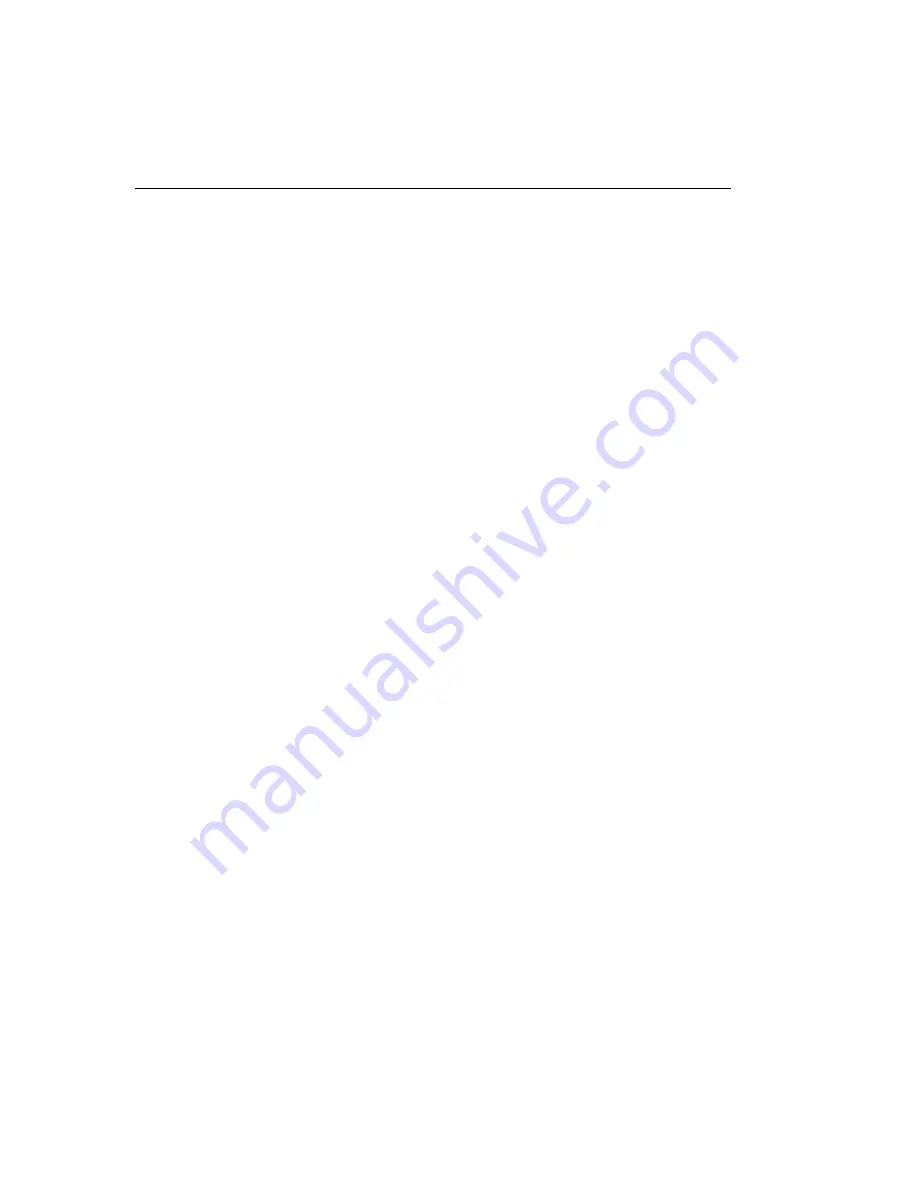
Chapter 2
28
Counter/Timer Operation Modes
The KUSB-3100 module supports the following counter/timer
operation modes:
• Event counting, described on this page.
• Frequency measurement, described on
.
• Edge-to-edge measurement, described on
• Rate generation, described on
.
Event Counting
Use event counting mode if you want to count the number of falling
edges that occur on Counter 0 In when the gate is active (high-level
gate or software gate). Refer to
for information about
specifying the active gate type.
You can count a maximum of 4,294,967,296 events before the counter
rolls over to 0 and starts counting again.
For event counting operations, use software to specify the
counter/timer mode as count, the C/T clock source as external, and
the active gate type as software or high-level.
Make sure that the signals are wired appropriately. Refer to the
KUSB-3100 Getting Started Manual
for an example of connecting an
event counting application.
Summary of Contents for KUSB-3100
Page 10: ...Contents x...
Page 14: ...About this Manual xiv...
Page 15: ...1 1 Overview Features 2 Supported Software 3...
Page 18: ...Chapter 1 4...
Page 46: ...Chapter 2 32...
Page 47: ...33 3 Supported Device Driver Capabilities...
Page 86: ...Chapter 4 72...
Page 87: ...73 5 Troubleshooting General Checklist 74 Service and Support 77...
Page 100: ...Chapter 6 86...
Page 101: ...87 A Specifications...
Page 112: ...Appendix A 98...
Page 113: ...99 B Connector Pin Assignments...
Page 115: ...101 C Reading from or Writing to the Digital Registers...