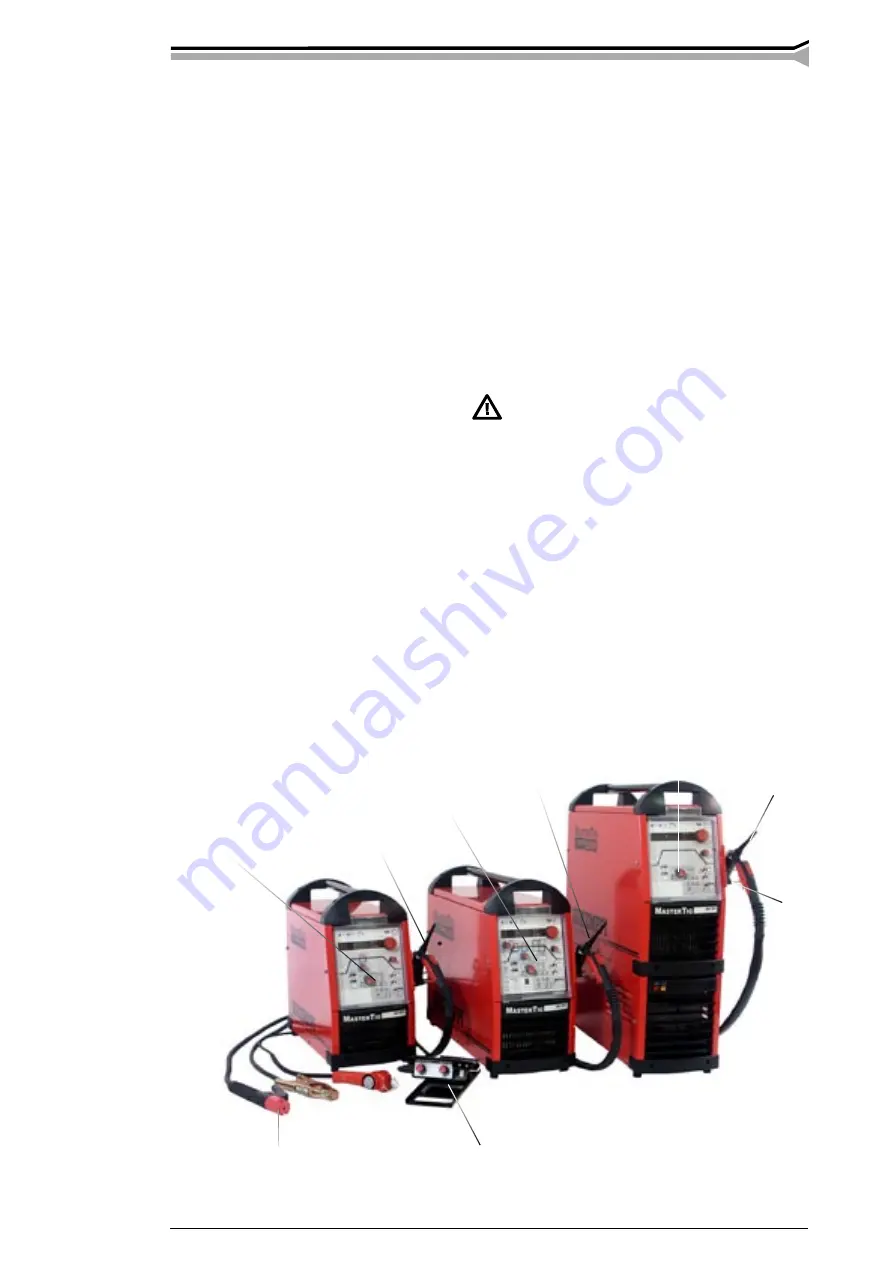
Mastertig AC/DC 2000, 2500, 2500W, 3500W/0510 – 3
©
COPYRIGHT
KEMPPI
OY
GH 20
C 100AC
C 100F
ACDC minilog
ACDC pulse
ACDC panel
TTK 160
TTK 220
TTK 350W
1. PREFACE
1.1. INTRODUCTION
Congratulations on having purchased this product. Properly installed Kemppi products should
prove to be productive machines requiring maintenance at only regular intervals. This manual
is arranged to give you a good understanding of the equipment and its safe operation. It also
contains maintenance information and technical specifications. Read this manual from front to
back before installing, operating or maintaining the equipment for the first time. For further
information on Kemppi products please contact us or your nearest Kemppi distributor.
The specifications and designs presented in this manual are subject to change without prior
notice.
In this document, for danger to life or injury the following symbol is used:
Read the warning texts carefully and follow the instructions. Please also study the Operation
safety instructions and respect them when installing, operating and servicing the machine.
1.2. PRODUCT INTRODUCTION
Mastertig AC/DC is a power source for TIG /MMA welding suitable for AC and DC welding
and designed for demanding professional use. The power source is an inverter, which is formed
with IGB transistors. The power source is available in three sizes, 200 A, 250 A and 350 A. The
250 A power source comes in two separate versions for gas-cooled torches and for water-cooled
torches. Three different exchangeable panel versions are available for the power source: a basic
panel, a minilog panel and a pulse panel.
Summary of Contents for MASTERTIG AC/DC 2000
Page 31: ......