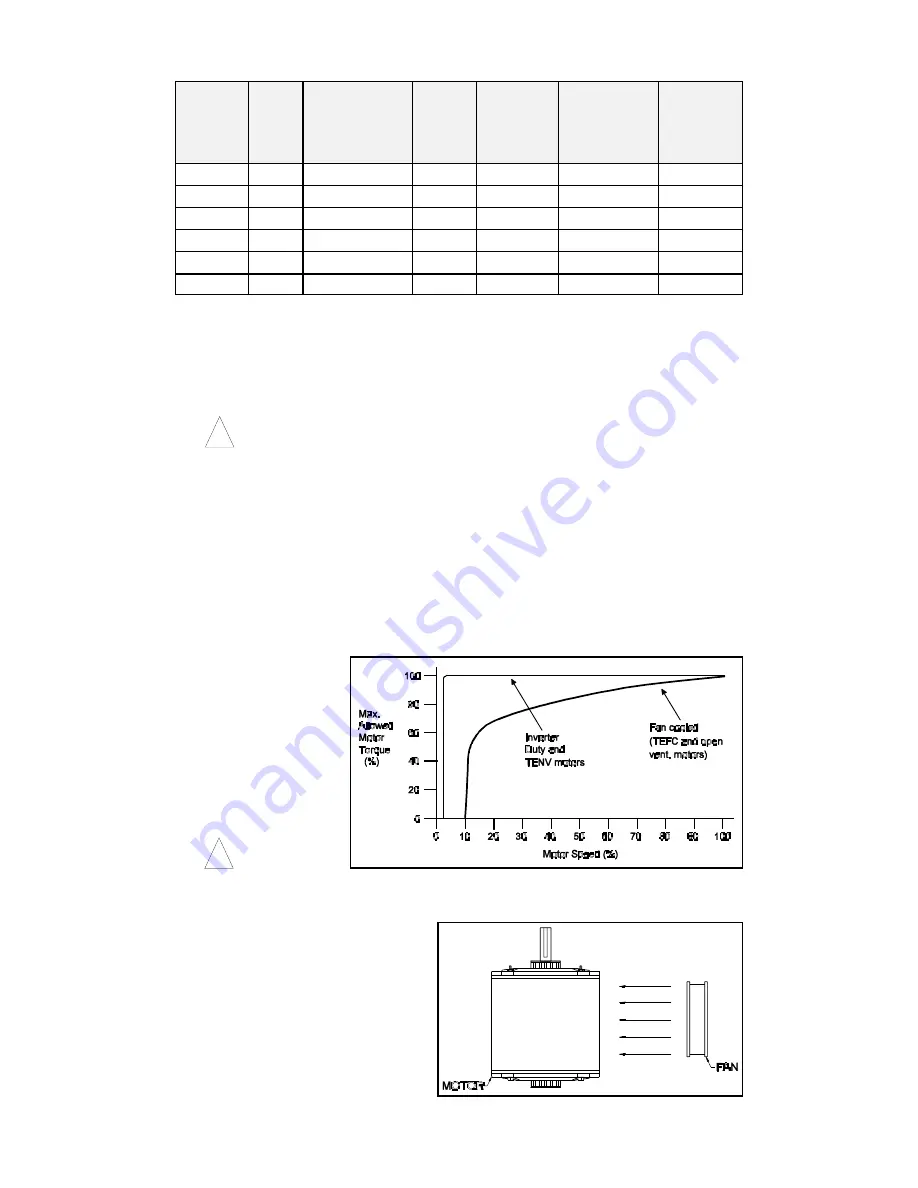
FIG. 1 – MAXIMUM ALLOWED MOTOR TORQUE vs SPEED
FIG. 2 – MOTOR WITH EXTERNAL COOLING
TABLE 2 – ELECTRICAL RATINGS
Model No.
KB Part
No.
Input Voltage
(VAC– 50/60 Hz)
Single Phase
Nominal
Output
Voltage
(VAC)
Maximum
Horsepower
Rating
HP, (KW)
Maximum
Continuous
Output Load
Current (RMS
Amps/Phase)
Maximum
AC Line
Input
Current
(Amps AC)
KBVF-13
9957
115
0 – 230
1/2, (.37)
2.4
11.0
KBVF-23
9958
230
0 – 230
1/2, (.37)
2.4
7.0
KBVF-23D
9959
115/230
0 – 230
1/2, (.37)
2.4
11.0 / 7.0
KBVF-14
9977
115
0 – 230
1, (.75)
4.0
16.0
KBVF-24
9978
230
0 – 230
1, (.75)
4.0
10.0
KBVF-24D
9979
115/230
0 – 230
1, (.75)
4.0
16.0 / 10.0
II.
IMPORTANT APPLICATION INFORMATION.
Most fan-cooled (TEFC and open ventilated) 3-phase motors will overheat if used with
an inverter beyond a limited speed range at full rated torque. Therefore, it is necessary
to reduce motor load as speed is decreased. Note: Some fan cooled motors can be
used over a wider speed range. Consult motor manufacturer for details.
WARNING!
There may be some motors whose characteristics may cause
overheating and winding failure under
light load
or
no load
conditions. If the
motor is operated in this manner for an extended period of time, it is recommended that
the unloaded motor amperage be checked from 2-15 Hz (60-450 RPM) to ensure motor
current does not exceed the nameplate rating.
Do not use the motor if the motor
current exceeds the nameplate rating.
...Continued on page 8
7
Inverter duty and
most totally
enclosed
nonventilated
(TENV) motors can
provide full rated
motor torque over an
extended speed
range without
overheating see
fig. 1.
Therefore, it is
recommended
that this control be used with
inverter duty and totally enclosed
nonventilated (TENV) motors.
If external fan cooling is provided,
open-ventilated motors can also
achieve an extended speed range
at full rated torque. A box fan or
blower with a minimum of 100 CFM
is recommended. Mount the fan a
few inches from the motor so it is
surrounded by the air flow.
8
!
!