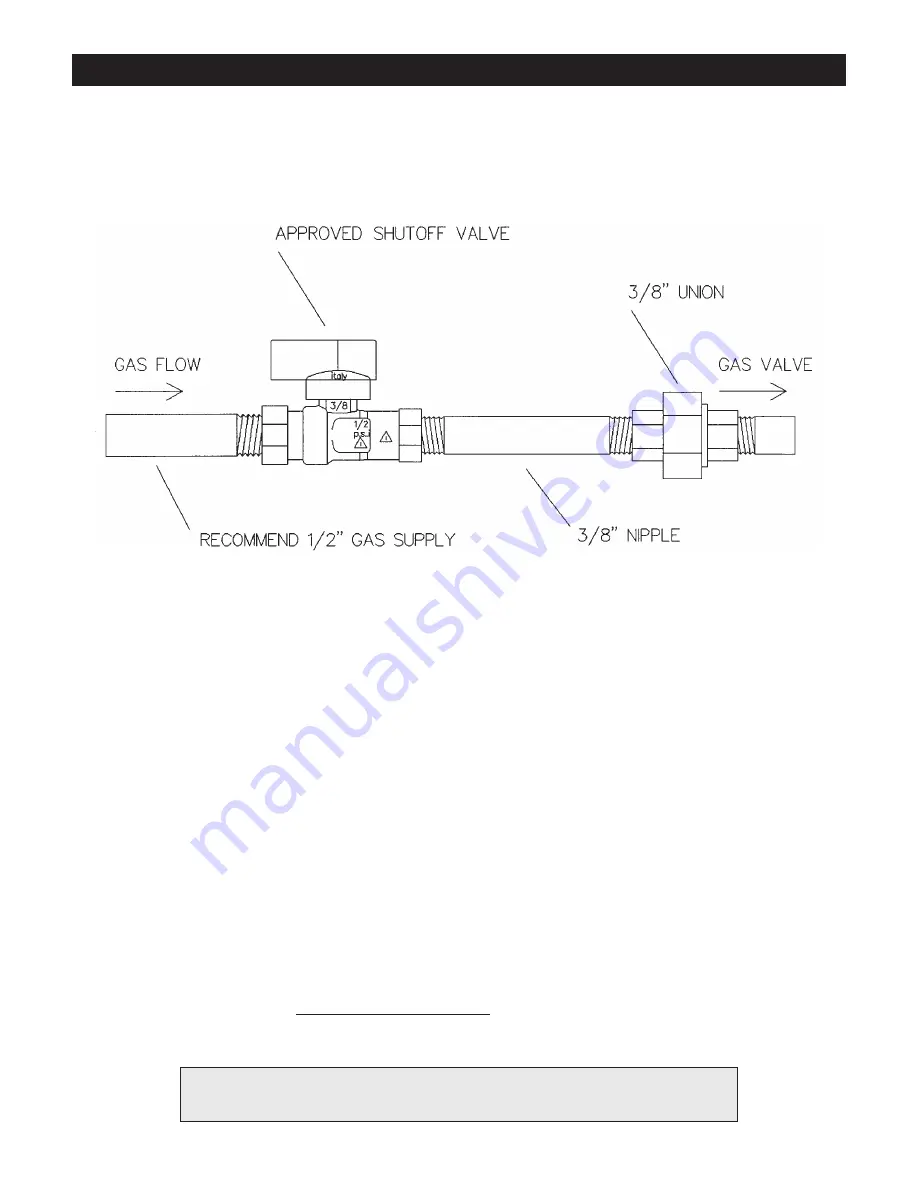
1.
The gas pipeline is brought into the unit on the back left side of the unit.
2.
The gas control inlet is 3/8". Typical installation layout for rigid pipe is shown below.
3.
When using copper or flex connector, use only approved fittings. Always provide a union so that gas line can
be easily disconnected for burner or fan servicing. See gas specification for pressure details and ratings.
4.
When a vertical section of gas pipe is required for installation, a condensation trap is needed.
See CAN/CGA-B149.1 or .2 for code details.
5.
For natural gas, a minimum of 3/8" iron pipe with gas minimum pressure of 5.5" w.c. must be used for supply
from the gas meter. Consult with the local gas utility if any questions arise concerning pipe sizes.
6.
A 1/8" NPT plugged tappings are accessible for test gauge connection both on the inlet and outlet of the gas
valve.
7.
Turn the gas supply ON and check for leaks. DO NOT USE OPEN FLAME FOR THIS PURPOSE. Use an
approved leak testing solution.
8.
The appliance and its individual shutoff valve must be disconnected from the gas supply piping system during
any pressure testing of that system at test pressures in excess of 1/2 PSIG (3.5 KPa).
9.
The appliance must be isolated from the gas supply piping system by closing its individual shutoff valve
during any pressure testing of the gas supply piping system at test pressures equal to or less than 1/2 PSIG
(3.5 KPa).
NOTE: The gas line connection may be made of 1/2" rigid pipe or an approved flex connector. Since some
municipalities have additional local codes, it is always best to consult your local authorities and the current CAN/CGA-
B149.1 or .2 installation code in Canada or the National Fuel Gas code ANSI Z223.1 in the U.S.A.
For the state of Massachusetts a
T-handle gas shut-off valve
must be used on a gas appliance. This T-handle gas
shut-off valve must be listed and approved by the state of Massachusetts. This is in reference to the state of
Massachusetts state code CMR238.
GAS LINE INSTALLATION
This gas appliance should be installed by a qualified installer in accordance with local building codes and with current
CSA-B149.1 installation codes for Gas Burning Appliances and Equipment in Canada and the National Fuel Gas
Code Z223.1 in the United States.
NOTE: IF THE OPTIONAL FAN KIT IS TO BE INSTALLED IT IS HIGHLY RECOMMENDED THAT IT BE
ATTACHED TO THE STOVE BEFORE THE STOVE IS PUT IN ITS FINAL POSITION.
8
IMPORTANT:
Always check for gas leaks with a soap and water solution.
Do not use open flame for leak testing.
7
Summary of Contents for FV200NE
Page 18: ...Gas Conversion for Modulator PART C WARNING WARNING 18...
Page 21: ...Configuration 1 Basic manual HI LO and manual ON OFF capabilities 21...
Page 22: ...Receiver Module 584 523 521 221 1001 P221SI Receiver Module 584 523 521 221 1001 P221SI 22...
Page 23: ...Receiver Module 584 523 521 221 1001 P221SI Receiver Module 584 523 521 221 1001 P221SI 23...