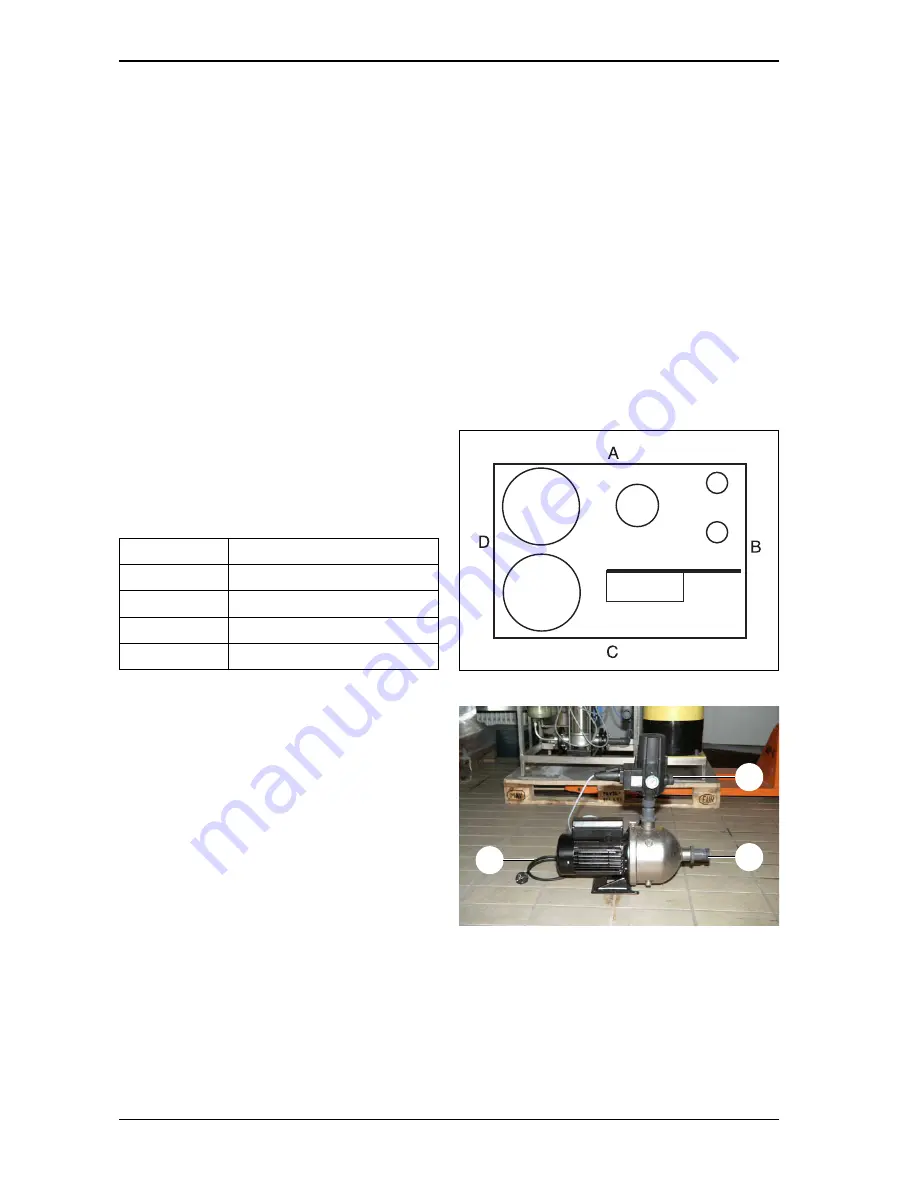
26
OPERATION OF THE SYSTEM
WTC 600 LP / MP
Service Handbook 08.2004
3.3
Connecting the Equipment
3.3.1
Connections, Valves and Indicators
Depending on the local untreated water supply, the WTC 600 LP/MP is connected directly to the
off-site supply or supplemented through a WTC 600 PI pressure-increase module.
The following constructional measures must be observed:
- The off-site untreated water supply must be equipped with a shut-off device (supplied by user
/ customer).
- All pipes / lines (untreated water, backwashing, concentrate and drinking water) to be installed
without mechanical tension.
- Drinking water line to be installed with free run-out and no further shut-off devices.
- Backwashing line to be installed with steady drop (under no circumstances inclined upward).
For easy and secure operation and main-
tenance of the system, minimum clearances
from the walls are to be observed:
Page
Minimum clearances [cm]
A
50
B
10
C
70
D
50
Table 12
Minimum clearances
Installation space (incl. working space for maintenance and operation, not including piping):
WTC 600 LP and MP: width x depth: 1300 x 1900mm
WTC 600 LP-A, LP-AM, MP-A, MP-AM: width x depth: 1700 x 1900 mm
WTC 600 CD: width x depth: 500 x 1100 mm
WTC 600 PI: width x depth: 600 x 200 mm
Figure 8
Minimum clearances WTC 600 LP/MP
Figure 9
Water connections, WTC 600 PI
2
1
3
Summary of Contents for WATERCLEAN 600 CD
Page 1: ...Service Handbook 5 905 521 08 2004 Waterclean 600 CD LP MP PI 1 024...
Page 6: ...WTC 600 LP MP 6 Service Handbook 08 2004...
Page 64: ...64 APPENDIX WTC 600 LP MP Service Handbook 08 2004 RO control program structure Figure21...
Page 65: ...65 WTC 600 LP MP APPENDIX Service Handbook 08 2004...