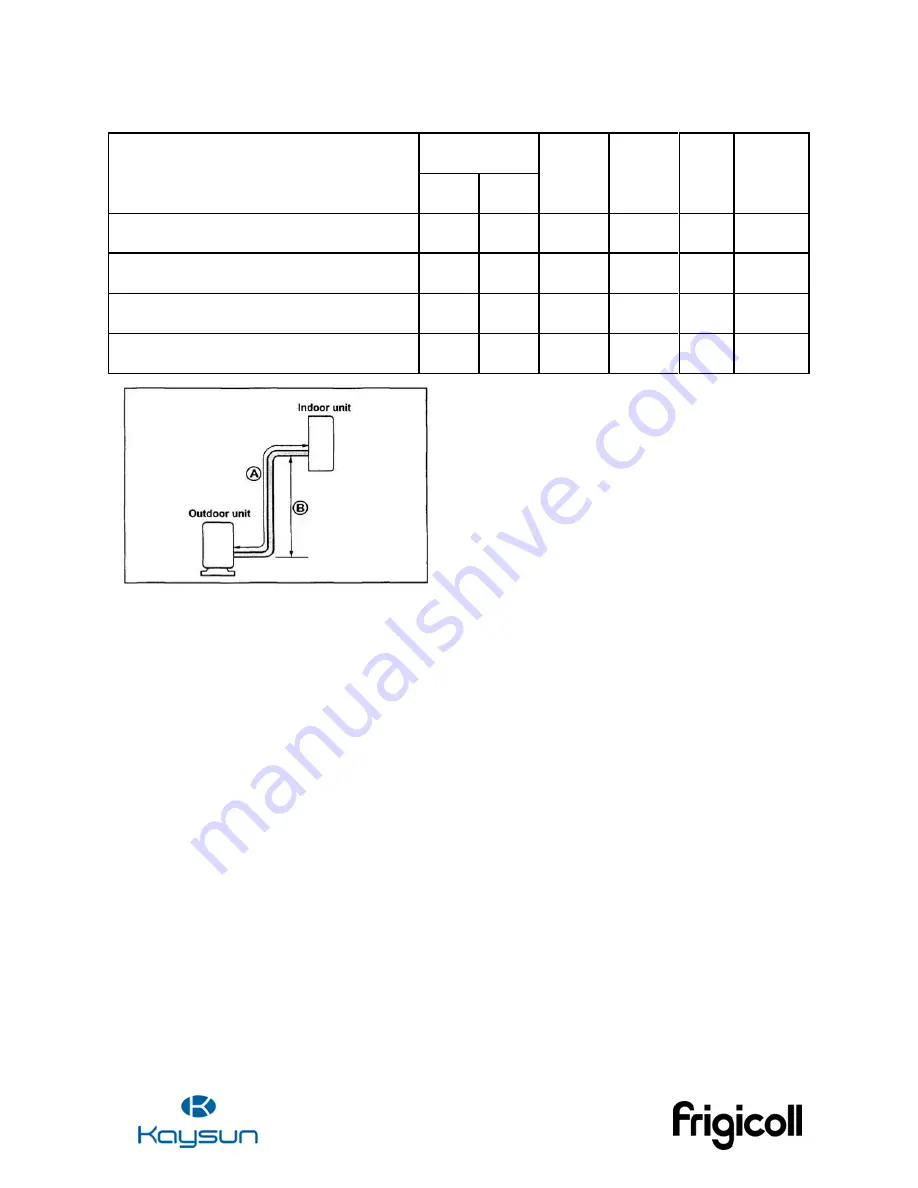
PRODIGY Technical Manual
20
5.3 Pipe length and the elevation
The pipe length and refrigerant amount:
Model
Pipe size
Standard
length
(m)
Max.
Elevation
B (m)
Max.
Length
A (m)
Additional
refrigerant
(g/m)
Gas
Liquid
KAY-26 DN7 + KAE-26 DN7
3/8‟‟
(
Ф9.52)
1/4‟‟
(Ф6.35)
5
10
25
15
KAY-35 DN7 + KAE-35 DN7
3/8‟‟
(
Ф9.52)
1/4‟‟
(Ф6.35)
5
10
25
15
KAY-52 DN7 + KAE-52 DN7
1/2
‟‟
(Ф12.7)
1/4‟‟
(Ф6.35)
5
20
30
15
KAY-71 DN7 + KAE-71 DN7
5
/8‟‟
(
Ф15.9)
3/8‟‟
(
Ф9.52)
5
25
50
30
Caution:
The capacity test is based on the standard length and the maximum permissive length is based on the
system reliability.
Summary of Contents for KAY-26 DN7
Page 1: ...PRODIGY 3D Inverter Technical Manual...
Page 11: ...PRODIGY Technical Manual 11 For KAY 26 DN7...
Page 12: ...PRODIGY Technical Manual 12 For KAY 35 DN7 For KAY 52 DN7...
Page 13: ...PRODIGY Technical Manual 13 For KAY 71 DN7...
Page 14: ...PRODIGY Technical Manual 14 3 2 Outdoor Unit...
Page 15: ...PRODIGY Technical Manual 15 For KAE 26 DN7...
Page 16: ...PRODIGY Technical Manual 16 For KAE 35 DN7 KAE 52 DN7...
Page 17: ...PRODIGY Technical Manual 17 For KAE 71 DN7...
Page 64: ......