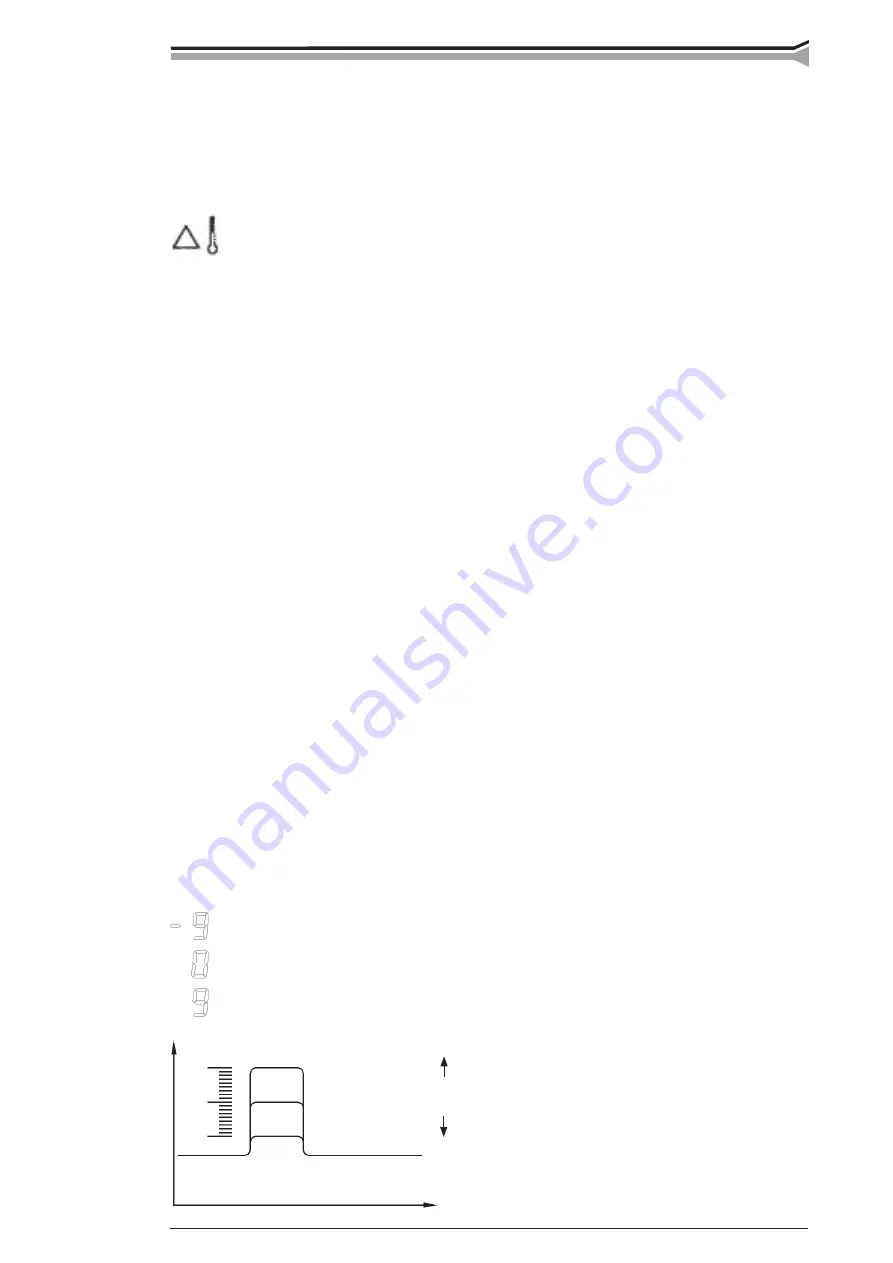
Kemppi pro evolution 300, 400, 500, 300 mvu, 400 mvu, 500 mvu / 0617 –
© Kemppi oy
0 =
9
-9
0
t
I
2
3.2. pIlot lamps
The pilot lamps of the machine report the electric operation:
The green pilot lamp H11 when lit indicates that the machine is on and ready for use and it
is connected to the mains supply with the main switch in the I-position.
H12 indicates when lit that the thermal protection of the machine has been activated due
to over heating. The cooling fan will continue to run and cool the machine down and when
the lamp is off the machine ia ready to weld.
3.3. local or remote control of weldIng current
You can control welding current either from local controls of PX or PL control panel, or from
remote control unit which is connected to remote control connector X14 or X15, or from Promig
or Protig unit.
Selector switch of control panel has to be in a position corresponding to control mode: local
control / MIG/TIG / remote control unit.
Suitable remote control units R10 and R20, see page 5.
At MIG and TIG welding, current control is made according to operation instruction of control
-
ling MIG or TIG unit.
3.4. operatIon of coolIng fan
In Kemppi Pro Evolution 3200 there is one and in 4200 and 5200 there are two simultaneously
operating fans.
- The fan is started for a moment when main switch is placed into postion I.
- The fan will start during welding as the machine heats up and it will run for 1 to 10 minutes
after the welding has stopped.
- On no-load fan is started in intervals of approx. half an hour for minute’s time.
Soft arc. Object to reduce amount of spatter in welding at the upper end of recommen
-
ded currents for electrode.
Factory setup (PX). Normal setting for all electrode types.
Rough arc. Object e.g. cellulose covered electrodes and thin stainless electrode in
welding at the lower end of the recommended curents for electrode.
Roughening
Factory setup
Softening
4. accessorIes
4.1. pl and pX control panels’ operatIon In
mma weldIng
4.1.1. Control for MMA welding dynamics (PL, PX)
With control for electrode dynamics you can influence arc behaviour in different kinds of opera
-
tion situations.
When arc is roughened, blowing is increasing and at the same time also spatter.