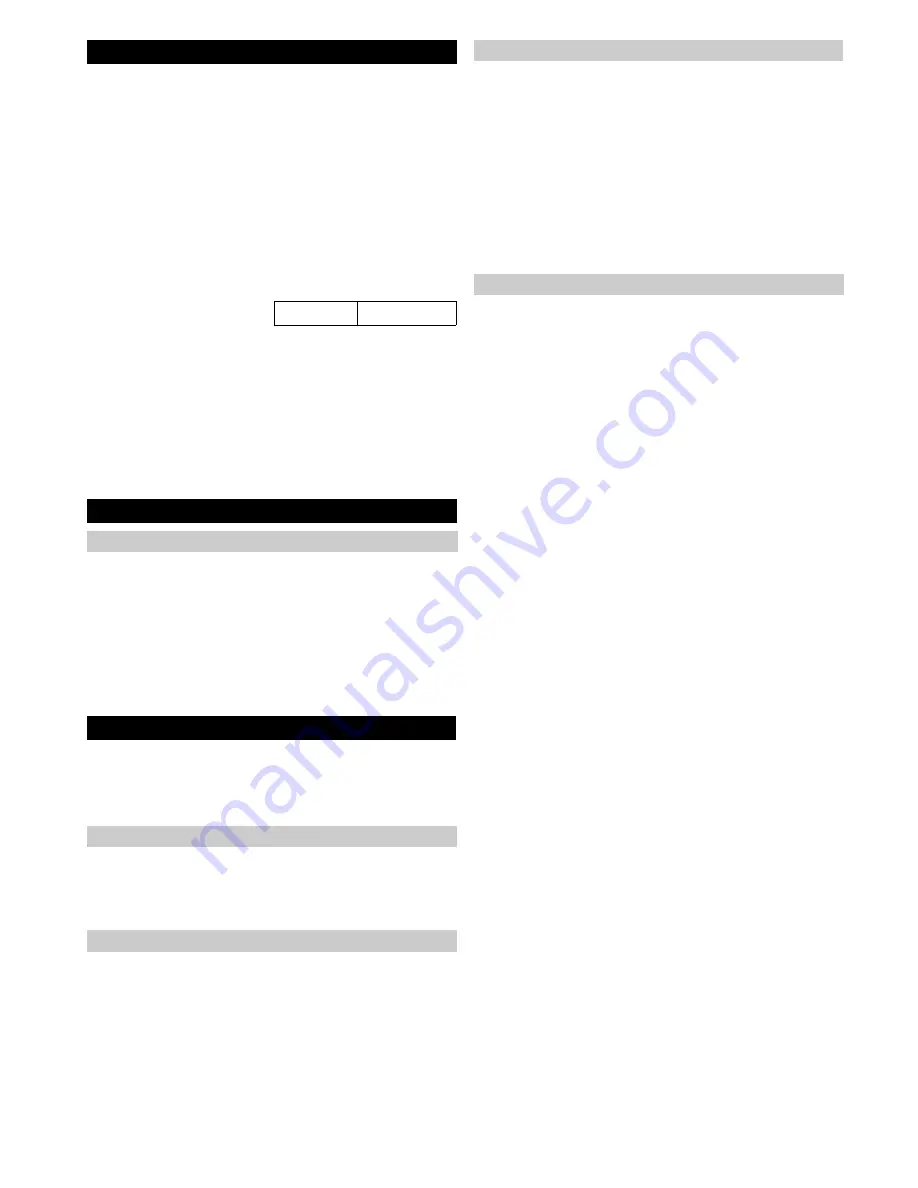
4
English
5.906-441.0 Rev. 01 (06/10)
Good service work requires extensive and practice-oriented train-
ing as well as well-structured training materials.
Hence we offer regular basic and advanced training programmes
covering the entire product range for all service engineers.
In addition to this, we also prepare service manuals for important
appliances - these can be initially used as instruction guides and
later on as reference guides.
Apart from this, we also regular information about product en-
hancements and their servicing.
If you should require supplements, have corrections or questions
regarding this document, please address these citing the following
subject to:
The responsible product specialist will take care of your issue.
Copying and duplication of texts and diagrams as well as
third-party access to this information is permitted only with
the explicit permission of the company:
Alfred Kärcher GmbH & Co. KG
P O Box 160
D -71349 Winnenden
www.kaercher.com
Danger
Immediate danger that can cause severe injury or even death.
몇
Warning
Possible hazardous situation that could lead to severe injury or
even death.
Caution
Possible hazardous situation that could lead to mild injury to per-
sons or damage to property.
Customised specifically to the requirements of the construction in-
dustry's machinery and accessories, these appliances feature a
crankshaft pump for long idle periods. The appliance can be trans-
ported easily due to its large, air-filled tyres and powder-coated
steel pipe frame with its built-in crane hook.
–
4-pin, air-cooled three-phase motor with 1400 rpm.
–
24 PS/17,76 kW, 2-cylinder petrol motor Honda GX 670
–
3 piston crankshaft pump
–
Ceramic piston
Diameter 16 mm at HD 13/35
Diameter 14 mm at HD 9/50
–
Cylinder head made of brass
–
Pressure and suction valves made of stainless steel, valve cag-
es made of plastic
–
Pressure and quantity regulation at the overflow
–
Built-in large water filter protects the pump from contamination.
The filter can be easily removed and cleaned
–
Oil level can be checked from the outside
–
Automatic safety switch-off after 30 minutes of non-operation
–
Winding protection contact
–
The pressure switch on the overflow switches the motor con-
tactor
–
Soft start increases the motor speed gradually to 1,400 1/min
and protects the circuit from overloads when switched on
–
Speed control on the pump reduces the motor speed to idle
speed when the hand spray gun is closed
–
The thermo valve the circuit water from becoming overheated
while the hand spray gun is closed
–
Newly developed industrial hand spray gun with rotating spray
tube
–
Power nozzle, 15° flat spray
–
High pressure hose 10 m
HD 9/50-4 Cage: DN 8, 64 MPa (640 bar)
HD 13/35-4 Cage: DN 10, 62 MPa (620 bar)
–
Rotating coupling for the connection of the high pressure hose
to the gun
1
Preface
Subject:
Fall 108022
2
Safety instructions
2.1
Hazard levels
3
Technical Features
3.1
Drive
3.1.1
HD 9/50-4 Cage, HD 13/35-4 Cage
3.1.2
HD 9/50 PE Cage, HD 13/35 PE Cage
3.2
Pump
3.3
Control
3.3.1 HD 9/50-4 Cage, HD 13/35-4 Cage
3.3.2 HD 9/50 PE Cage, HD 13/35 PE Cage
3.4
Accessories