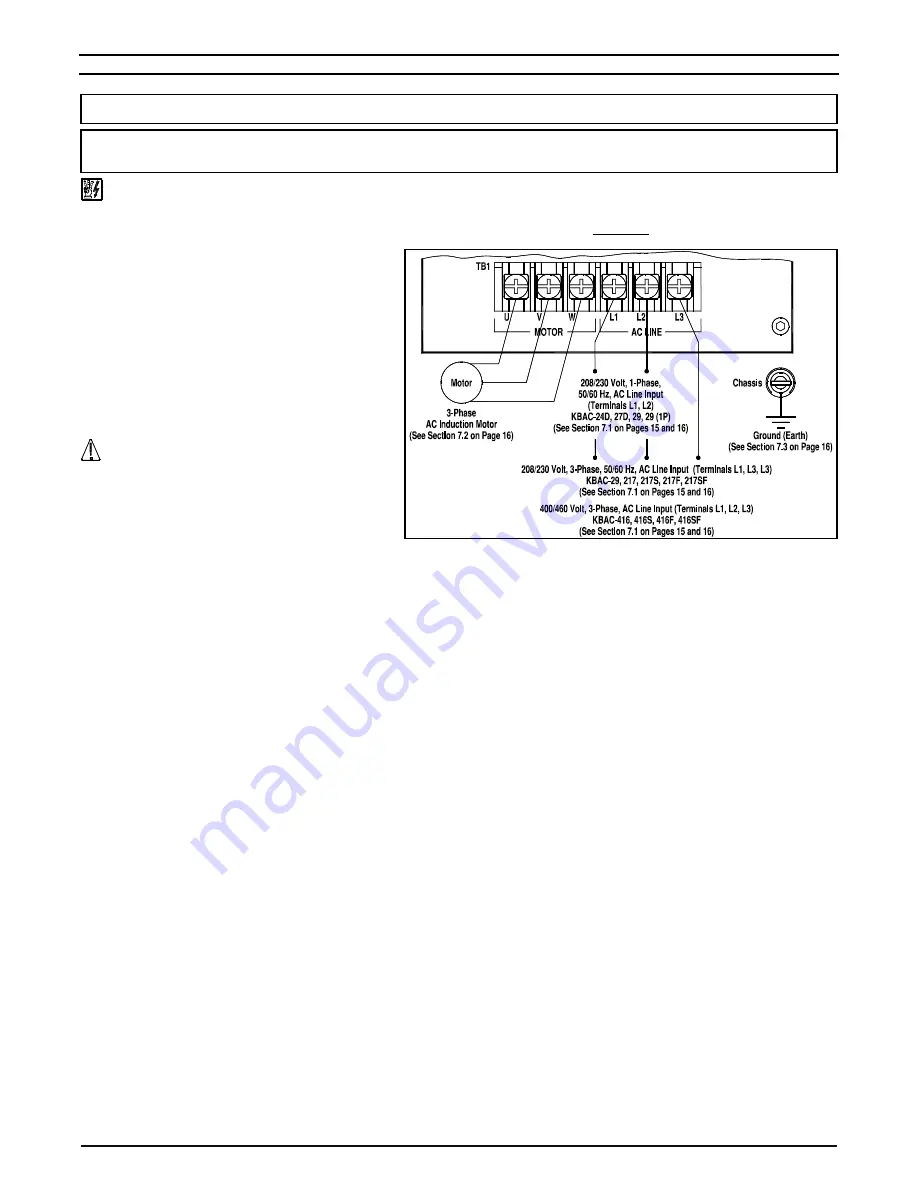
KBAC SERIES INSTALLATION AND OPERATION MANUAL
4
1 – QUICK-START INSTRUCTIONS
Also see Section 4 – Important Application Information on page 5.
Important:
You must read these simplified instructions before proceeding. These instructions are to be used as a reference only and are not
intended to replace the details provided herein. You must read the Safety Warnings on page 5 before proceeding.
Reconditioning the Bus Capacitors:
If this drive has been in storage for over one year, it is necessary to recondition the power supply bus
capacitors. To recondition the bus capacitors, apply the AC Line, with the drive in the Stop Mode, for a minimum of one hour. Not following
this procedure will cause the bus capacitors to fail.
