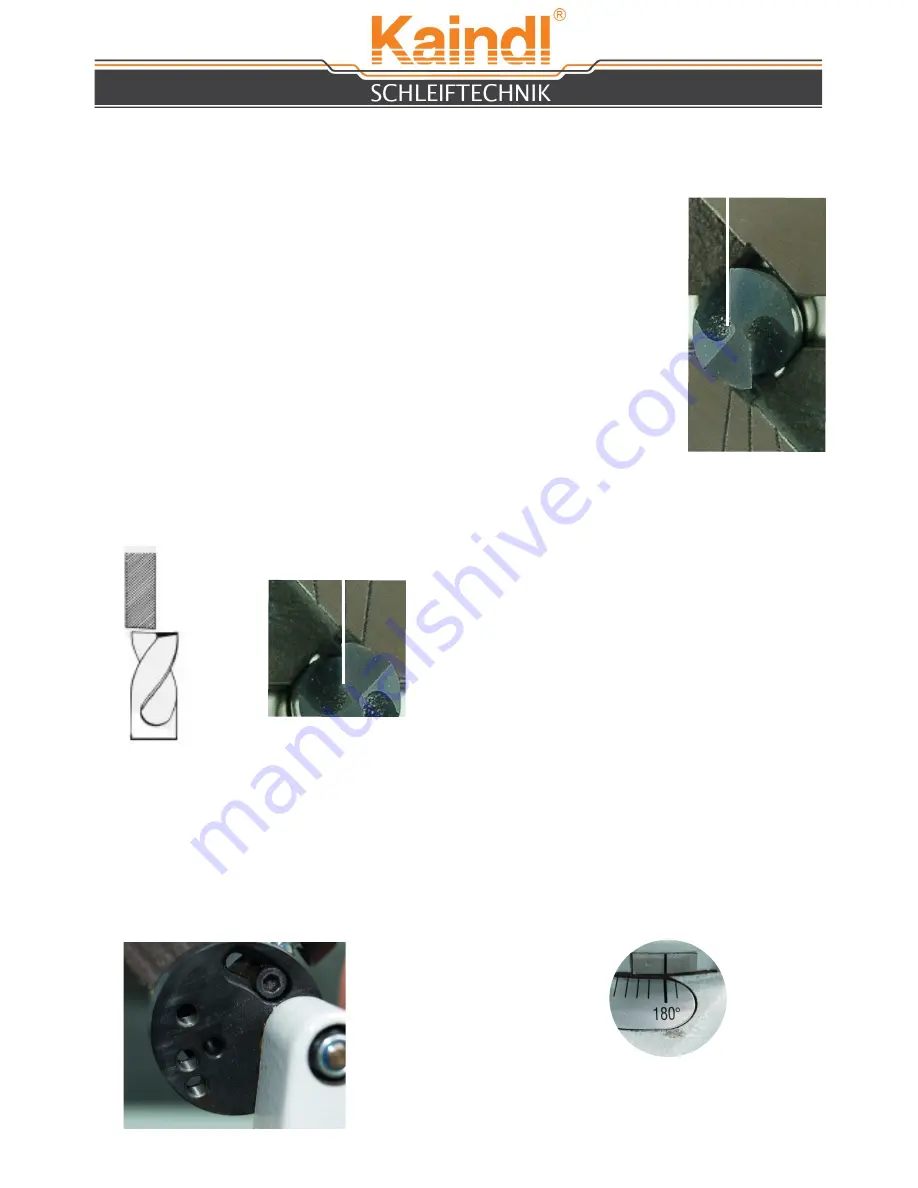
1 9
1 6.
GRINDING OF CROSS CUTTING OR
4
FACET DRILLS
1 6.1
GRINDING OF A CUTTER
Depending of the drill is made of, use the corresponding grinding wheel.
Align one cutting edge parallel to both graduation lines (see picture).
Project the drill
approx. 20 mm outside
the prism. Fix the turning
mechanism in hole
A
(see picture below).
Adjust the top and clearance angle to your specifications. Grind the first
side over the right edge of the grinding wheel by feeding the prism and
moving with the motor feed. The second side is ground with the same
adjustments. For grinding the back, fix the turning mechanism in hole
B
.
The grinding operation is the same as for the first two cutting edges.
Align the cutter to the
straight line of the prism
Cutter grinding is slightly different to cross facet grinding. But the adjustment and
alignment is identical to the 4 facet drill. The dirrerence in only the top angle adjustment.
Here use
180°185°
(see picture below).
The shaprening procedure is identical. For cutters with more then two cutting edges use
the magnetic depth stop, listed under special accessoires. For cutters with odd cutting
edges (e. g. 3-cutters) each cutting edge has to be adjust separately. Having cutters with
even numbers of cutting edges, the opposite is cutting edges can by ground by reversing.
A:
Locking for main
cutting edge
B:
Locking for free
sharpening
Prism rest
180° 185°
A
B
C