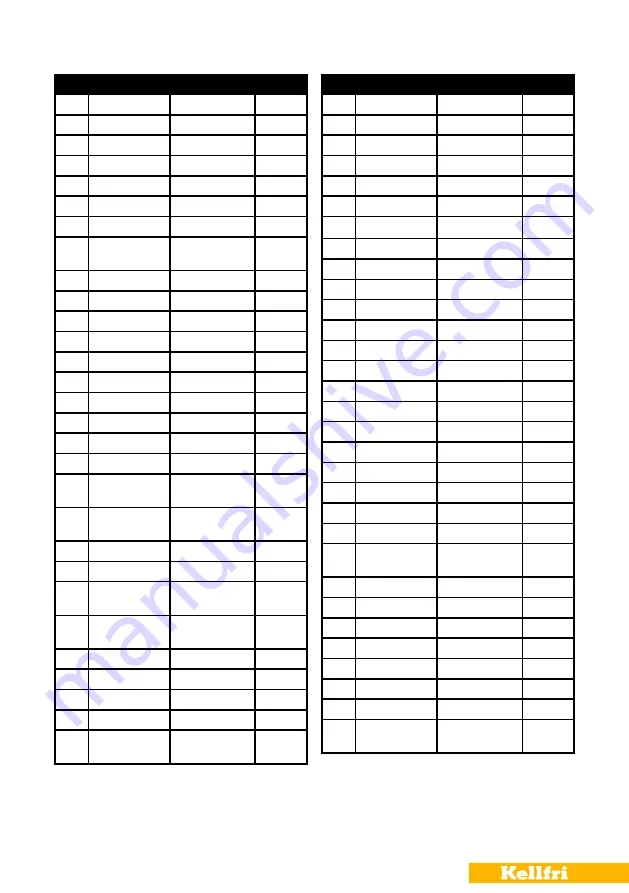
21
Item Spare part no. Designation
Quantity
1
R35-HRT160.001
M12 x 60 bolt
2
2
R35-HRT160.002
Hydraulic motor
1
3
R35-HRT160.003
Hydraulic coupling
2
4
R35-HRT160.004
Nut M12
10
5
R35-HRT160.005
Washer
2
6
R35-HRT160.006
Lower beam bracket
1
7
R35-HRT160.007
M12x45 bolt
4
8
R35-HRT160.008
Complete engine
mount
2
9
R35-HRT160.009
M12x45 bolt
6
10
R35-HRT160.010
Crank disc
1
11
R35-HRT160.011
Lock washer
1
12
R35-HRT160.012
Connecting rod bolt
1
13
R35-HRT160.013
O-ring 20
1
14
R35-HRT160.014
Side guard
1
15
R35-HRT160.015
Bolt M10x30
16
16
R35-HRT160.016
Bolt M10x35
10
17
R35-HRT160.017
Cutterbar fingers
11
18
R35-HRT160.018
Nut M10
32
19
R35-HRT160.019
Reinforcement plate
– side
2
20
R35-HRT160.020
Reinforcement plate
– outer
1
21
R35-HRT160.021
Bolt M10x25
10
22
R35-HRT160.022
Cutterbar
1
23
R35-HRT160.023
Blade beam base
plate
5
24
R35-HRT160.024
Attachment plate
blade beam
5
25
R35-HRT160.025
Washer 10
28
26
R35-HRT160.026
Cutterbar holder
1
27
R35-HRT160.027
Hinge pin
1
28
R35-HRT160.028
Washer 16
8
29
R35-HRT160.029
Complete swivel
arm kit
1
Item Spare part no. Designation
Quantity
30
R35-HRT160.030
Nut M12
1
31
R35-HRT160.031
Bearing 6009
1
32
R35-HRT160.032
Clamp ring 45
1
33
R35-HRT160.033
Bearing housing
1
34
R35-HRT160.034
Clamp ring 75
1
35
R35-HRT160.035
Washer 12
16
36
R35-HRT160.036
Nut M14
5
37
R35-HRT160.037
Washer 14
9
38
R35-HRT160.038
Top beam bracket
1
39
R35-HRT160.039
Spacer
1
40
R35-HRT160.040
Bolt M14x40
4
41
R35-HRT160.041
Bolt M8 x 25
6
42
R35-HRT160.042
Spring washer 8
17
43
R35-HRT160.043
Washer 8
12
44
R35-HRT160.044
Bearing housing
1
45
R35-HRT160.045
Bearing 6004
1
46
R35-HRT160.046
Bearing support arm
1
47
R35-HRT160.047
Nut M10
2
48
R35-HRT160.048
Spring washer 10
6
49
R35-HRT160.049
Swivel arm
1
50
R35-HRT160.050
Screw M10x35
2
51
R35-HRT160.051
Bolt M8x30
4
52
R35-HRT160.052
Swivel arm holder
beam
1
53
R35-HRT160.053
Side plate
2
54
R35-HRT160.054
Spring arm
1
55
R35-HRT160.055
Flange
2
56
R35-HRT160.056
Nut M16
1
57
R35-HRT160.057
Nut M16
1
58
R35-HRT160.058
Bushing 18×16×10
1
59
R35-HRT160.059
Nut M8
4
60
R35-HRT160.060
Hydraulic hose for
motor
2
FIGURE 1: CUTTING HEAD