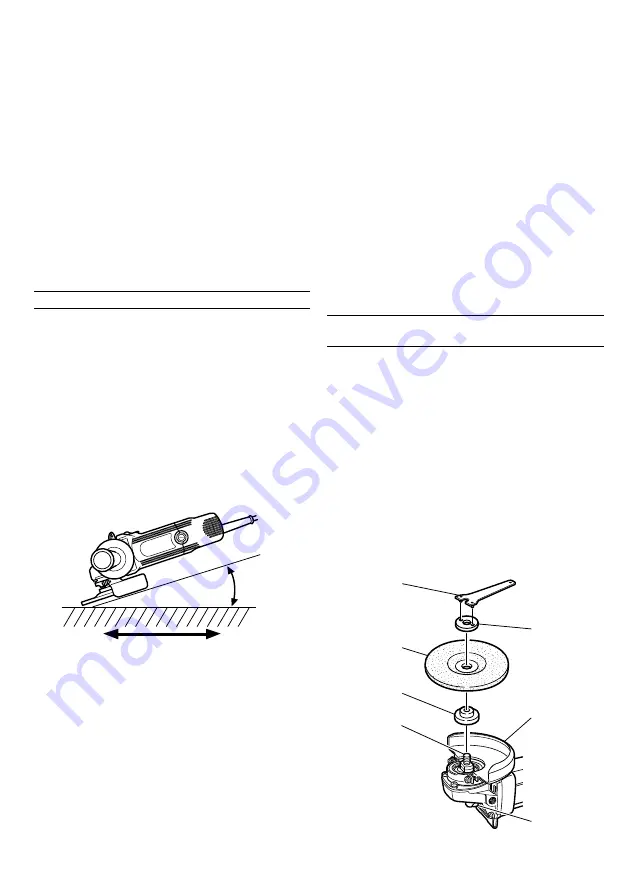
4
For tools intended to be fitted with threaded hole
wheel, ensure that the thread in the wheel is long
enough to accept the spindle length.
Do not use cutting off wheel for side grinding.
6. Conducting a trial run
Ensure that the abrasive products is correctly
mounted and tightened before use and run the tool
at no-load for 30 seconds in a safe position, stop
immediately if there is considerable vibration or if
other defects are detected.
If this condition occurs, check the machine to
determine the cause.
7. Confirm the push button.
Confirm that the push button is disengaged by
pushing push button two or three times before
switching the power tool on (See Fig. 2).
8. Fixing the side handle
Screw the side handle into the gear cover.
PRACTICAL GRINDER APPLICATION
1. Pressure
To prolong the life of the machine and ensure a
first class finish, it is important that the machine
should not be overloaded by applying too much
pressure. In most applications, the weight of the
machine alone is sufficient for effective grinding.
Too much pressure will result in reduced rotational
speed, inferior surface finish, and overloading which
could reduce the life of the machine.
2. Grinding angle
Do not apply the entire surface of the depressed
center wheel to the material to be ground. As
shown in Fig. 1, the machine should be held at an
angle of 15° – 30° so that the external edge of the
depressed center wheel contacts the material at an
optimum angle.
A
B
15
°
– 30
°
Fig. 1
3. To prevent a new depressed center wheel from
digging into the workpiece, initial grinding should
be performed by drawing the grinder across the
workpiece toward the operator (Fig. 1 direction B).
Once the leading edge of the depressed center
wheel is properly abraded, grinding may be
conducted in either direction.
4. Precautions immediately after finishing operation
The wheel continues to rotate after the tool is
switched off.
After switching off the machine, do not put it down
until the depressed center wheel has come to a
complete stop. Apart from avoiding serious
accidents, this precaution will reduce the amount
of dust and swarf sucked into the machine.
CAUTIONS
䡬
Check that the work piece is properly supported.
䡬
Ensure that ventilation openings are kept clear when
working in dusty conditions.
If it should become necessary to clear dust, first
disconnect the tool from the mains supply (use non-
metallic objects) and avoid damaging internal parts.
䡬
Ensure that sparks resulting from use do not create
a hazard e.g. do not hit persons, or ignite flammable
substances.
䡬
Always use protective safety glasses and hearing
protectors, use other personal protective equipment
such as gloves, apron and helmet when necessary.
䡬
Always use eye and ear protection.
Other personal protective equipment such as dust
mask, gloves, helmet and apron should be worn
when necessary.
If in doubt, wear the protective equipment.
䡬
When the machine is not use, the power source
should be disconnected.
ASSEMBLING AND DISASSEMBLING THE
DEPRESSED CENTER WHEEL (Fig. 2)
CAUTION Be sure to switch OFF and disconnect the
attachment plug from the receptacle to avoid
a serious accident.
1. Assembling (Fig. 2)
(1) Turn the disc grinder upsidedown so that the spindle
is facing upward.
(2) Align the across flats of the wheel washer with the
notched part of the spindle, then attach them.
(3) Fit the protuberance of the depressed center wheel
onto the wheel washer.
(4) Screw the wheel nut onto the spindle.
(5) While pushing the push button with one hand, lock
the spindle by turning the depressed center wheel
slowly with the other hand.
Tighten the wheel nut by using the supplied wrench
as shown in Fig. 2.
2. Disassembling
Follow the above procedures in reverse.
Fig. 2
Wrench
Depressed
center wheel
Wheel nut
Wheel washer
Spindle
Wheel guard
Push button
Summary of Contents for EGA100
Page 7: ...7 ...