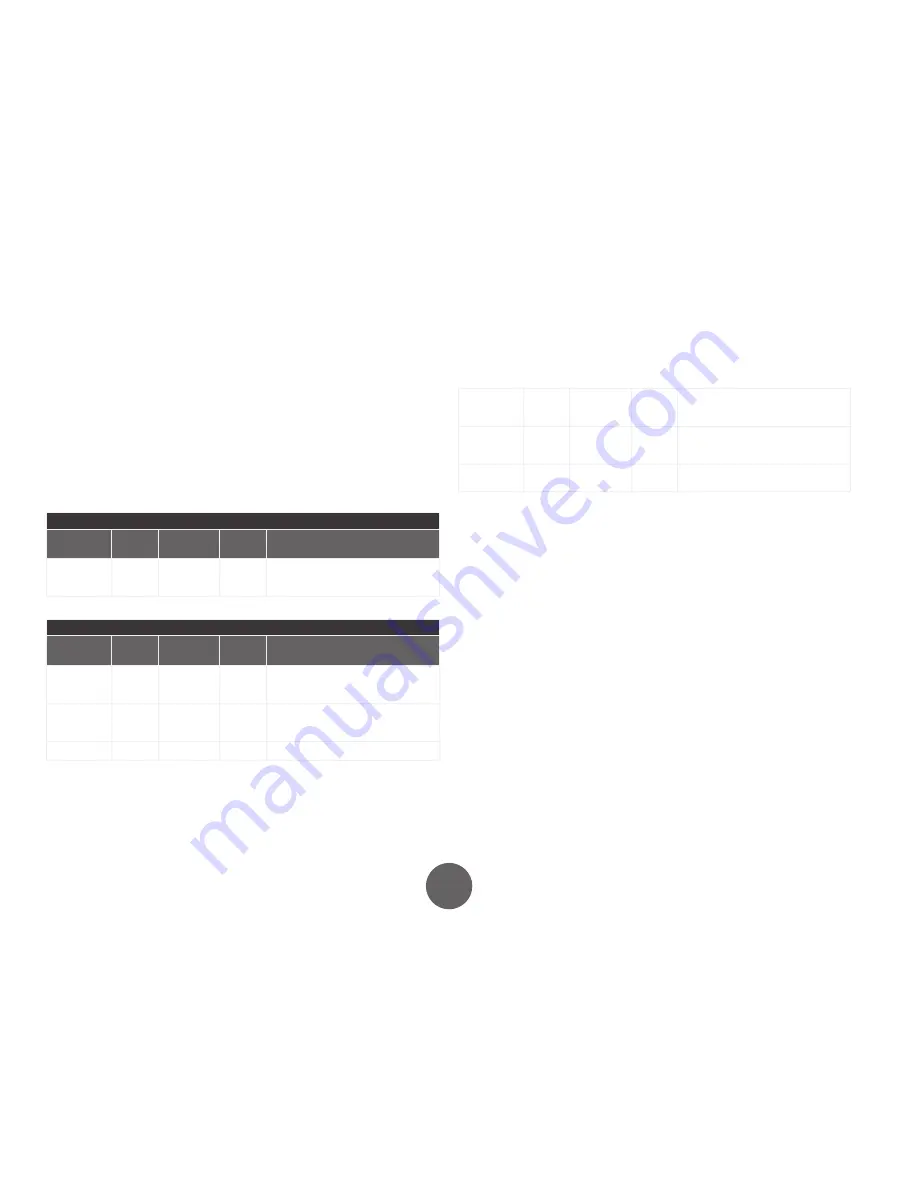
20
A3 MIG Welder
© Kemppi Oy 2018
1826
OPERA
TING M
ANU
AL
4.7 Welding and system setup
Quick setup
To set the values of the functional parameters for MIG features, use the QUICK SETUP
feature, which you can activate by briefly pressing the SETUP button (5).
Select the parameter to adjust using the left-hand side control knob or the button (8)
and then set the parameter value with the right-hand side control knob. The value you
specified is instantly stored in the control panel memory. The following tables list the
parameter values that can be specified for the MIG features.
QUICK SETUP, MIG
Parameter
Display
Value range Factory
setting
Description
Creep start
level
Cre
10 ... 170 %
50 %
Percent of wire feed speed default
10% refers to slow start,
170% refers to fast start
QUICK SETUP, 1-MIG, WiseThin, WiseRoot
Parameter
Display
Value range Factory
setting
Description
Creep start
level
Cre
10 ... 170 %
50 %
Percent of wire feed speed default
10% refers to slow start,
170% refers to fast start
Hot start
level
Hot
-50 ... 75 %
30 %
Percent of welding power:
-50% refers to cold start
+75% refers to hot start
Hot start time
H2t
0 ... 9.9 s
1.2 s
The duration of the hot start in seconds.
Crater fill
start level
CrS
Crater fill
end level ...
250 %
90 %
The welding power at the beginning of
the crater fill stage as a percentage of
the welding power pre-set value.
Crater fill end
level
CrL
10 ... Crater
fill start level
30 %
The welding power at the end of the
crater fill stage as a percentage of the
welding power pre-set value.
Crater fill
time
Crt
0 ... 9.9 s
2 s
The duration of the crater fill stage in
seconds.
All setup parameters
The machine has several parameters, whose settings can be specified with the control
panel's SETUP function as follows:
1. Press and hold down the SETUP button (5) for at least 5 seconds.
2. Select the parameter to adjust using the left-hand side control knob. The parameter
name is shown in display left-hand display.
3. Specify the parameter value with the right-hand side control knob. The selected
value is shown in the right-hand display. The parameter’s value is immediately
stored in the memory.
4. Exit the SETUP mode by pressing and holding down the SETUP button again for at
least 5 seconds or by briefly pressing the ESC button.
All welding processes have their own setup parameters. For example, adjusting the post-
current for synergic MIG welding does not affect the post-current of normal MIG weld-
ing.
The tables below show the features available in this welding machine and their possible
values.