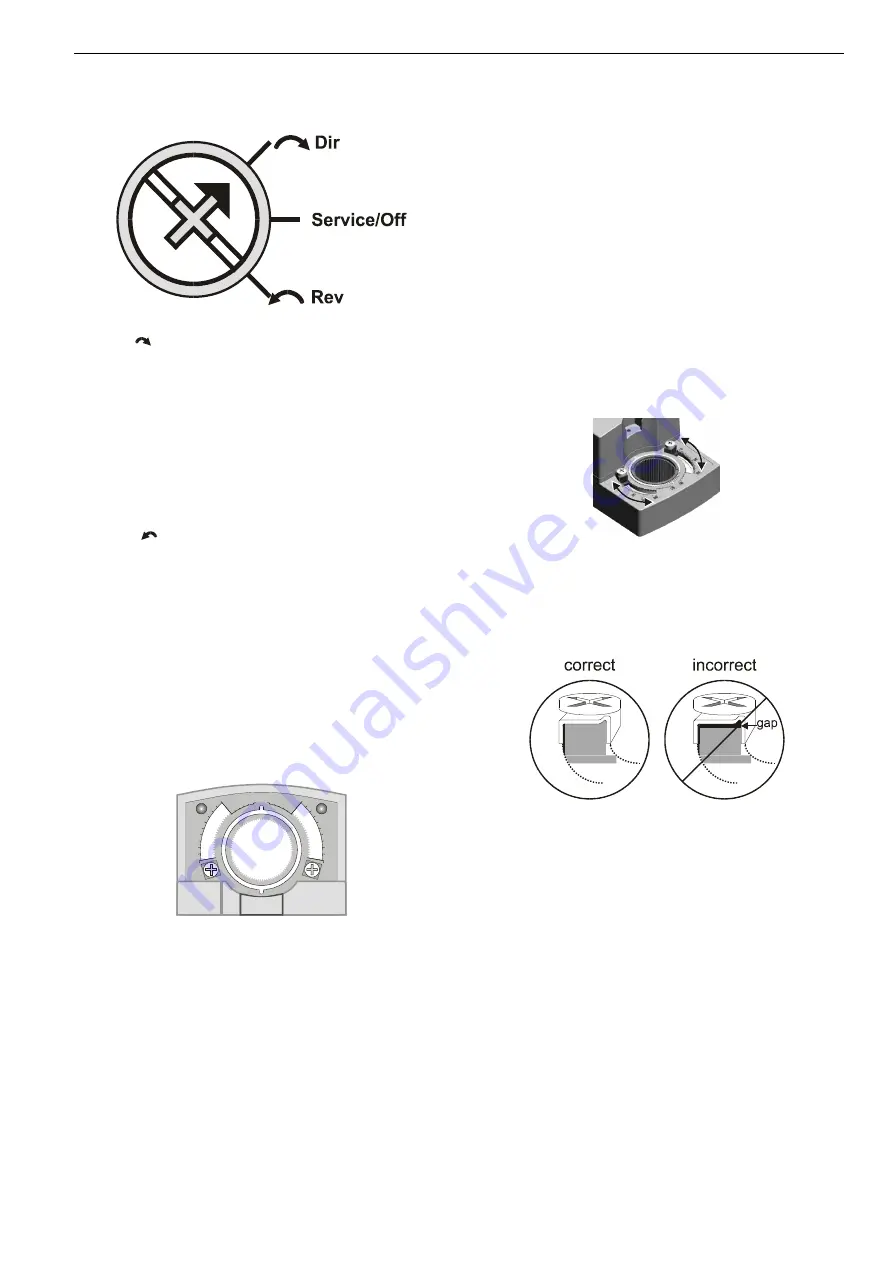
KA-175-2T, KA-301-2T
3
EN0B-0320GE51 R0903
Rotation Direction Switch
Fig. 3. Rotation Direction Switch
•
Dir
("
") is the default shipping position. When the
rotation direction switch is set to this position, the
actuator internally switches the rotation direction control
signals as stated in section "Wiring Diagrams" on pages
Fehler! Textmarke nicht definiert.
•
"
Service/Off
": When the rotation direction switch is set
to this position, all actuator rotary movement is cancelled
and all control signals are ignored, thus enabling the
actuator to be manually operated (see section "Manual
Adjustment"). The user can then perform maintenance /
commissioning without having to remove power from the
actuator. To return to the control mode, simply move the
rotation direction switch to its former setting.
•
Rev
("
"): When the rotation direction switch is set to
this position, the actuator follows signals as stated in
section "Wiring Diagrams" on pages 5 and
Two-Position or Floating Control
The actuator is capable of being operated by either a two-
position (open/close) or a floating (three-wire) controller.
Refer to wiring diagrams for correct connection.
Position Indication
The hub adapter indicates the rotation angle position by
means of the rotational angle scales (0...90° / 90...0°)
provided in the actuator plate (see Fig. 4).
90 90
60
30
60
30
0
0
Fig. 4. Position indication
Manual Adjustment
IMPORTANT
To prevent equipment damage, you must remove
power or set the rotation direction switch to the
"Service/Off" position before manual adjustment.
After removing power or setting the rotation direction switch
to the "Service/Off" position, the gear train can be
disengaged using the declutch button, permitting the actuator
shaft to be manually rotated to any position. The feedback
signal will then follow the new position.
Limitation of Rotation Stroke
Two adjustable mechanical end limits (177 lb-in [20 Nm]
models, only) are provided to limit the angle of rotation as
Fig. 5. Mechanical end limits
The mechanical end limits must be securely fastened in
place as shown in Fig. 6. Specifically, it is important that they
properly mesh with the rotational angle scales when the
screws are tightened.
Fig. 6. Correct / incorrect tightening of end limits