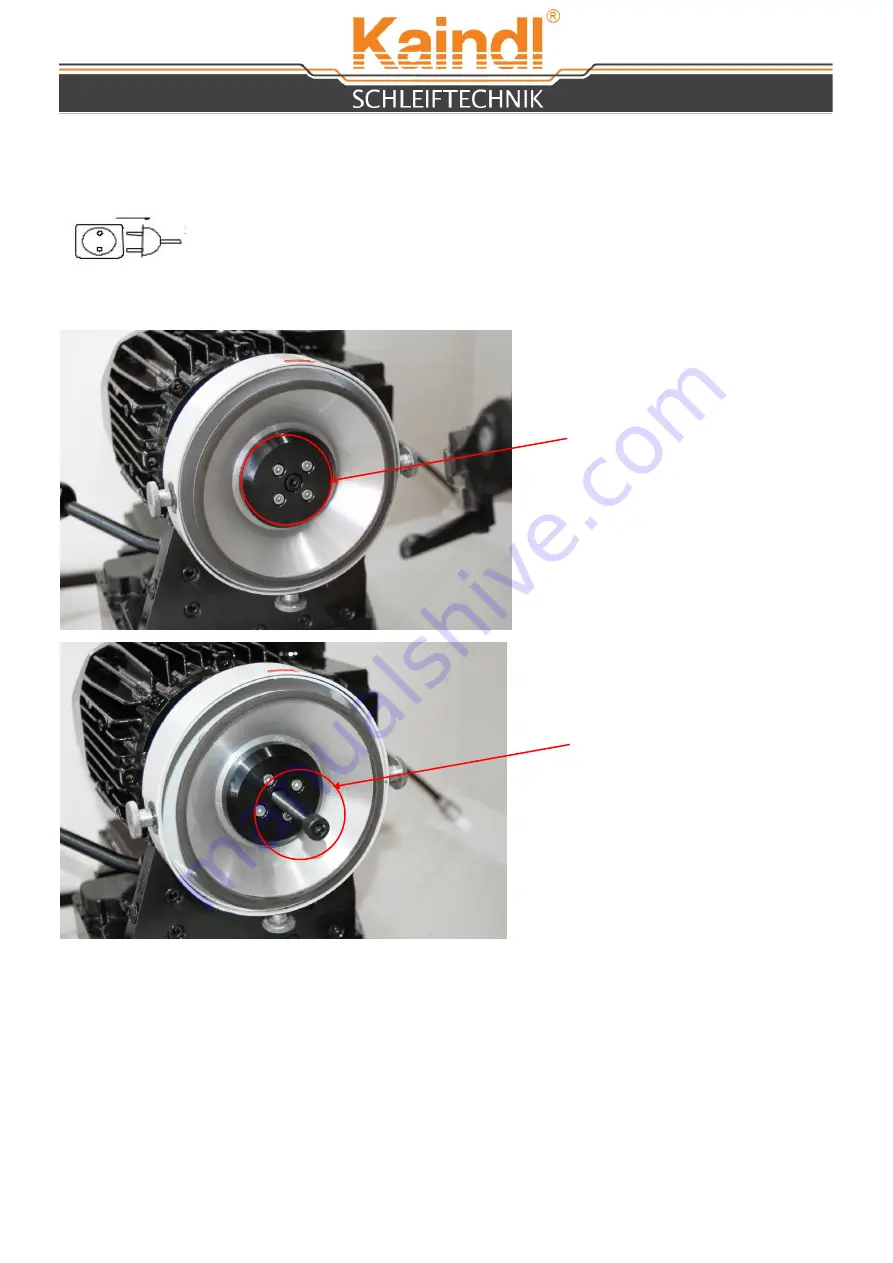
12
First unplug from electric current!
Unscrew the allen screw M6 with the supplied allen wrench SW 5.
Screw in the lifting screw M8 for lifting the grinding wheel support with the grinding wheel.
Place the new grinding wheel on the motor shaft and pay attention that the driving pin of
the grinding wheel support is placed in the groove of the motor shaft.
Now tighten the grinding wheel support with an allen wrench.
8.
CHANGE
OF
THE
GRINDING
WHEEL
Imperatively also remove the circular knife before!
Open the hexagon
screw M6
Screw in the lifting
screw M8 for lifting the
grinding wheel support
with the grinding wheel