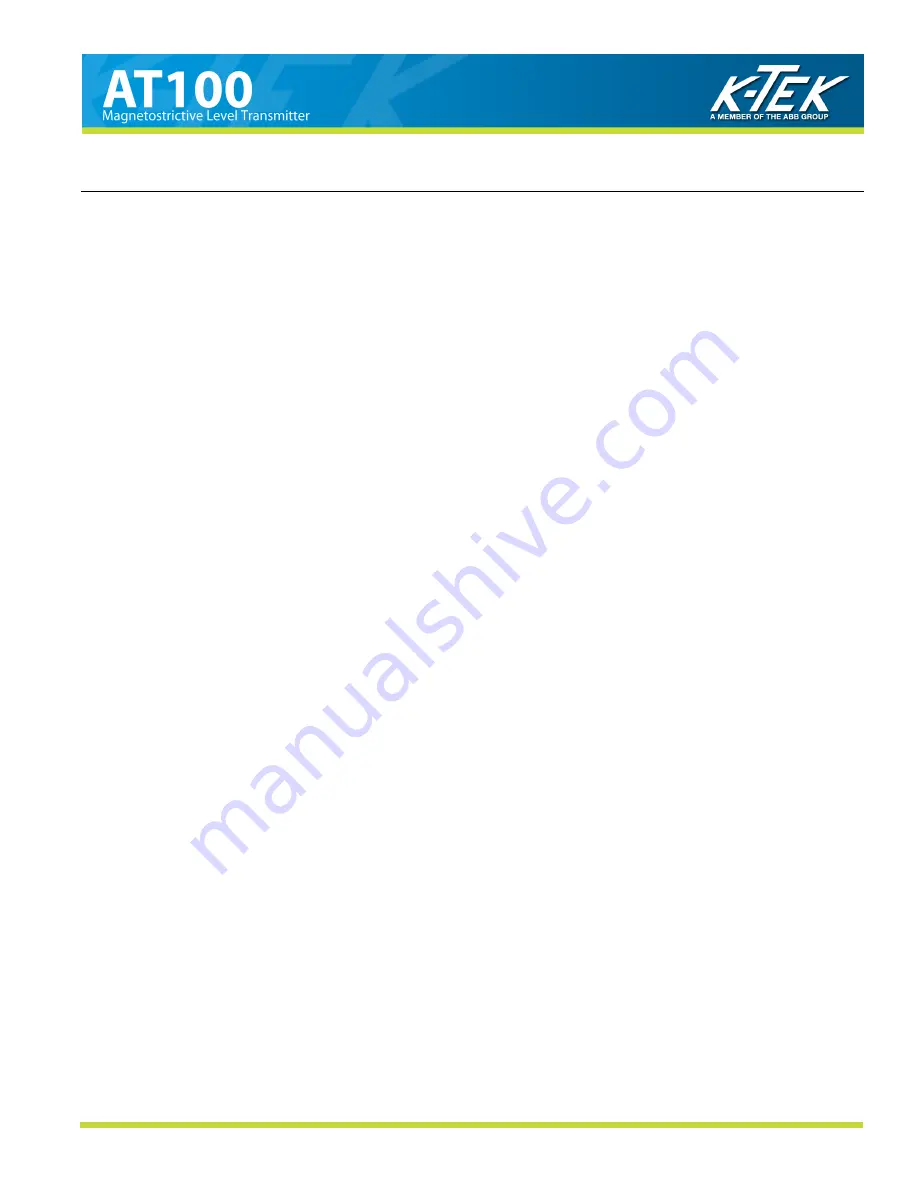
AT100-0200-1 Rev L (10-2010) DCN0528
17
5.0 COMMUNICATION OPTIONS
5.3.4 Jumper Settings
The Jumpers are located on the face of the electronic module (top left hand side) can be setup as follows:
WRITE PROTECT (right jumper)
See Document ELE1002
- When the jumper is in the lower position, the transmitter configuration cannot be changed via the LCD.
