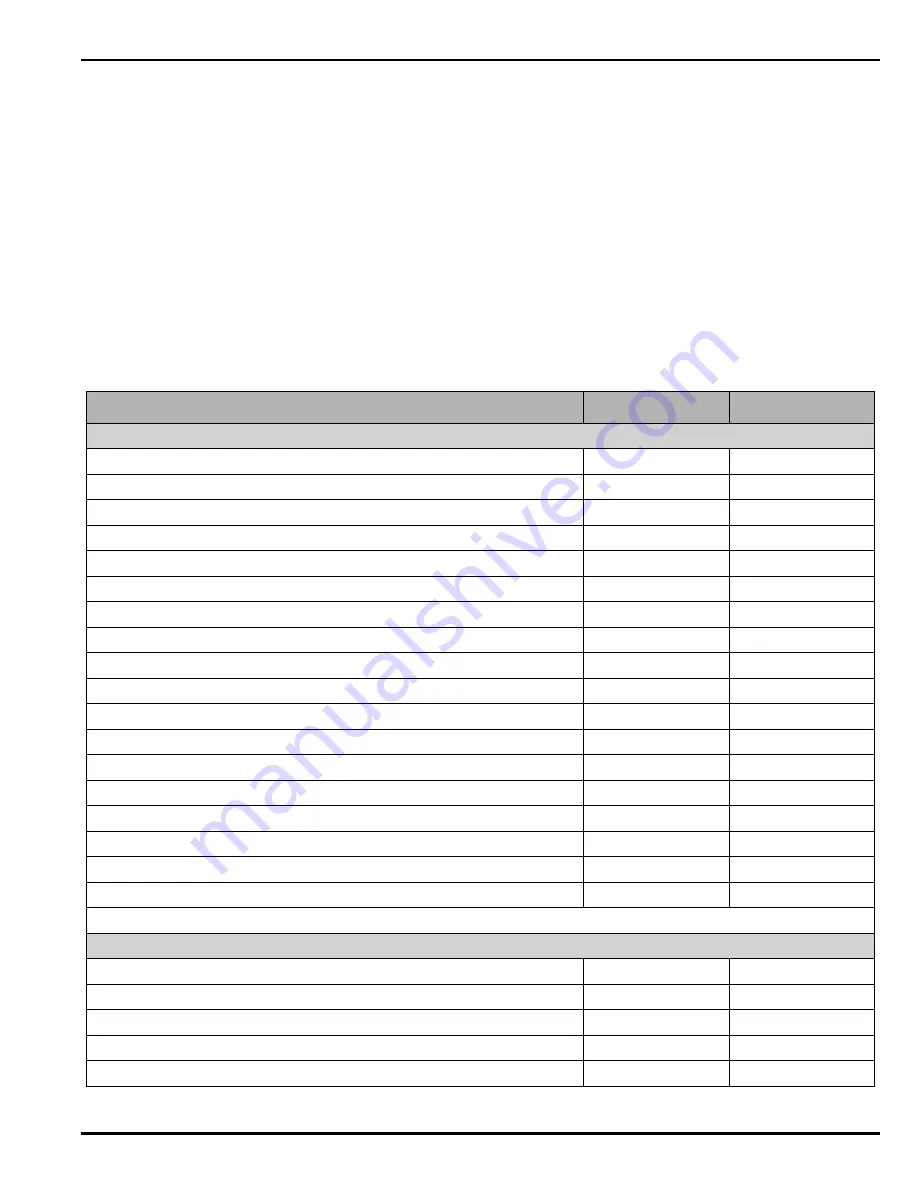
Parts List
06-236115-001
7-1
October 2014
CHAPTER 7
PARTS LIST
7-1
INTRODUCTION AND PARTS LIST
The table below, and on the following pages, provides a complete list of the Kidde Fire Systems
ECS Fire Suppression System with HFC-227ea Agent parts and associated system equipment.
Equipment can be ordered as complete assemblies or as individual items. In most situations,
when ordering a system, it will be easier and more cost effective to order by assembly part
numbers.
Note: Unless otherwise noted, the parts documented in this section are UL Listed and FM Ap-
proved. For non-agency approved parts, see datasheet K-90-2075.
Table 7-1. Parts List
Nomenclature
Part Number
Original P/N
Cylinder/Valve Assemblies
10 lb STD
90-100010-001
20 lb STD
90-100020-001
40 lb STD
90-100040-001
70 lb STD
90-100070-001
125 lb STD
90-100125-001
125 lb W/LLI
90-100121-001
200 lb STD Old Style Hemispherical Head before 3/98
90-100200-001
200 lb W/LLI Old Style Hemispherical Head before 3/98
90-100201-001
200 lb STD New Style Ellipsoidal Head after 3/98
90-100200-101
200 lb W/LLI New Style Ellipsoidal Head after 3/98
90-100201-101
350 lb STD
90-100350-001
350 lb W/LLI
90-100351-001
600 lb STD old style supplied before 9/01 (discontinued)
90-100600-001
600 lb W/LLI old style supplied before 9/01 (discontinued)
90-100601-001
600 lb STD new style supplied after 9/01
90-100600-100
600 lb W/LLI new style supplied after 9/01
90-100601-100
900 lb STD
90-100900-001
900 lb W/LLI
90-100901-001
(STD=Standard Cylinder Assembly, W/LLI=Cylinder with liquid level indicator)
Flexible Discharge Hoses
10-125 lb Cylinders
WK-283898-000
283898
200-350 lb Cylinders
WK-283899-000
283899
600 lb Cylinders (old style supplied before 9/01)
WK-283900-000
283900
600 lb Cylinders (new style after 9/01)
06-118225-001
900 lb Cylinders
06-118225-001
Summary of Contents for ECS
Page 3: ......
Page 9: ...THIS PAGE INTENTIONALLY LEFT BLANK October 2014 vi 06 236115 001 ...
Page 19: ...October 2014 xvi 06 236115 001 THIS PAGE INTENTIONALLY LEFT BLANK ...
Page 25: ...October 2014 1 6 06 236115 001 THIS PAGE INTENTIONALLY LEFT BLANK ...
Page 63: ...Component Description October 2014 3 36 06 236115 001 THIS PAGE INTENTIONALLY LEFT BLANK ...
Page 103: ...Design and Installation October 2014 4 40 06 236115 001 THIS PAGE INTENTIONALLY LEFT BLANK ...
Page 137: ...Post Discharge Maintenance October 2014 6 18 06 236115 001 THIS PAGE INTENTIONALLY LEFT BLANK ...
Page 148: ...P N 06 236115 001 A 1 October 2014 APPENDIX A MATERIAL SAFETY DATASHEETS ...
Page 167: ...October 2014 A 2 P N 06 236115 001 THIS PAGE INTENTIONALLY LEFT BLANK ...
Page 168: ......
Page 171: ......
Page 173: ...July 2016 ii 06 236115 003 THIS PAGE INTENTIONALLY LEFT BLANK ...
Page 186: ......
Page 189: ......
Page 191: ...August 2016 ii 06 237553 001 THIS PAGE INTENTIONALLY LEFT BLANK ...
Page 198: ......
Page 201: ......
Page 203: ...May 2016 ii 06 236115 004 THIS PAGE INTENTIONALLY LEFT BLANK ...
Page 211: ...May 2016 8 06 236115 004 THIS PAGE INTENTIONALLY LEFT BLANK ...
Page 212: ......