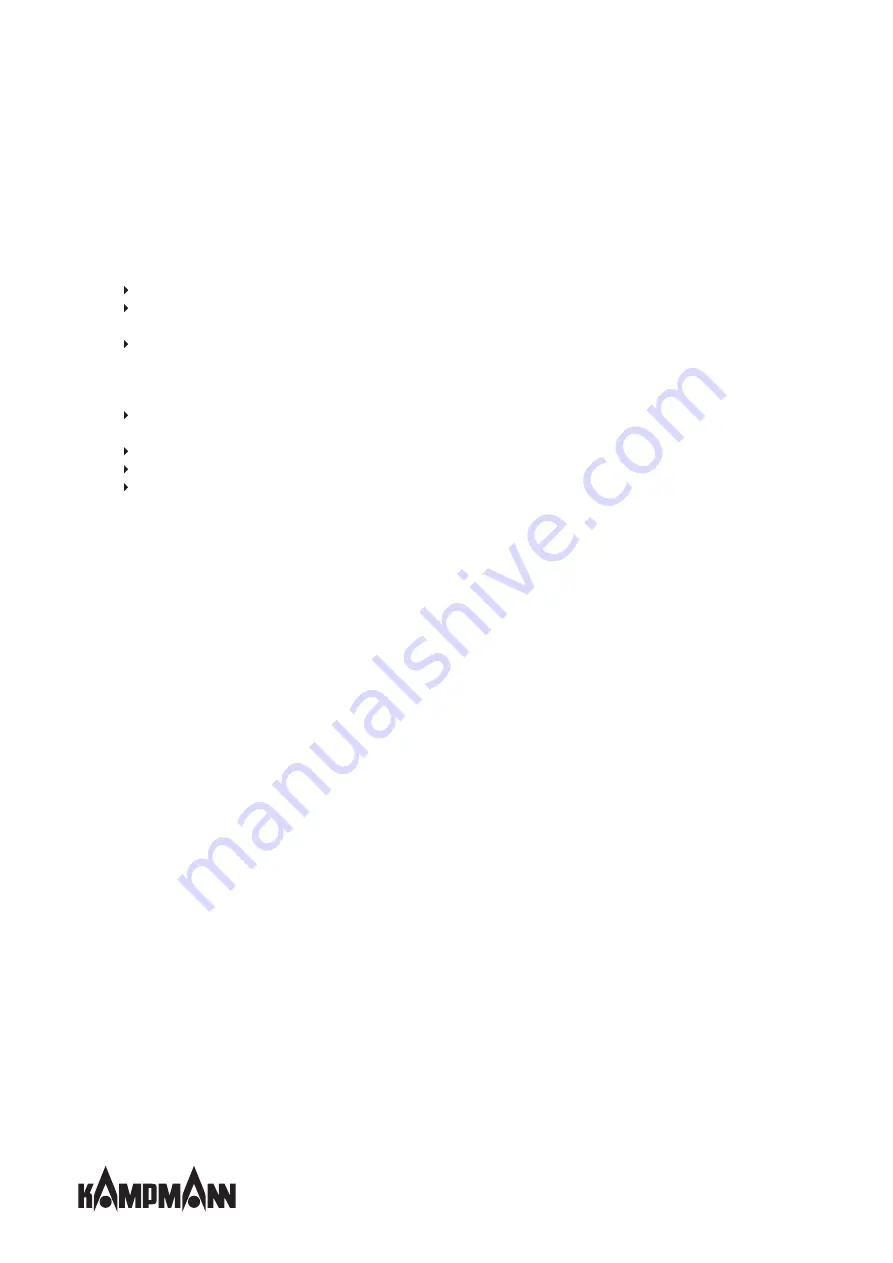
Ultra Allround
Assembly, installation and operating instructions
20
6.5
Installation
Hydraulic connection
Note the following points when connecting the hydraulic side:
Install and test safety components (expansion vessels, pressure relief valves and overflow valves).
Route condensation lines with a sufficient cross-section without bends and narrow sections with a gradient to the in situ
waste water pipe.
Allow adequate space for the air flow (air inlet and outlet).
Observe the following additional points for cooling operation:
Install continuous, vapor diffusion-tight insulation on all water-bearing components (piping, valves, connections), in each
case up to the unit.
Select suitable pipe hangers (cold clamps) for cooling operation.
Sufficiently dimension the diameter of the condensate pipe.
Protect siphons (if any) in the condensate pipe from drying out.
Summary of Contents for Ultra Allround
Page 2: ......