SIMULATE (left jumper)
See Document ELE1002
-The simulate jumper is used in conjunction with the Analog Input (AI) function block. This switch is used to
simulate channel output, and as a lock-out feature for the AI function block. To enable the simulate feature,
move the jumper to the lower position on the module housing.
5.3.3 Field Wiring
All power to the transmitter is supplied over the signal wiring. Signal wiring should be a shielded, twisted pair
for best results. Do not run unshielded signal wiring in conduit or open trays with power wiring or near heavy
electrical equipment.
If the sensor is installed in a high-voltage environment and a fault condition or installation error occurs, the
sensor leads and transmitter terminals could carry lethal voltages. Use extreme caution when making contact with
the leads and terminals.
Quiescent Current Consumption: 12.5mA.
Communication Mode: H1 (31.25Kbit/s Voltage Mode Signaling). All other devices on the same bus must
use the same signaling. 12 to 16 devices can be connected in parallel along the same pair of wires.
5.3.5 DD Files
The incorporation of the AT100 transmitter in a control system will require the use of specific DD files within
the host system. These files may be downloaded from www.fieldbus.org.
5.3.6 Transducer Block
The Transducer Block contains transmitter specific data regarding the setup, configuration, and indication of
the instrument. Under normal circumstances it will not be necessary to change any of the parameters in the
Transducer Block. The process data is expressed in the Transducer Block as the following:
LEVEL_VALUE_1: Level 1
LEVEL_VALUE_2: Level 2 *
TEMPERATURE_VALUE: Temperature *
LIN_VALUE_1: Linearization/Strapping Output, Level 1 *
LIN_VALUE_2: Linearization/Strapping Output, Level 2 *
* = Depending on options selected when ordering
5.3.7 Analog Input (AI) Function Blocks
The AT transmitter comes configured with 5 AI Function Blocks. Depending on the specific model, each
block can be used to access 1 of the 5 possible Transducer Block output values. The AI Blocks take data from the
Transducer Block and make it available to other blocks. To select the desired data, configure the AI.CHANNEL
parameter as follows:
AI.CHANNEL = 1: Level 1
AI.CHANNEL = 2: Level 2 *
AI.CHANNEL = 3: Temperature *
AI.CHANNEL = 4: Linearization/Strapping Output, Level 1 *
AI.CHANNEL = 5: Linearization/Strapping Output, Level 2 *
* = Depending on options selected when ordering
Summary of Contents for AccuTrak AT100
Page 1: ......
Page 29: ...AT100 0200 1 Rev L 10 2010 DCN0528 29 8 0 WIRING DIAGRAMS 8 1 FM CSA ...
Page 30: ...AT100 0200 1 Rev L 10 2010 DCN0528 30 8 1 FM CSA continued 8 0 WIRING DIAGRAMS ...
Page 31: ...AT100 0200 1 Rev L 10 2010 DCN0528 31 8 2 ATEX IEC 8 0 WIRING DIAGRAMS ...
Page 32: ...AT100 0200 1 Rev L 10 2010 DCN0528 32 8 2 ATEX IEC continued 8 0 WIRING DIAGRAMS ...
Page 33: ...AT100 0200 1 Rev L 10 2010 DCN0528 33 8 3 Typical Loop Wiring Diagram 8 0 WIRING DIAGRAMS ...
Page 36: ...AT100 0200 1 Rev L 10 2010 DCN0528 36 9 0 F1 OPTION ASSEMBLY DRAWING ...
Page 37: ...AT100 0200 1 Rev L 10 2010 DCN0528 37 10 0 SIL Certificate ...
Page 38: ...AT100 0200 1 Rev L 10 2010 DCN0528 38 10 0 SIL Certificate continued ...
Page 39: ...AT100 0200 1 Rev L 10 2010 DCN0528 39 11 0 EU DECLARATION OF CONFORMITY ...