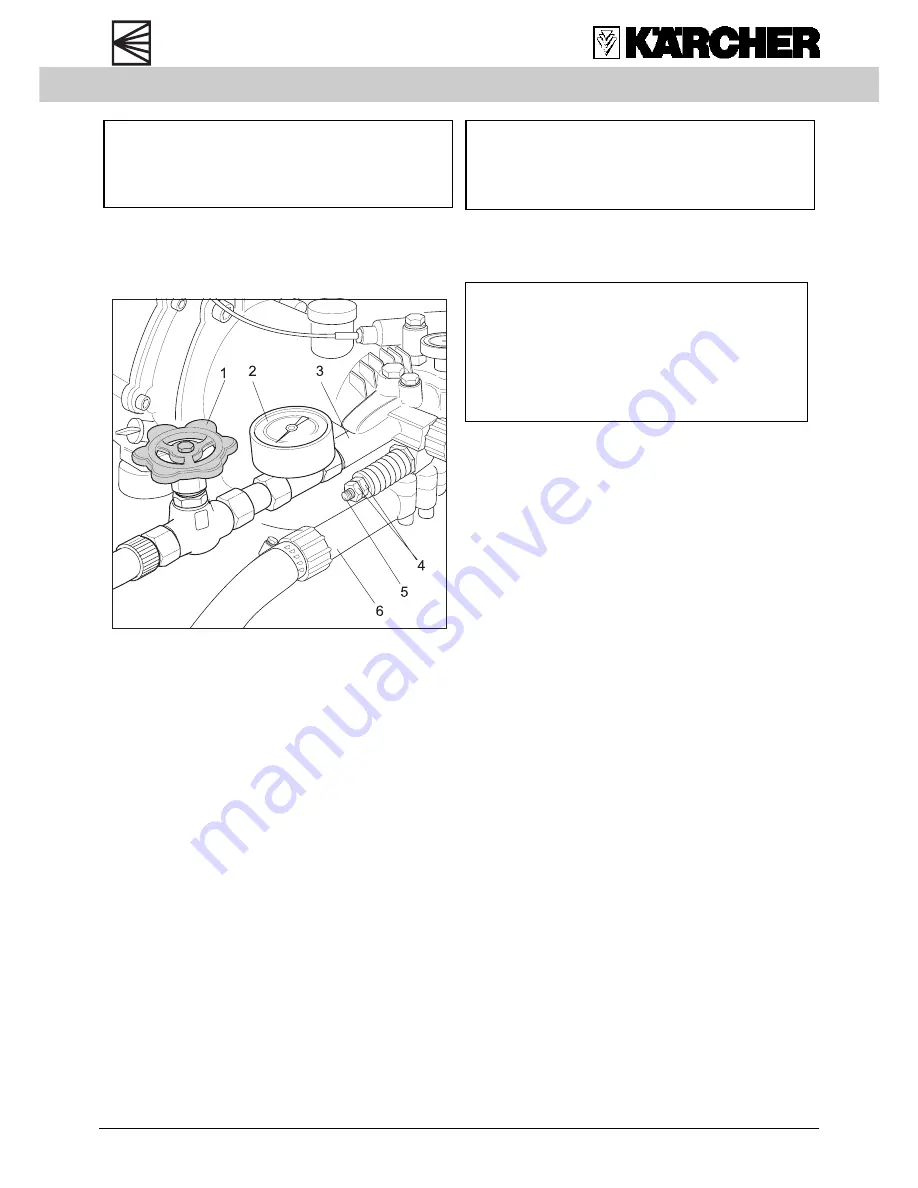
Page 7/10
International Service Information
International Service Information
June 24th, 1999
HD 1050 B
New Unit Information
Adjustment overflow valve
Note
Before any adjustments the high-pressure
nozzle, air filter and spark plug must be
checked for damage or wear. All defective
parts must be replaced.
1. Mount test pressure gauge (2), shut-off valve
(1), high-pressure hose and servopress
handgun on high-pressure outlet (3).
The unit pressure gauge is not to be used to
check the operation pressure because it
measures too inaccurate !
2. Set servopress handgun to maximum water
volume and operate the unit.
3. Close shut-off cock (1) slowly until flow rate
has achieved 6,7 to 7,5 litres/min. (see
technical data). This corresponds to the
smallest servopress setting (flow rate
measured by litres).
4. Now set adjusting screw (4) to operation
pressure 208 to 212 bar (see technical
data) and check with test pressure
gauge.
Increase spring tension: pressure
increases.
Decrease spring tension: pressure
decreases.
5. Open shut-off valve completely. Close and
open servopress handgun several times.
6. Repeat step 3 and 4 and adjust once more
if required.
7. Finally secure the adjusting screw with
locking nut (4) and seal with safety paint.
1
Shut-off valve
2
Test pressure gauge
3
High-pressure outlet
4
Adjusting screw with locking nut
5
Overflow valve spindle
6
Water inlet connection