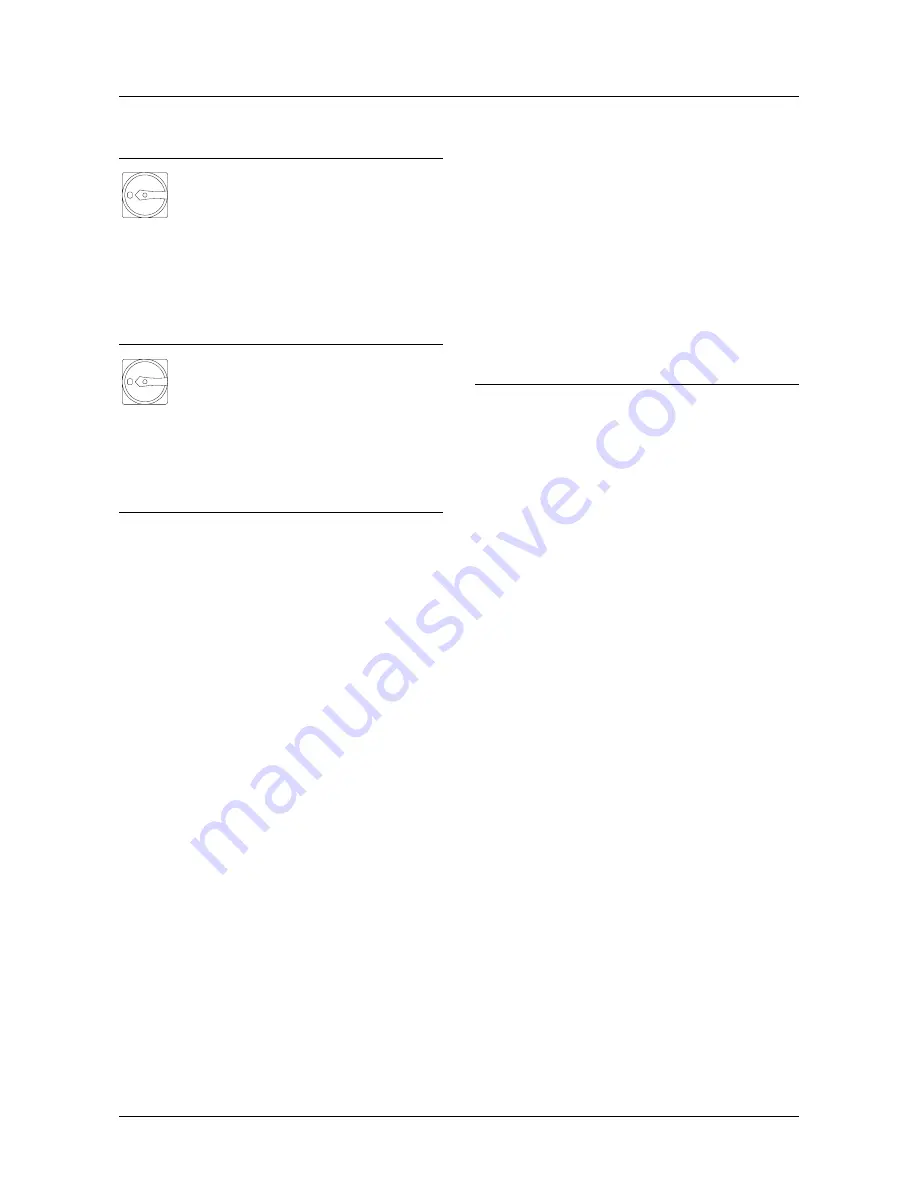
HD 4000 C / HD 6000 C
English
5.956-648 A10369 (06/98)
10. Protective Devices
System operation is stopped by the
Emergency-STOP master switch
located at the instrument panel.
n
Inadvertent contact with all hot system
components is prevented by the
protective housing.
11. Emergency Drill
Disable the system by activating
the Emergency-STOP master
switch.
n
Release water pressure by opening a
high-pressure spray gun.
12. Guidelines and Regulations
In the Federal Republic of Germany the
operation of this system is subject to the
Regulations for Liquid Spraying Devices
(VBG ZH 1/406), published by the Principal
Organisation of the Commercial Employers’
Liability Insurance Association. The
guidelines may be ordered from Carl
Heymann Verlag KG, Luxemburger Strasse
449, D-50939 Cologne, Germany.
Among other requirements, the Regulations
foresee a system inspection by a certified
professional in intervals of no more than 12
months. The results of the inspection must
be documented in writing.
A testing log for entering the inspection
results is located at the end of this manual.
Kärcher customer service engineers qualify
as certified professionals, and are
authorised to carry out the aforementioned
inspection.
Also applicable are the (German)
Regulations governing liquid spraying
devices, VBG 87, and the Ordinance on
Hazardous Substances VBG ZH 1/220
(GefStoffV).
A. For Your Safety
Please also observe local regulations
concerning electrical connections, water
supply and waste-water connections. The
applicable regulations may be obtained
from the respective utility companies.
Any connection and installation work in
accordance with the aforementioned
regulations must be carried out by the
Kärcher customer service or authorised
contractors.
13. Proper Use of the Equipment
This system conveys water under high
pressure to high-pressure cleaning stations
situated downstream of the system. The
system is designed for stationary
installation in a dry indoor environment. At
the installation site, a water and mains
power connection satisfying the criteria
stated in the Specifications section of this
manual must be provided. The
environmental temperature at the
installation site must not rise above 40 °C.
The high-pressure water is distributed via a
fixed-installation tubing network.
Only clean water may be used as a high-
pressure medium. Water contamination of
any kind would cause premature
component wear or lead to deposits within
the system.
In the presence of water hardness
exceeding 15°dH appropriate water
treatment measures for lowering the
hardness point.
The use of recycling water requires prior
discussion with Kärcher.
A4