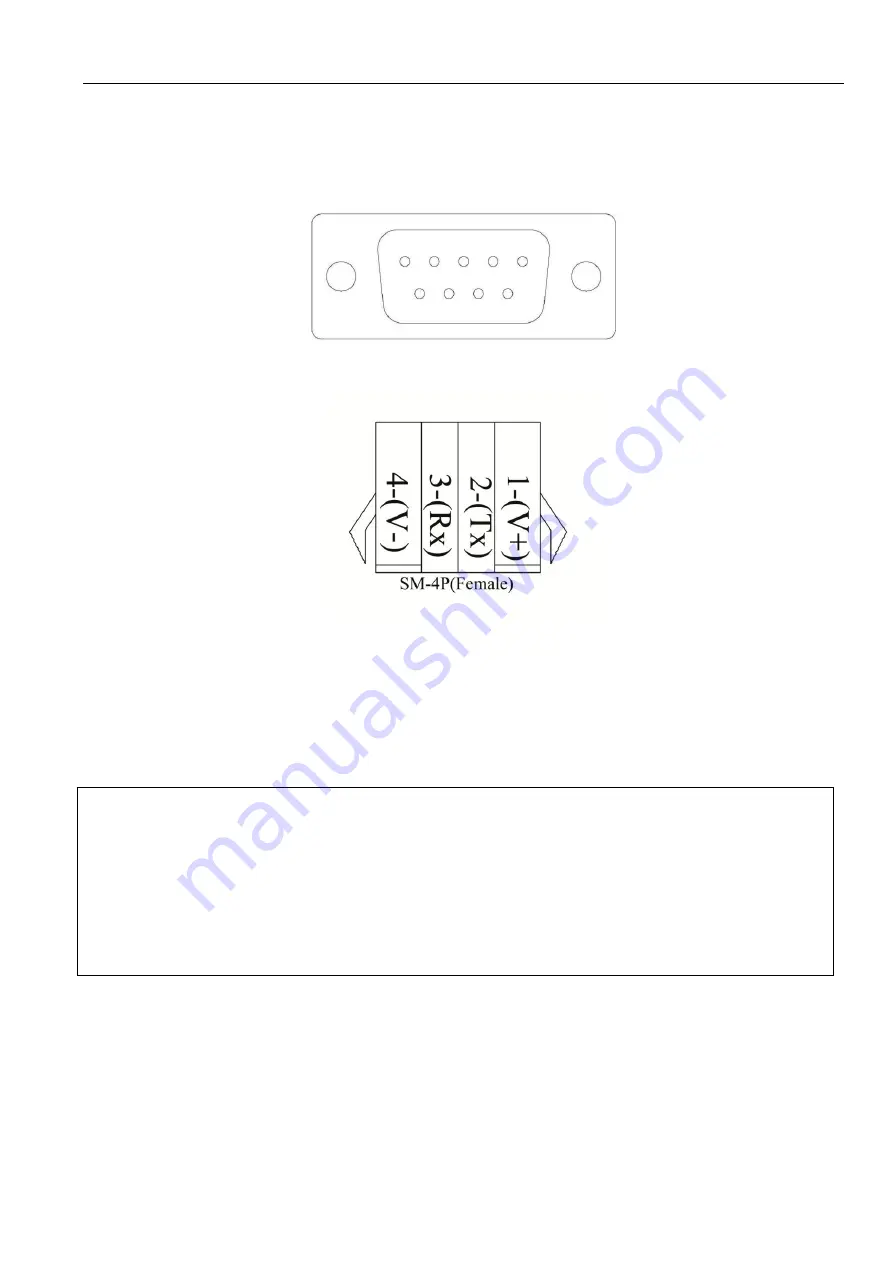
Kelly KLS8080N/NPS Sinusoidal Brushless Motor Controller User
’s Manual
V 1.10
12
3.2.4 Communication Port
A 4pin connector to RS232 port is provided to communicate with host computer for calibration and
configuration.
Figure 8:
RS232 Interface on 4pin connector to RS232 converter
Figure 9
:
SM-4P connector for communication interface on KLS8080N controller
3.3 Installation Check List
Before operating the vehicle, complete the following checkout procedure. Use LED code as
a reference as listed in Table 1.
Caution:
•
Put the vehicle up on blocks to get the drive wheels off the ground before beginning these
tests.
•
Do not allow anyone to stand directly in front of or behind the vehicle during the checkout.
•
Make sure the PWR switch and the brake is off
•
Use well-insulated tools.
•
Prohibit trying to connect the controller to user program while the motor is still running,let
alone change the settings in the user program.