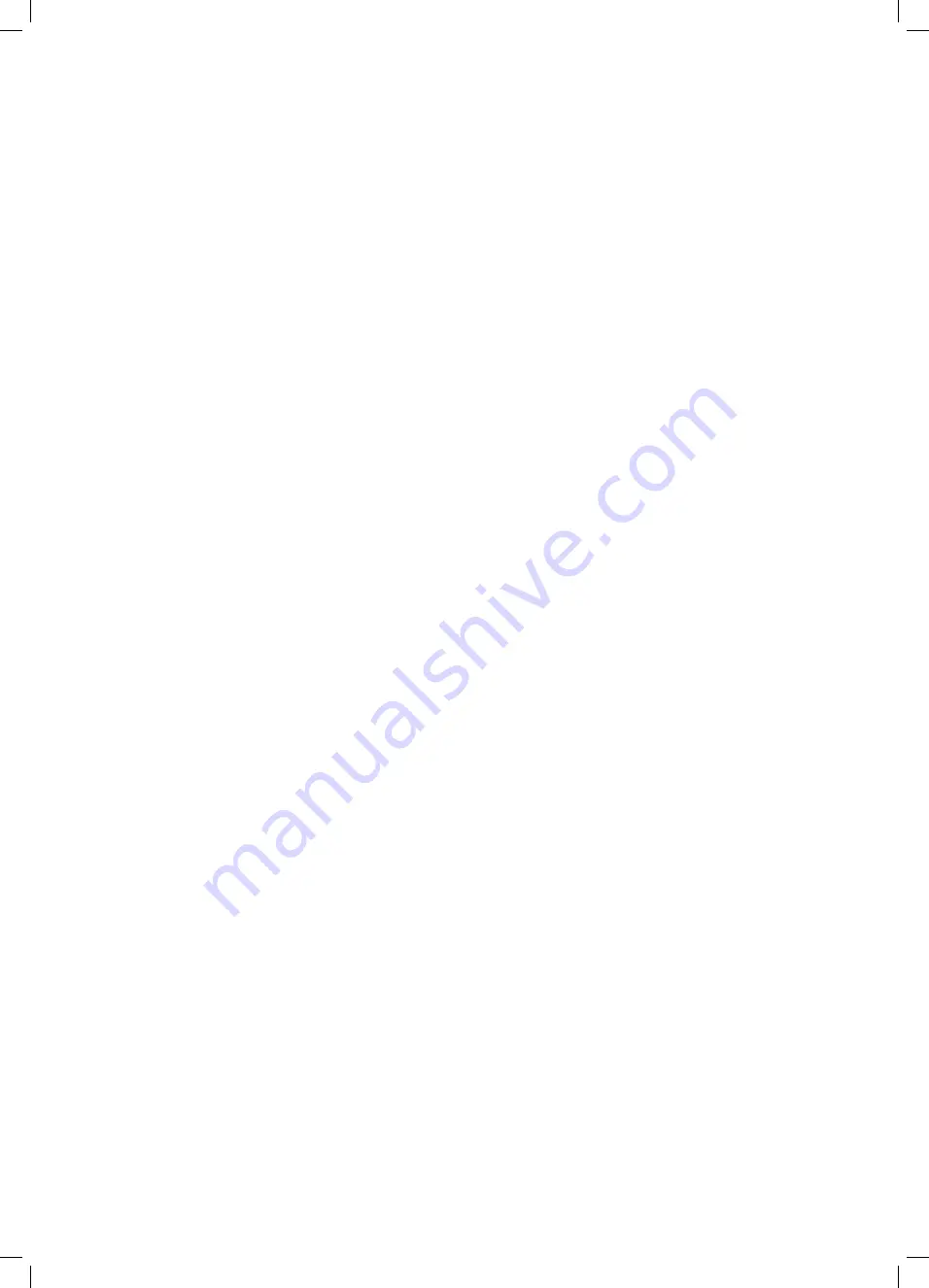
Kelvinator Air Conditioning
Information servicing 19
Information servicing
Repairs to sealed components
1. During repairs to sealed components, all electrical supplies
shall be disconnected from the equipment being worked upon
prior to any removal of sealed covers, etc. If it is absolutely
necessary to have an electrical supply to equipment during
servicing, then a permanently operating form of leak detection
shall be located at the most critical point to warn of a
potentially hazardous situation.
