...22 NOTES ...