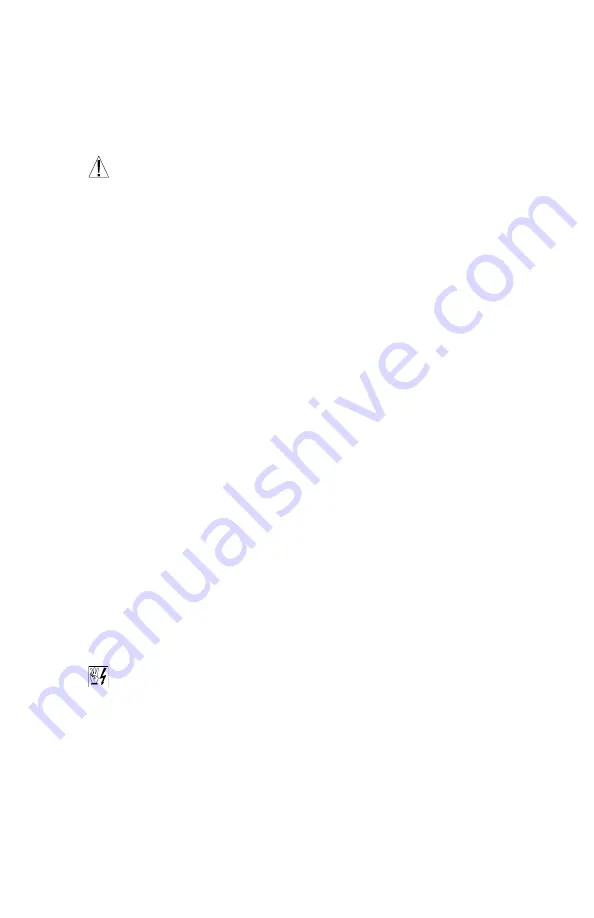
28
10 DRIVE OPERATION
10.1 Start-Up Procedure – After the drive has been properly setup (jumpers and trimpots set to the
desired positions) and wiring completed, the start-up procedure can begin. If the AC power has
been properly brought to the drive, the power (PWR) LED will illuminate green. The status (ST) LED
will indicate drive status, as described in Section 12.2.
To start the drive, momentarily set the Start/Stop Switch to the “START” position. The motor will
begin to accelerate to the set speed.
WARNING! Using a jumper to eliminate the start/stop function will cause the motor to run at
the Main Speed Potentiometer setting when the AC Line is applied. See Section 10.2.
Note:
If the motor rotates in the incorrect direction, it will be necessary to disconnect the AC Line, reverse
any two motor leads, and repeat the start-up procedure.
10.2 Restarting the Drive After a Fault has been Cleared
1,2
– The drive monitors five faults:
Undervoltage, Overvoltage, Short Circuit at the motor (phase-to-phase), Overload and Phase Loss
Detection. See Section 12.2 for the Status (ST) LED indication. Also see Section 6.3 on page 23 for
Automatic Ride-Through or Manual Restart selection with Jumper J3.
To restart the drive after a fault has been cleared, use the Start/Stop Switch
2,3
.
If the Start/Stop Switch has been eliminated (bypassed), see Section 5.6 on page 21.
4
The drive
can be restarted (after the fault has been cleared) by disconnecting the AC power, and all LEDs are
no longer illuminated, and then reconnecting the AC power.
Notes: 1.
For an Overload Fault, be sure the fault has been cleared before restarting the drive. Check the
motor current with an AC RMS responding ammeter. Also, the CL setting may be set too low. See Section
13.7 on page 30.
2.
For an Overvoltage Fault, if the drive is set for Automatic Ride-Through, the drive will
automatically restart when the AC Line voltage returns to below the specified Overvoltage Trip Point.
3
. If the Forward-Stop-Reverse Switch has been installed, it can be used to restart the drive.
4.
If the
Start/Stop Switch has been eliminated (bypassed), the AC Line must be used to restart the drive after an
Overload Fault has been cleared.
11 AC LINE FUSING
The drive does not contain line fuses. Most electrical codes require that each ungrounded conductor
contain circuit protection. Do not fuse neutral or ground connections. It is recommended to install
a fuse (Littelfuse 312/314, Buss ABC, or equivalent) or a circuit breaker in series with each ungrounded
conductor. Do not fuse motor leads. For the recommended fuse size, see Table 4 on page 14.
Wire the drive in accordance with the National Electrical Code requirements and other local codes that
may apply to the application.
12 DIAGNOSTIC LEDs
The drive contains two diagnostic LEDs mounted on the enclosure cover to display the drive’s
operational status.
12.1 Power On LED (PWR) – The “PWR” LED will illuminate green when the AC Line is applied
to the drive.
WARNING! Do not depend on the PWR LED as a guaranteed power off condition.
Be sure the main power switch or circuit breaker is in the “OFF” position before
servicing this drive.
12.2 Status LED (ST) – The “ST” LED is a tricolor LED which provides indication of a fault or abnormal
condition. The information provided can be used to diagnose an installation problem such as incor-
rect input voltage, overload condition, and drive output miswiring. It also provides a signal which
informs the user that all drive and microcontroller operating parameters are normal.
Table 7, summarizes the “ST” LED functions.
Summary of Contents for KBAC-24D
Page 34: ...34 Notes ...
Page 35: ...35 Notes ...