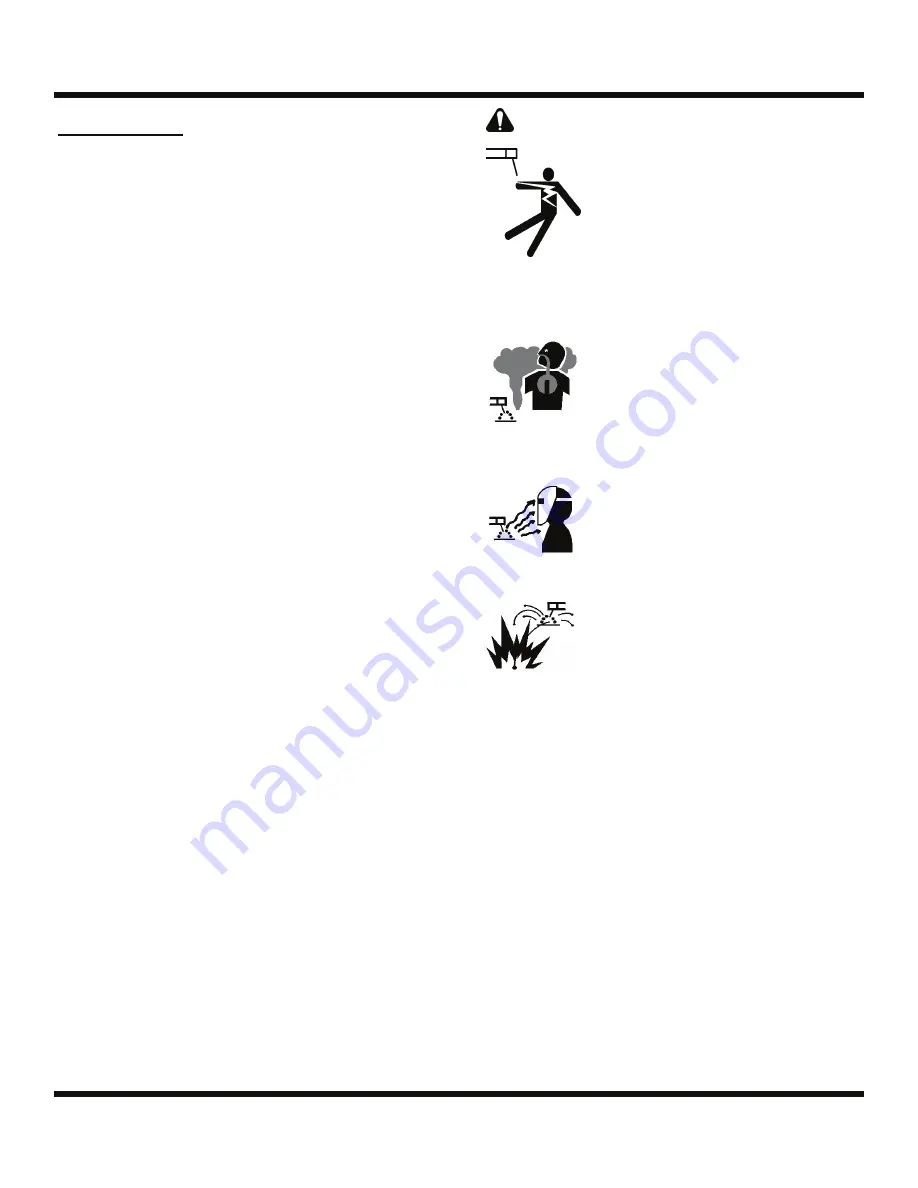
Installation/Setup
Loading Wire
1. Remove the shielding gas nozzle and the con-
tact tip.
2. Remove the spool cover by turning the spool
cover retaining knob counterclockwise.
3. Remove the spool retention spring and knob by
turning the knob counterclockwise.
4. Place the spool of wire on the wire spindle
with the wire coming off of the top of the spool
toward the nozzle end.
5. Replace the retention spring and knob and
tighten until the spool does not turn freely. Do
not over tighten, the spool should be able to
turn with about 2 pounds of pull on the wire.
6. Loosen the wire tension adjustment knob.
7. Extend a few inches of wire, cut off bent or
kinked wire. Straighten the wire by back bend-
ing the wire.
8. Guide the wire through the wire guide inlet to
the drive roll grove.
9. Once past the drive roll, guide the wire into the
tube liner.
10. Continue pushing the wire through until it ex-
tends 2 inches past the gas diffuser.
11. Slide the contact tip over the wire and thread it
into the gas diffuser.
12. Slide the shielding gas nozzle over the wire
and contact tip and thread it onto the gas dif-
fuser.
13. Tighten the spool tension adjustment knob to
increase the pressure of the drive wheel on the
wire being fed.
14. Reinstall the spool cover and cover retaining
knob.
15. Turn the welder on pull the trigger to insure
wire feeds properly.
16. The gun is ready to begin welding.
17. See welder manual for power and wire feed
control information.
KDAR Company
8
Electric Shock Can Kill
•
Do not touch live electrical parts
of the electrode with skin or wet
clothing.
•
Insulate yourself from work and
ground.
•
Always wear insulated gloves and keep them
dry.
Warning
Fumes & Gases Can Be Haz-
ardous
•
Welders and Spool Guns should
only be used in a well ventilated area
or with an exhaust system.
•
Keep your head away from the fumes.
Arc Rays Can Burn Skin and
Eyes
•
Always were eye, ear and body
protection.
Cutting Sparks Can Cause In-
jury, Fire , or Explosion
•
Do not use near flammable mate-
rial.
•
Do not weld on containers that have held com-
bustibles.
Summary of Contents for SPG
Page 11: ...KDAR Company 10 Notes ...