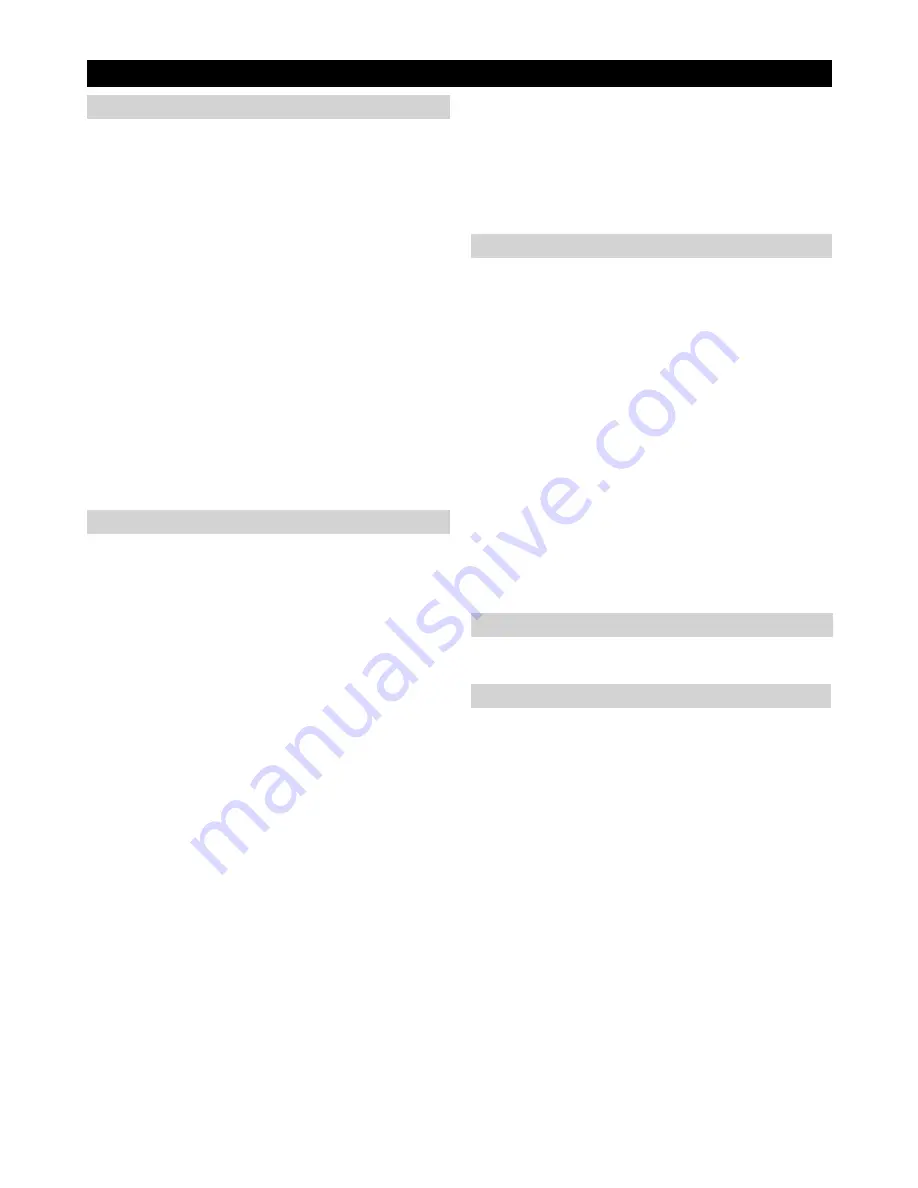
English
5.906-494.0 Rev. 01 (04/11)
23
–
No power
Check whether the voltage indicated on the type
plate corresponds to the voltage of the socket.
Check the mains connection cable for damages.
–
Indicator lamp is blinking green
Operational readiness period has expired. Switch
on/off the appliance again.
–
The water shortage fuse (option) was triggered
due to low water inlet pressure.
The indicator lamp "lack of water" will illuminate.
Check water inlet pressure, minimum value see
"Specifications".
Turn the device switch to "0" and turn on again to
restart the system.
–
Motor overloaded/ over-heated or electrical circuit
breaker or winding protection switch has got re-
leased.
Switch off appliance and let it cool down. Remove
the cause of the problem. Turn on the appliance
again.
The indicator lamps display the operating states
(green) and interruptions (red).
Reset:
Set the appliance switch to "0".
Wait for a while.
Set the appliance switch to "I".
Continuous green:
–
The appliance is now ready for operation.
1x blinking green:
–
Operational readiness has expired after 30 min-
utes.
–
The appliance has switched off after 30 minutes of
continuous operation (safety if the high pressure
hose bursts).
Continuous red light:
–
Electrical problems in appliance
Pull out the mains plug.
Call Customer Service.
1x blinking red:
–
High pressure side is leaky
Check high pressure hose, hose connections and
hand spray gun for leaks.
2x blinking red:
–
Engine overload/overheat
Set the appliance switch to "0".
Allow device to cool down.
Set the appliance switch to "I".
–
Water pressure is too low
Ensure adequate water line pressure.
3x blinking red:
–
Fault in the voltage supply
Check main connections and mains fuse.
4x blinking red:
–
Power consumption is too high
Call Customer Service.
–
Wrong nozzle
Check nozzle for correct size (see technical spec-
ifications).
–
Flushed the nozzle.
Clean/ replace nozzle.
–
Filter is dirty.
Clean filter at the water connection.
Unscrew the filter casing, remove the filter, clean
it and replace it.
–
Air within the system
Appliance ventilation:
Unscrew the nozzle. Switch on the appliance and
let it run until the water exiting from the spray pipe
is bubble-free. Switch off the appliance and fit the
nozzle again.
–
Pipe inlets to pump are leaky or blocked
Check all supply lines to the pump for leaks or
blockages.
3 drops per minute are permitted and can come
out from the lower side of the appliance.
Check all supply lines to the high-pressure pump
for leaks or blockages.
Appliance ventilation:
Unscrew the nozzle. Switch on the appliance and
let it run until the water exiting from the spray pipe
is bubble-free. Switch off the appliance and fit the
nozzle again.
6
Troubleshooting
6.1
Appliance is not running
6.2
Indicator lamp
6.2.1 Operating status display
6.2.2 Fault indication
6.3
Device is not building up pressure
6.4
High pressure side is leaky
6.5
High pressure pump is vibrating