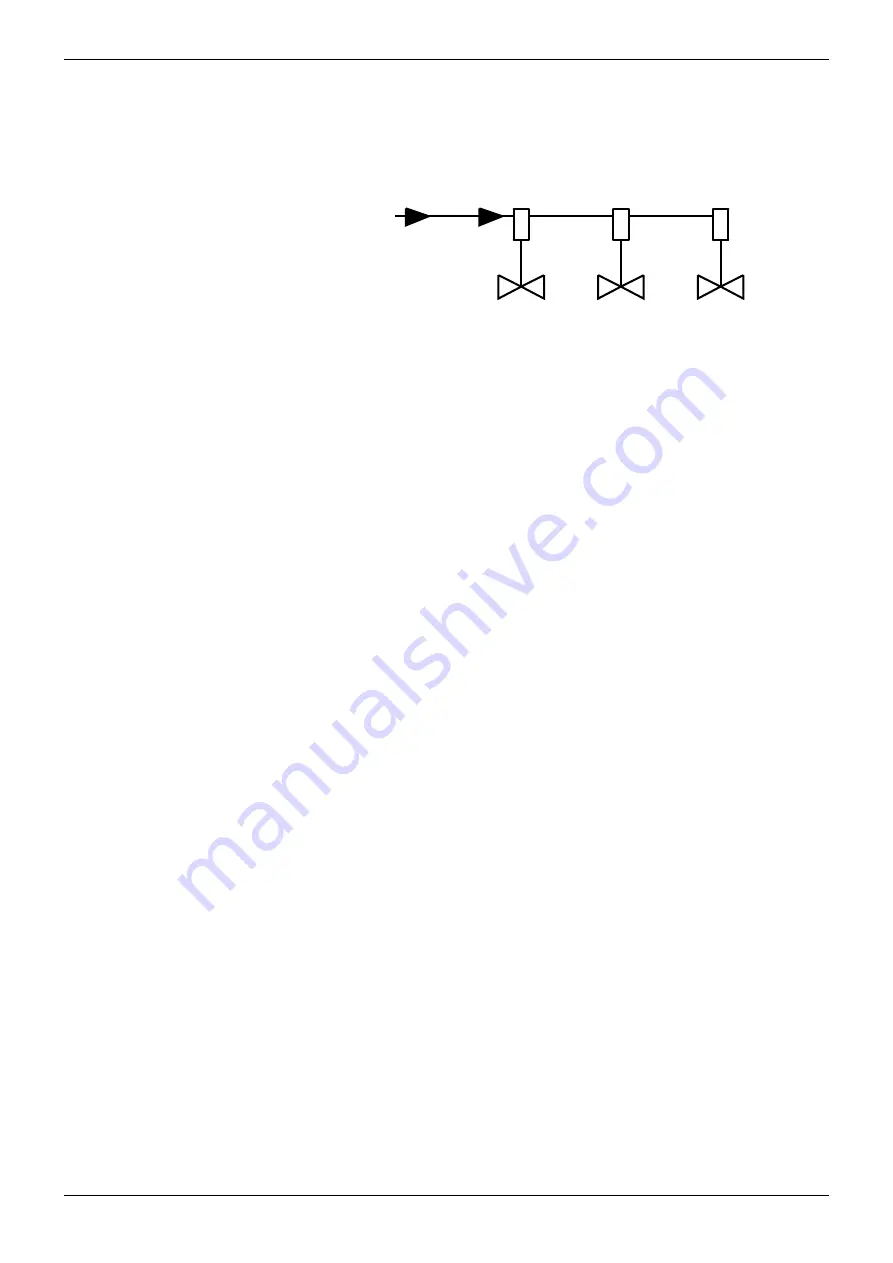
5.961-163 A 2006087 (09/03)
English
Operating instructions
HD 9000 E USA
B. Design and function
4.
Flow diagram of compressed air supply
for pneumatic high-pressure solenoid valves
(gantry and underbody wash) on the
high-pressure module
Figure B.5
Flow diagram
1 Compressed air inlet (provided on site)
2 „Bypass“ solenoid valve
3 „High-pressure gantry“ solenoid valve
4 „High-pressure underbody wash“ solenoid valve
(optional)
B5
1
2
3
4
Summary of Contents for HD 9000 E USA
Page 2: ......