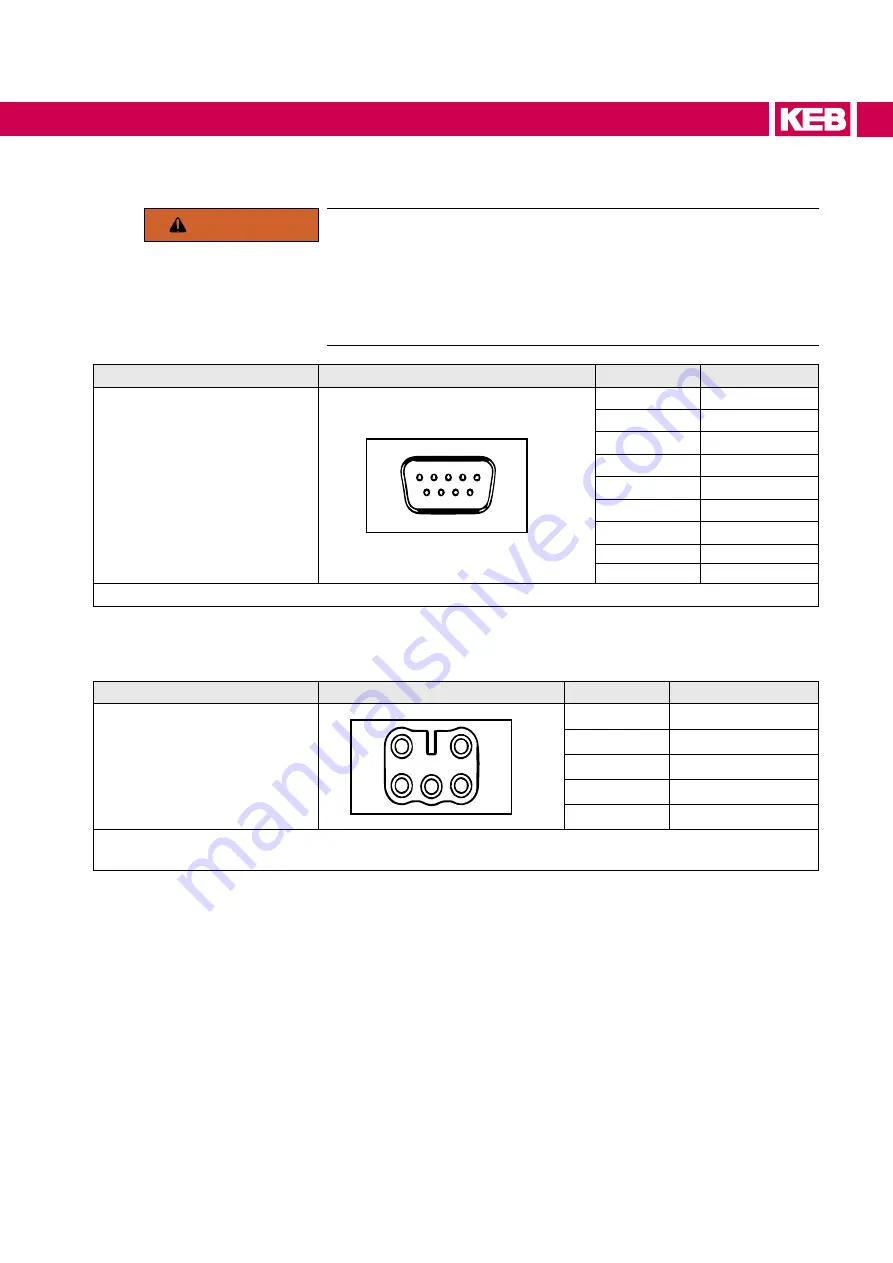
4.1.2 Encoder connection servo motor 7606910-40xx
WArNING
Adjustment of the measuring system
The measuring system of synchronous motors must be adjusted to the
respective inverter. Any mis-adjustment may lead to uncontrolled motor
response or complete failure of the motor.
In order to avoid any risk, the motor must be put into operation only in
no-load operation, without connection to the system.
Description
View
Pin Nr.
Signal
View of the connector pins of the
resolver
5
9
1
6
1
R1 (Ref+)
2
R2 (Ref-)
3
S1 (Cos+)
4
S3 (Cos-)
5
S2 (Sin+)
6
S4 (Sin-)
7
GND
housing
Shield
8, 9
Not connected
Figure 12: Terminal assignment of the resolver plug for servo motor 7606910-40xx
4.1.3 Connection of the brake and temperature monitoring for servo motor 7606910-40xx
Description
View
Pin Nr.
Signal
View of the brake and tempera-
ture connector
4
5
1
2
1
Brake +
2
Brake -
3
Temp. +
4
Temp. -
5
Not connected
Figure 13: Pin assignment of the brake connection and temperature monitoring for servo motor 7606910-
40xx
39
CONNECTION
Summary of Contents for 7608000-4001
Page 2: ......
Page 12: ...12 Standards forasynchronousand synchronous motors...
Page 18: ...18...
Page 24: ...24...
Page 36: ...36...
Page 48: ...48 NOTES...
Page 50: ......