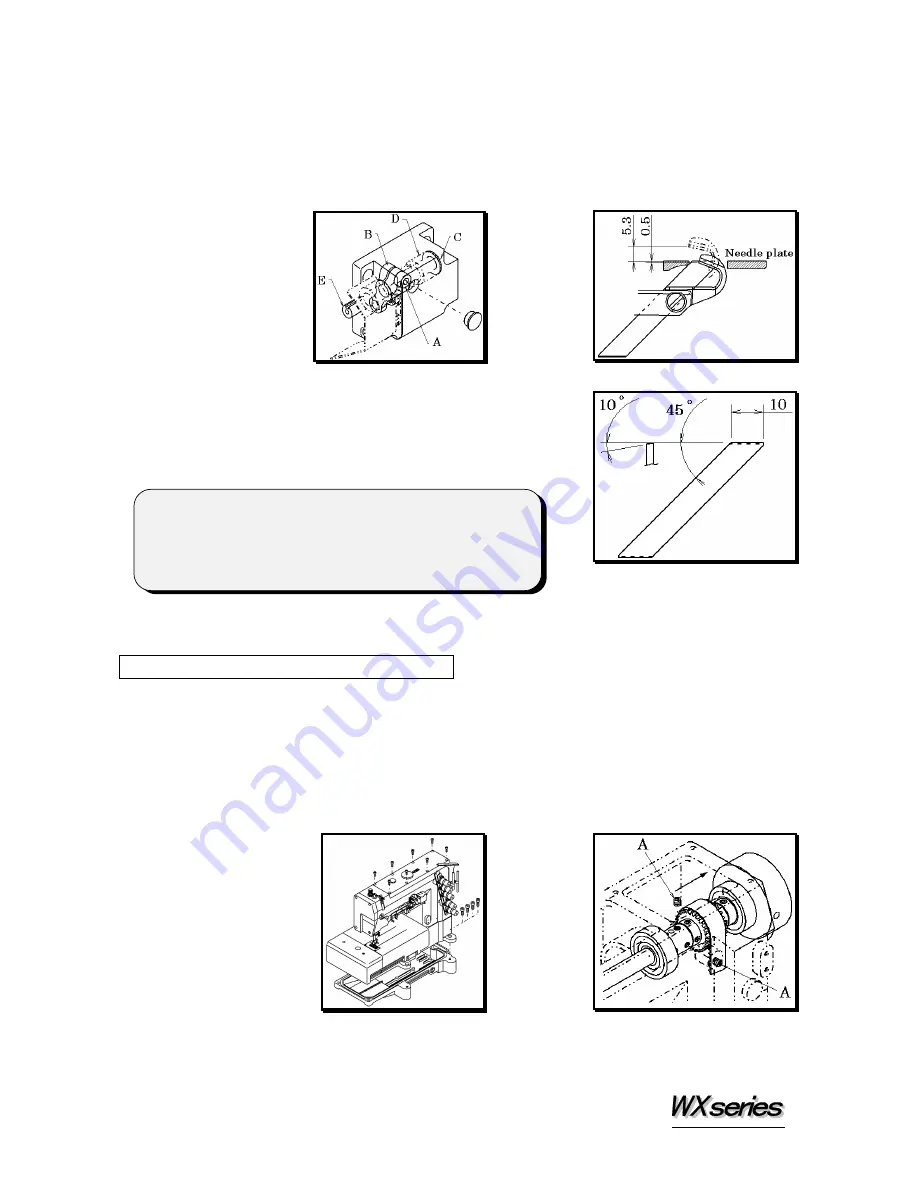
22
12-4 Overlap of the upper and lower knives
When the upper knife is at the bottom of its travel, there should be approximately 0.5mm
overlap of the upper and lower knives. To make this adjustment, loosen screw A on the
upper knife shaft lever. Then the upper knife and upper knife holder can be moved up
and down simultaneously. Tighten screw A when 0.5mm overlap of the upper and lower
knives is obtained. Secure bushing D with upper knife shaft lever B and washer C so
that there is no left-to-right shake on upper knife shaft E. Then tighten screw A.
12-5 To sharpen the knife
The upper knife is made of an extra hard alloy.
When the knives become dull, sharpen the lower knife
first (see the illustration). If cutting is still not
performed properly, replace the upper knife.
【
13
】
REPLACING THE TIMING BELT
13-1 To remove the timing belt
1.
Loosen the eight arm cover set screws and the six oil reservoir set screws (see the
illustration). Remove each part.
2.
Loosen two screws A. Remove the handwheel to the right while turning it slowly
(see the illustration).
3.
Remove the pulley, plates and bearing in sequence by referring to the illustration
below. Then remove the timing belt from the hole for the bearing.
< Note >
The max. space between the chip guard (H) and the
shooter (I) is adjusted under 8mm at the delivery of the
factory. If re-adjustment is needed due to repairing job
etc., please make sure to adjust it under 8mm.
From the library of: Superior Sewing Machine & Supply LLC