2. Particular attention shall be paid to the following to ensure that
by working on electrical components, the casing is not altered
in such a way that the level of protection is affected. This shall
include damage to cables, excessive number of connections,
terminals not made to original specification, damage to seals,
incorrect fitting of glands, etc.
•
Ensure that apparatus is mounted securely.
•
Ensure that seals or sealing materials have not degraded
such that they no longer serve the purpose of preventing the
ingress of flammable atmospheres. Replacement parts shall be
in accordance with the manufacturer's specifications.
NOTE: The use of silicon sealant may inhibit the effectiveness
of some types of leak detection equipment. Intrinsically safe
components do not have to be isolated prior to working on them.
Repair to intrinsically safe components
Do not apply any permanent inductive or capacitance loads to the
circuit without ensuring that this will not exceed the permissible
voltage and current permitted for the equipment in use. Intrinsically
safe components are the only types that can be worked on while
live in the presence of a flammable atmosphere. The test apparatus
shall be at the correct rating. Replace components only with parts
specified by the manufacturer. Other parts may result in the ignition
of refrigerant in the atmosphere from a leak.
Cabling
Check that cabling will not be subject to wear, corrosion,
excessive pressure, vibration, sharp edges or any other adverse
environmental effects. The check shall also take into account
the effects of aging or continual vibration from sources such as
compressors or fans.
Leak detection methods
The following leak detection methods are deemed acceptable
for systems containing flammable refrigerants. Electronic leak
detectors shall be used to detect flammable refrigerants, but
the sensitivity may not be adequate, or may need re-calibration.
(Detection equipment shall be calibrated in a refrigerant-free
area.) Ensure that the detector is not a potential source of ignition
and is suitable for the refrigerant used. Leak detection equipment
shall be set at a percentage of the LFL of the refrigerant and shall
be calibrated to the refrigerant employed and the appropriate
percentage of gas (25 % maximum) is confirmed. Leak detection
fluids are suitable for use with most refrigerants but the use of
detergents containing chlorine shall be avoided as the chlorine
may react with the refrigerant and corrode the copper pipe-
work. If a leak is suspected, all naked flames shall be removed or
extinguished. If a leakage of refrigerant is found which requires
brazing, all of the refrigerant shall be recovered from the system, or
isolated (by means of shut off valves) in a part of the system remote
from the leak. Oxygen free nitrogen (OFN) shall then be purged
through the system both before and during the brazing process.
Removal and evacuation
When breaking into the refrigerant circuit to make repairs or for any
other purpose conventional procedures shall be used. However,
it is important that best practice is followed since flammability is a
consideration. The following procedure shall be adhered to
•
Remove refrigerant;
•
Purge the circuit with inert gas;
•
Evacuate;
•
Purge again with inert gas;
•
Open the circuit by cutting or brazing.
The refrigerant charge shall be recovered into the correct recovery
cylinders. The system shall be flushed with OFN to render the
unit safe. This process may need to be repeated several times.
Compressed air or oxygen shall not be used for this task. Flushing
shall be achieved by breaking the vacuum in the system with OFN
and continuing to fill until the working pressure is achieved, then
venting to atmosphere, and finally pulling down to a vacuum. This
process shall be repeated until no refrigerant is within the system.
When the final OFN charge is used, the system shall be vented
down to atmospheric pressure to enable work to take place. This
operation is absolutely vital if brazing operations on the pipe-work
are to take place. Ensure that the outlet for the vacuum pump is not
close to any ignition sources and there is ventilation available.