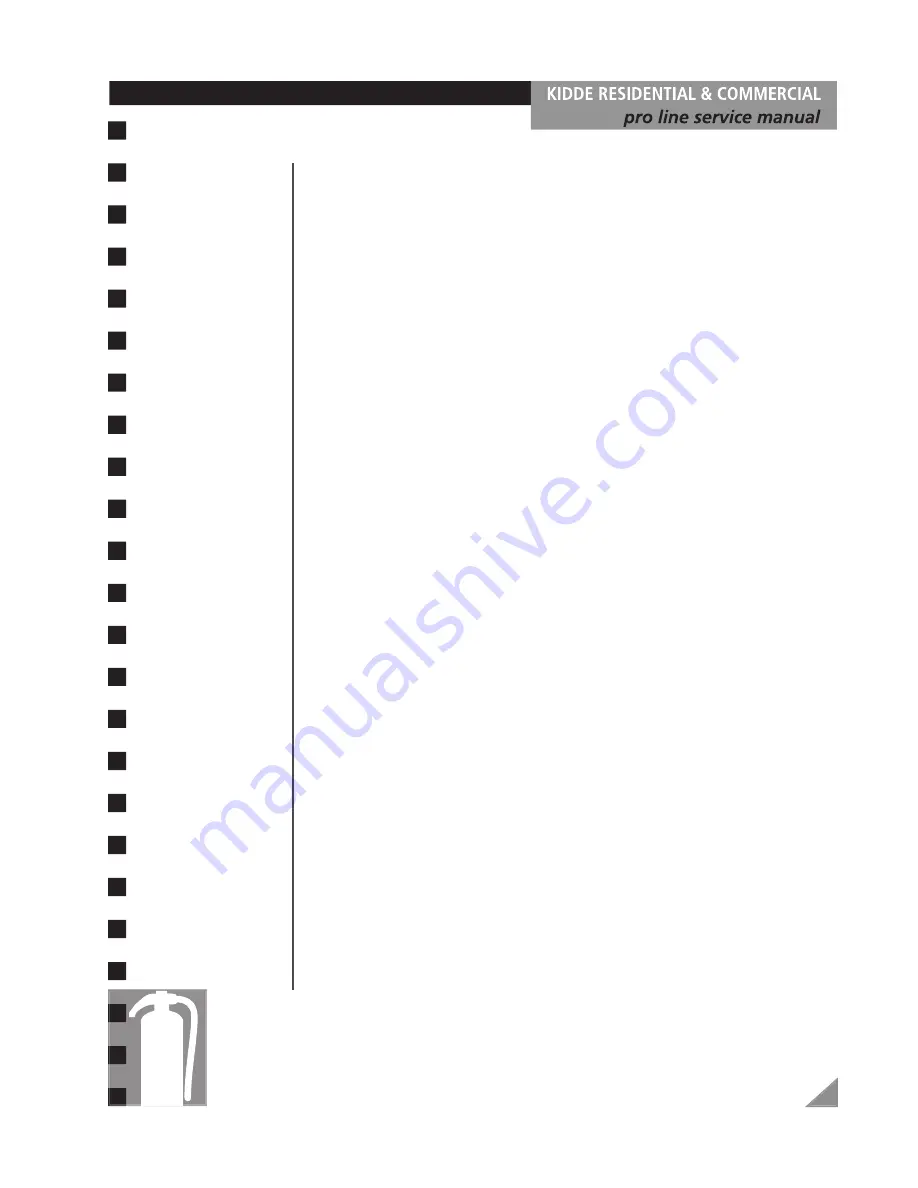
Evidence of conditions such as exposure to fire or heat, thread damage,
thread wear, corrosion, cylinder repairs or physical damage as detailed
within NFPA-10 require the extinguisher cylinder to be removed from
service and proper disposal at the owner’s direction.
Hydrostatic testing should only be performed by those persons trained
in the appropriate testing procedures/safeguards and having the proper
testing equipment, facilities and information.
Some Kidde hydrostatic test recommendations:
• Extinguisher cylinders should be replaced any time the pressure vessel
has been weakened due to corrosion, cuts, dents, digs, etc.
• That only water be used as the test medium and that the extinguisher
then be flushed clean, dried and visually re-examined after testing.
• The discharge valve assembly should be removed prior to hydrostatic
testing of the cylinder. (Refer to Note in Step 5 of Recharge
instructions.)
• The agent cylinder hydrostatic test marking method should only
utilize the proper type of record labels per NFPA-10 requirements.
• Never stamp or etch any markings onto the cylinder.
• Any time a fire extinguisher is known to have contained agents,
additives or mediums other than that specified on the nameplate, it
should be removed from service and properly disposed at the owner’s
direction.
• No repairs to the cylinder are permitted. If such cylinder repairs are
observed, the extinguisher should be removed from service and
properly disposed at the owner’s direction.
Hydrostatic Re-Test Data:
Component Description
Periodic Test Interval
Test Pressure
Agent cylinders
12 year
585 PSI
11