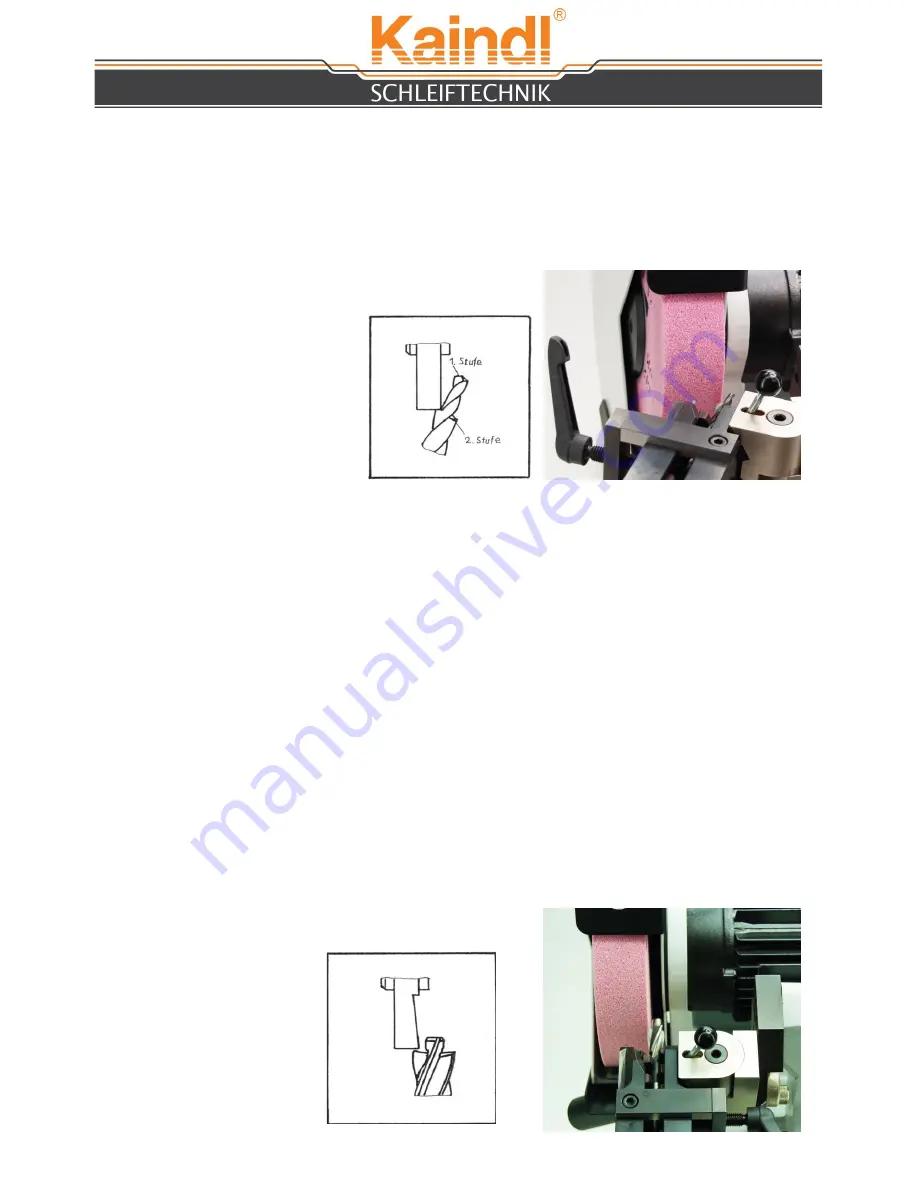
First step:
Adjust prism support to scale mark
118°
. The fixation and alignment is same
as described in page 1 0 (right hand drills).
Second step:
Adjustment as first step and sharpen
over the right edge at the
straight angle of the grinding
wheel. Clearance angle as per
your request.
13.
GRINDING OF STEPPED DRILLS
WITH
2
CUTTING EDGES
118°
14.
GRINDING OF STEPPED DRILLS
90°
First step:
The grinding is same as for right hand drills.
Second step:
For this you have to "hollow out" the right side of the grinding wheel from
the outside to the middle, in order the angle of edge of wheel is less than
90°
. Then
adjust the second step. Adjust prism support to
180°
, clearance angle to
0
. Fix star knop
screw in boring
A
. By means of motor feed form the outside to the inside and move back
when finished. Reverse the prism and repeat the grinding procedure.
15.
GRINDING OF SPOT FACERS
Hollow out the grinding wheel as described for
90° stepped drills
. Let the spot facer
project around
35 mm
outside the prism and align one cutting edge parallel to the
straight marking line. Use magnetic depth stop and cutting rost (page 8). Adjust
clearance angle to
0
and lock knob screw in boring
A
. Grind from the inside to the
outside by use of the motor feed. Move back and align the next cutting edge.
Do not change prism feed position.
For back grinding
fix the star knob screw in hole
B
and repeat the
grinding procedure as
before.
1 4