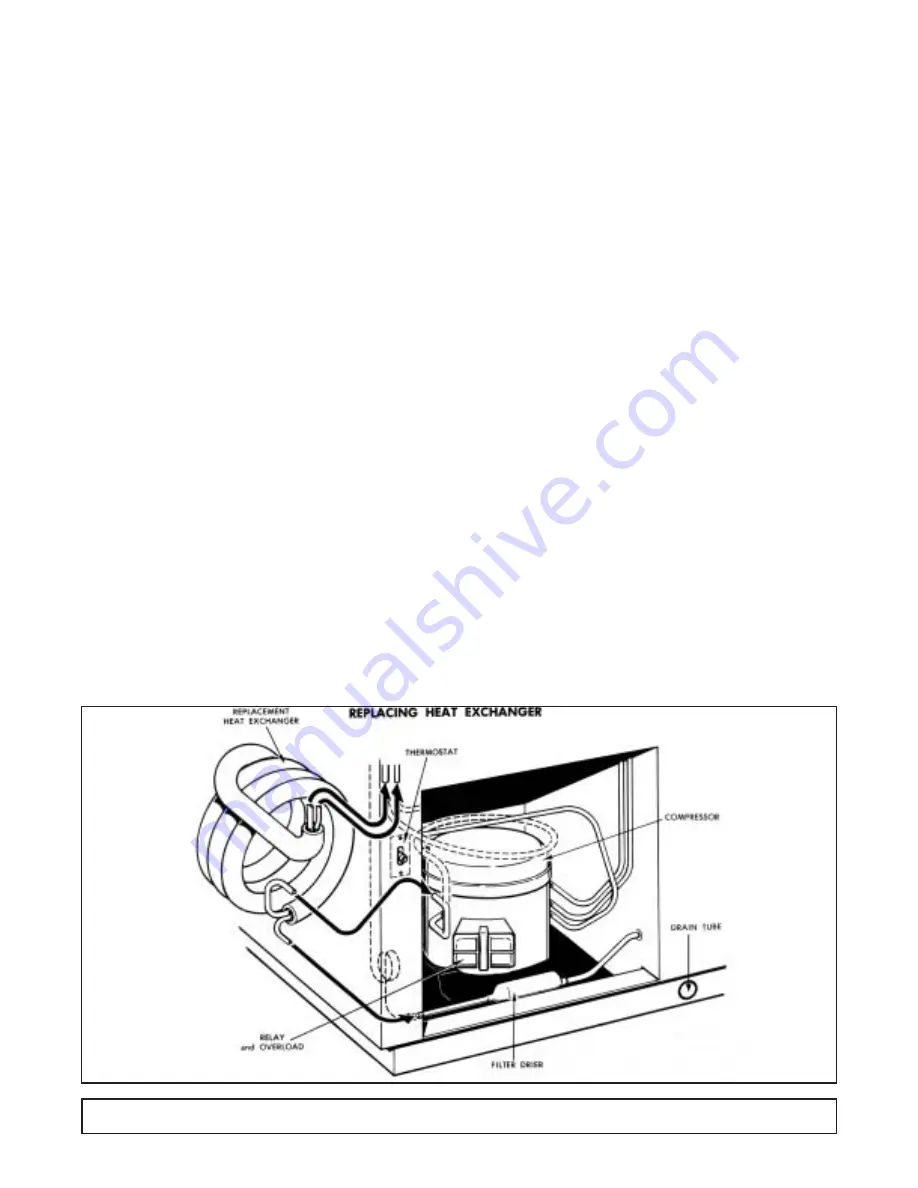
12
GENERAL OPERATIONS
cabinet in a warm room the wrapper will be warm to
the touch. This is a normal condition with this type of
condenser.
The wrapper type condenser is free of many of the faults
common to the conventional type system. Because of
the design there are no fans to fail; no fins to clog with
grease, lint or dust causing high condensing tempera-
tures. The condensing temperatures compare very
favorably with other types and the system has the added
advantage that condenser efficiency is constant
throughout the life of the cabinet.
FILTER DRIER
A filter drier’s purpose is to filter and trap minute parti-
cles of foreign materials and absorb any moisture which
may be in the system.
The drier is located in the liquid line ahead of the capill-
ary tube. A fine mesh screen filters out foreign particles
and the desiccant absorbs the moisture.
REPLACING THE FILTER DRIER
1. Disconnect the cabinet from its power source.
2. Install a tap line service valve to both the high and low
side process tubes.
3. Attach a compound gauge manifold to system.
4. Hook up refrigerant reclaimer to system and remove
all refrigerant from cabinet.
5. Remove drier from system.
6. Replace with same part number. Changing drier
size will effect the system charge.
7. Evacuate system to 500 microns.
8. Refer to cabinet data plate for proper charge and type
of refrigerant used.
CAPILLARY TUBE
A capillary tube is used to regulate the flow of liquid
refrigerant into the low side of the system. Its resistance
or pressure drop due to the length of tube and smaller
diameter, meters the flow of the refrigerant.
HEAT EXCHANGER
The liquid and suction lines are soldered together to
form an efficient heat exchanger. The warm liquid refrig-
erant is sub-cooled by the cold suction vapor prior to
entering the low side. The heat exchanger is located in
the area above the compressor
REPLACING THE HEAT EXCHANGER
1. Disconnect the cabinet from the power source.
2. Install service tops to process tube on high and low
sides of system.
3. Attach a manifold gauge set.
4. Reclaim all refrigerant in cabinet.
5. Remove cork impregnated tape from refrigerant
lines at bottom of cabinet.
6. Disconnect heat exchanger suction line from low
side outlet line.
7. Disconnect the capillary line from the low side inlet
line.
8. Place replacement heat exchanger in position and
connect the lines.
9. Replace the filter drier.
10. Evacuate system below 500 microns.
11. Refer to cabinet data plate for charge and type of
refrigerant. After charging, pinch off service taps and
braze tube closed.