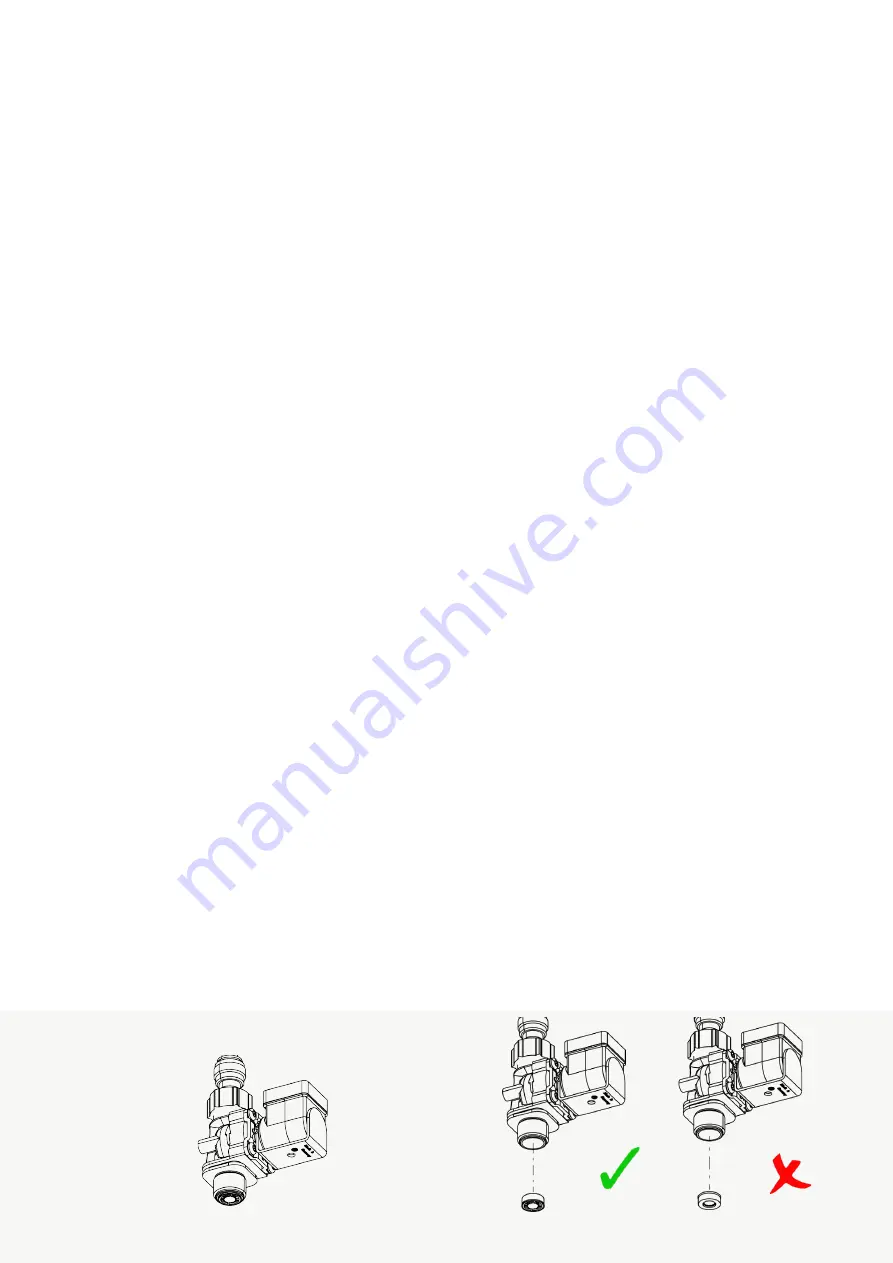
15
Kelda Showers products are designed for easy maintenance and should give continued superior and safe performance,
provided:
1.
Kelda Showers products are installed, commissioned, operated and maintained in accordance with this installation
guide.
2.
Periodic attention is given as necessary to maintain the product in good functional order.
Guidelines for frequency are given below. Maintenance must be carried out in accordance with these instructions, and
must be conducted by designated, qualified and competent personnel. Children are not to perform maintenance. Kelda
showers are built with the highest quality components which are designed for a long life, but due care must be taken
during maintenance to avoid damage.
Daily/Weekly Hygiene
External surfaces of the chrome plated showerhead wiped clean with soft cloth and a mild detergent. Take care not to
get detergents on to stainless steel. Stainless steel should be regularly cleaned with warm water and soft cloth, taking
care to remove any dirt and remnants of shampoo or soap. See "Stainless Steel Care" for more details.
Quarterly Hygiene*
Shower heads to be dismantled to clean, de-scale and sanitise main shower head components. Please see instructions
for dismantling and reassembling head for cleaning. Unlike a conventional showerhead a Kelda showerhead is highly
unlikely to block due to limescale and so service timings can set purely for hygiene.
*This service point can be adjusted to suit site specific maintenance regime and shower usage levels.
Bi-Annual Visual & Hygiene
Check internal component condition of the shower head and hoses. Inspect for debris, scale deposition, deformation,
damage, etc. Maintain or renew if necessary. Instructions for cleaning and disinfecting air hoses are given in this booklet.
Shut off water supply, check stop valves then remove and clear filters of debris. These may be located in thermostatic
mixer if an one is fitted.
If a mixer is fitted into panel then please follow maintenance guide which is specific to that model of mixer.
Stainless Steel Care
Stainless steel requires regular cleaning for to keep its anti-corrosion properties, this can be done just with a soft cloth
and warm water. Glass cleaner can be used to remove fingerprints (we advise you spot test the use of any cleaner first).
Chlorine, bleach, detergents, shampoos and soaps can all all strip stainless steel of its anti-corrosion properties and if left
uncleaned this can result in rust spotting. If you believe any of these substances have been in contact with the stainless
steel or if the panels need cleaning following a period of neglect, then use a stainless-steel cleaner – these are widely
available but stop test any cleaner first.
If cleaning has been missed and rust spotting has occurred, then vigorous cleaning with stainless-steel cleaner can bring
back original anti-corrosion properties.
Maintenance
Flow Regulator Installation