WARNING! High Voltage!
Disconnect the main power before making connections to the control. Do not depend on the POWER or
STATUS LEDs, located on the front cover, to no longer be illuminated as a guaranteed power off condition.
1.1 – MOUNTING INSTRUCTIONS
See Section 5 on page 12.
1.2 – AC LINE INPUT FUSING
It is recommended that a fuse(s) or circuit breaker be
installed in the AC Line. Fuse each conductor that is not at
ground potential. For the recommended fuse size, see
Table 2 on page 7. Also see Section 6 on page 15.
1.3 – AC LINE INPUT CONNECTION
Connect the AC Line input to Terminal Block TB1, as
shown in Figure 1. Also see Section 7.1 on pages 15 and
16.
GFCI Operation:
Third Generation (3G) drives are jumper
selectable (J12) for standard and sensitive GFCIs.
CAUTION!
The rated AC Line voltage of the drive
must match the actual AC Line input voltage.
On KBAC-24D, 27D the setting of Jumper J1 must match
the actual AC Line input voltage.
KBAC-24D, 27D, 29 (1P):
Designed to accept 1-phase
(Terminals L1, L2) AC Line input only. Rated for 208/230
Volt AC Line input with Jumper J1 set to the "230V" position (factory setting). Rated for 115 Volt AC Line input with Jumper J1 set to the
"115V" position. KBAC-27D is rated for 1½ HP maximum with 115 Volt AC Line input and 2 HP maximum with 208/230 Volt AC Line input.
KBAC-29:
Designed to accept 1-phase (Terminals L1, L2) or 3-phase (Terminals L1, L2, L3) AC Line input. Rated for 208/230 Volt AC Line
input only. Rated for 2 HP maximum with 1-phase AC Line input and 3 HP maximum with 3-phase AC Line input.
KBAC-217, 217S, 217F, 217SF:
Designed to accept 3-phase (Terminals L1, L2, L3) AC Line input only. Rated for 208/230 Volt AC Line input
only.
KBAC-45, 48, 416, 416S, 416F, 416SF:
Designed to accept 3-phase (Terminals L1, L2, L3) AC Line input only. Rated for 400/460 Volt AC
Line input only.
1.4 – MOTOR CONNECTION
Connect the motor to Terminal Block TB1 Terminals U, V, W, as shown in Figure 1 above. See Section 7.2 on page 16. Motor cable length
should not exceed 100 ft. (30 m) – special reactors may be required – contact Technical Support.
1.5 – GROUND CONNECTION
Connect the ground wire (earth) to the ground screw, as shown in Figure 1 above. See Section 7.3 on page 16. Be sure the motor is also
properly grounded.
1.6 – 60 Hz AND 50 Hz MOTOR OPERATION
The drive is factory set for 60 Hz motor operation (Jumper J4 set to the "1X" position and Jumper J5 set to the "60Hz" position). For 50 Hz
motor operation, be sure Jumper J4 is set to the "1X" position and set Jumper J5 to the "50Hz" position. See Section 10.4 on page 19.
1.7 – START/STOP SWITCH
A prewired Start/Stop Switch is supplied to electronically "start" and "stop" the drive, as described in Section 7.5 on page 17. This switch must
be used to "start" the drive each time the AC Line is applied to the drive or to "restart" the drive. Also see Section 10.8 on page 20.
1.8 – JUMPER SETTINGS
All jumpers have been factory set for most applications. However, some jumpers may need to be set in order to tailor the drive for a specific
application. See Section 10 on pages 19 and 20.
IMPORTANT:
To ensure that the motor is properly protected with the I
2
t Overload Protection feature, it is required that Jumper J2 is set to the
corresponding position for the motor horsepower being used, as shown in Figure 23 on page 19.
1.9 – TRIMPOT ADJUSTMENTS
All trimpots have been factory set for most applications. Some applications require adjustment of the trimpots to tailor the drive for a specific
requirement. See Section 12 on page 21 and 22.
1.10 – DIAGNOSTIC LEDs
After power has been applied, observe the LEDs to verify proper drive operation, as described in Section 13 on page 23.
FIGURE 1
GENERAL CONNECTION DIAGRAM