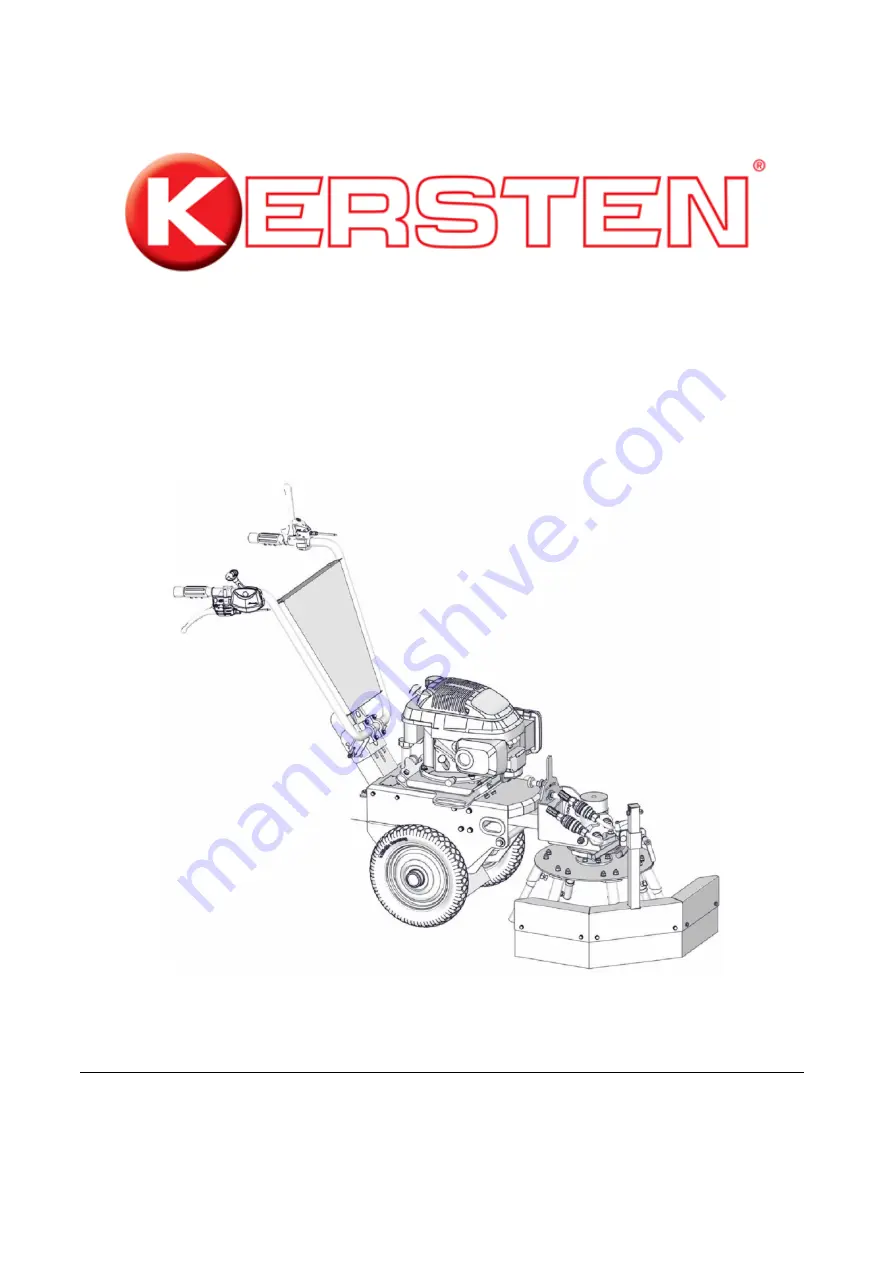
Pos: 2 / Anleitungen / Bookmark / Kersten front page language-independent area @ 15 \ mod_1549625959450_6.docx @ 257678 @ @ 1
Original operating instructions
Single-axis weed brush Weedo II
Pos: 3 / Anleitungen / Bookmark / Kersten front page language-dependent area @ 15 \ mod_1549625757522_6.docx @ 257657 @ @ 1
=== End of list for bookmark title page ===
Order number:B00100
from machine no .:62954
Rev .: R00
Was standing:
2019-03-01
Summary of Contents for Weedo II
Page 2: ...DE 2019 03 01 2 79...