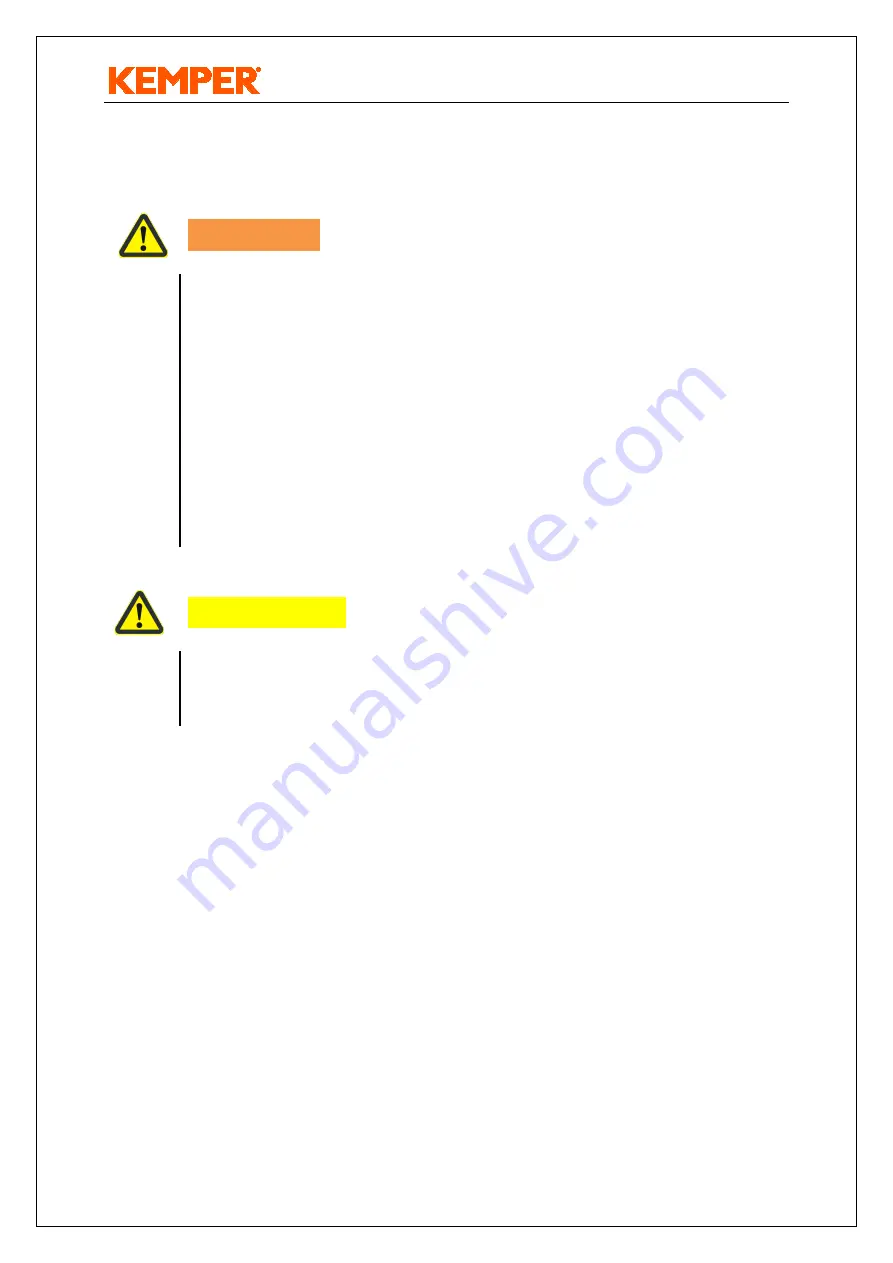
KEMPER ProfiMaster Manual
EN
Art. No.: 150 2121
- 27 -
Rev.:
1
Subject to technical modifications and errors.
Issued: 10/2013
8. Disposal
WARNING
Skin contact with cutting smoke, etc. can lead to skin irritation for
people with sensitive skin!
Dismantling work on the ProfiMasters may only be carried out by
trained and authorized personnel who observe the safety
instructions and applicable accident-prevention regulations!
Serious injury to the respiratory tract and respiratory organs
possible!
To avoid contact with and inhalation of dust, use protective
clothing, gloves and an air respirator!
The release of hazardous dust when cleaning is to be avoided, so
that people not charged with the task are not harmed.
TAKE CARE
Comply with the legal obligations regarding waste prevention and
proper recycling/disposal when working with the ProfiMaster!
8.1 Plastics
The plastics used must be sorted as far as possible.
Plastics must be disposed of in compliance with official regulations.
8.2 Metal
Various metals must be separated and disposed of. Disposal must be performed by
an authorized company.