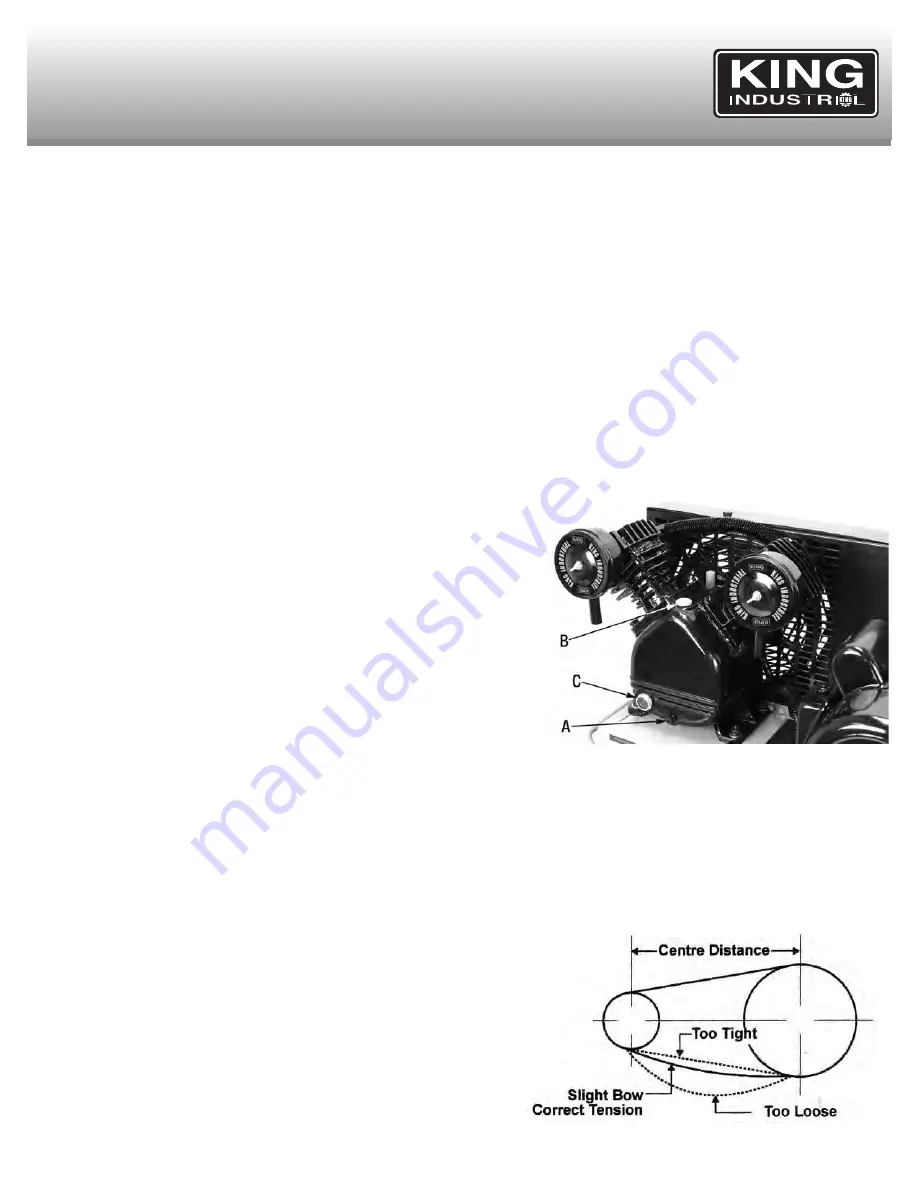
OPERATIONAL GUIDELINES
& MAINTENANCE
OPERATIONAL GUIDELINES
Moisture in compressed air
When humidity is high or when the compressor is in continuous use for an extended period of time, this moisture will collect in the air tank.
When using a spray gun or sandblast gun, this water will be carried from the tank through the hose and out of the gun as droplets mixed with
the spray material. This will cause water spots in a paint job, especially when spraying other than water based paint. If sandblasting, it will cause
the material to cake and clog the gun, rendering it ineffective. An optional air control unit with dirt and moisture removal should be used to
prevent these undesireable results.
MAINTENANCE
Before doing any maintenance or adjustments to your air compressor, the following safety precautions should be taken:
- Turn power off (turn circuit breaker off or unplug power cord), drain air tank of pressure.
After Use:
1) Set the “OFF/AUTO” lever to “OFF”.
2) Pull ring on safety valve (D) Fig. 8, allowing air to bleed from the tank until tank pressure is approximately 20 PSI. Release safety valve ring.
3) Drain water from air tank. Open drain valve lever (A) Fig.9, turn it counterclockwise to open.
WARNING!
: Water will condense in the air tank. If not drained water will corrode and weaken the air tank causing a risk of air tank rupture.
NOTE:
If drain valve is plugged, pull ring on safety valve (D) Fig.8, and hold until all air pressure has been released. The valve can then be
removed, cleaned, and reinstalled.
4) After the water has been completely drained, turn drain valve clockwise to close.
Daily or before each use
1) Check oil level. Oil level must be in the centre of the red dot of oil sight glass.
2) Drain condensation from tank.
3) Check for any unusual noise or vibration.
4) Be sure all nuts and bolts are tight.
Monthly
1) Inspect air system for leaks by applying soapy water to all joints. Tighten those
joints if leakage is observed.
Initial oil change must be done after the first 100 hours
1) Once initial oil change is done after 100 hours of operation, change oil every 300
hours or 3 months, which ever comes first. See changing oil instructions.
2) Replace oil more often if used near paint spraying operations or in dusty
environments.
CHANGING OIL
To change oil, oil must be drained from the crankcase by removing oil drain bolt (A) Fig.11. Drain oil and replace oil drain bolt. To fill the
crankcase with oil, first unscrew and remove oil fill cap (B), pour air compressor oil (approx. 600
ml of SAE 30 weight non-detergent oil) into oil
opening until the oil level reaches the red dot at the centre of the oil sight glass (C). Reinstall the fill cap (B).
KEEP COMPRESSOR CLEAN
Periodically blow out all air passages with dry compressed air. Clean all parts with a soft damp cloth.
CAUTION
: Wear safety glasses while
using compressed air.
REPLACING/TENSIONING DRIVE BELT
If the drive belt needs tensioning, the belt should be adjusted so when pressure
is applied in the centre, there is approximately 1/2” slack. See Fig.12.
1) To install a new belt, remove the outer belt guard by removing the 6 hex. bolts
that secure it. Loosen motor mount bolts and slide motor towards the pump,
remove belt.
2) Install proper replacement belt, slide motor away from pump to provide
recommended tension, align pulleys and fasten motor mount bolts.
3) Reinstall belt guard. Belt tension should be checked after 20 hours of
operation. Check belt tension monthly thereafter.
FIGURE 11
FIGURE 12