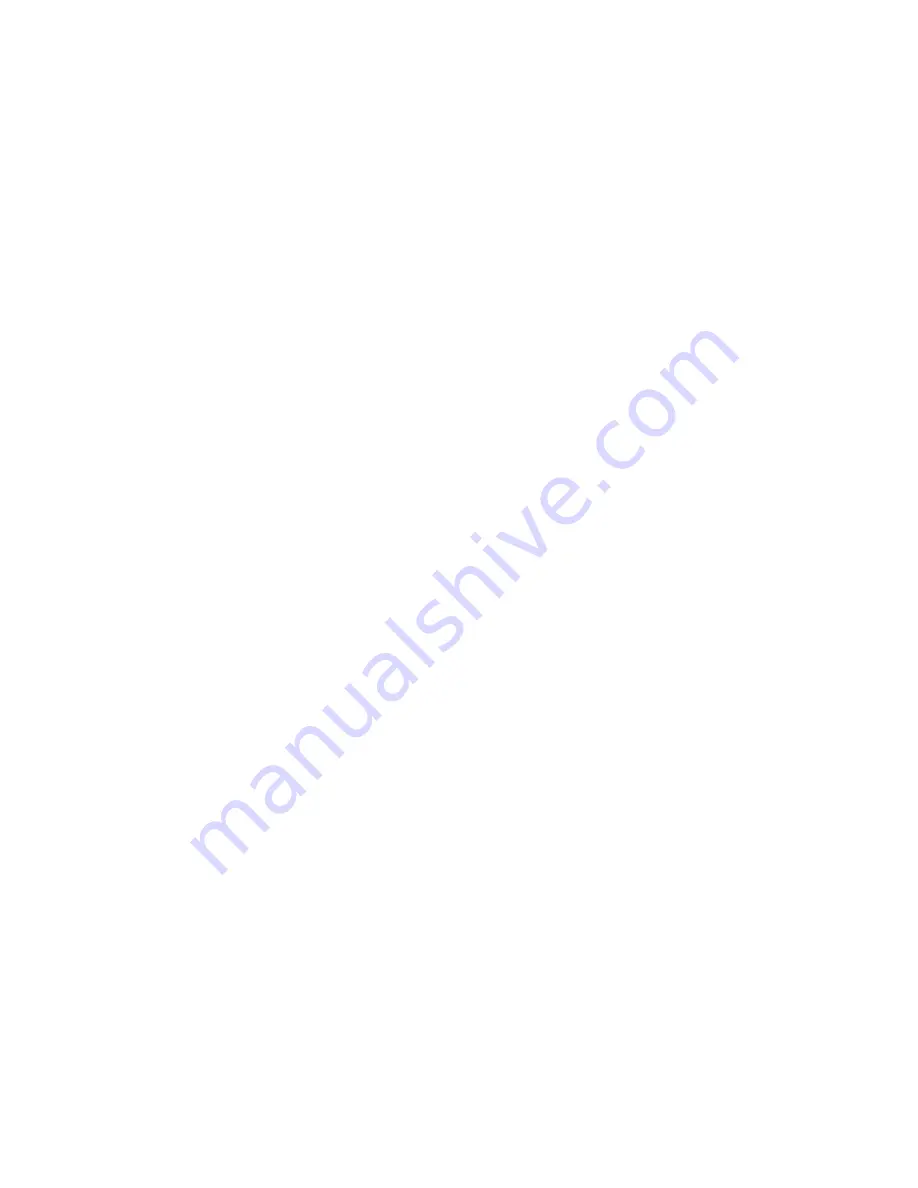
18
5 INSTRUCTION NOTES
5.1 Operation environment
1
)
Welding operation should be carried out in a relatively dry environment with air humidity
usually less than 90%.
2
)
Ambient temperature should be kept between -10
C ~40
C.
3
)
Welding in the sun or rain should be avoided and water or rainwater should never be seeped into
the welder interior.
4
)
Welding in the dusty area or under a corrosive gas environment should be avoided.
5
)
Gas protection welding operation in an environment with strong air flow should be avoided.
5.2 SAFTY
In this welder over-voltage, over-current and overheat protection circuits have been installed
beforehand. When the grid voltage, output current and machine temperature surpass the set
standards, the machine will stop automatically. But excessive use (for example, when the
voltage is too high) can still lead to the breakdown of the welder. So you have to pay attention to
the following items:
1
)
Good ventilation
!
This machine is a small type welder. In operation a high working current flows in and natural
ventilation is unable to meet the welder’s requirement for cooling. So a fan is fitted to
effectively cool the welder to keep it work smoothly.
Operators should make sure that the vent is not covered or plugged, the distance of the welder
from its surrounding objects is not less than 0.3 m and good ventilation is kept all the time. All
these are very important for better operation of the welder and longer service life of the welder.
2
)
No overload
!
Operators should bear in mind that maximum permissible load current (relative to the selected
load duration factor) be observed at any time and welding current should never surpass the
maximum permissible load current.
Over-current will shorten the service life of the welder remarkably and even burn it down.
3
)
No over-voltage
!
Power voltage is shown in the main performance parameter table. In general, the voltage
auto-compensation circuit in the welder will ensure the welding current remain within the
permissible range. If power voltage surpasses the permissible value, the welder will be broken
down. Operators should fully know this and adopt corresponding preventive measures.
4
)
Behind each welder there is a grounding screw with the grounding mark. Before operation the
shell of the welder should be grounded reliably by a cable wire with a sectional area bigger than
6mm
2
so as to release static electricity or prevent any accident due to leakage.
5
)
If the welding machine exceeds the standard load duration factor in operation, it may probably
go into a protective state suddenly and stop work, which indicates it has exceeded the standard