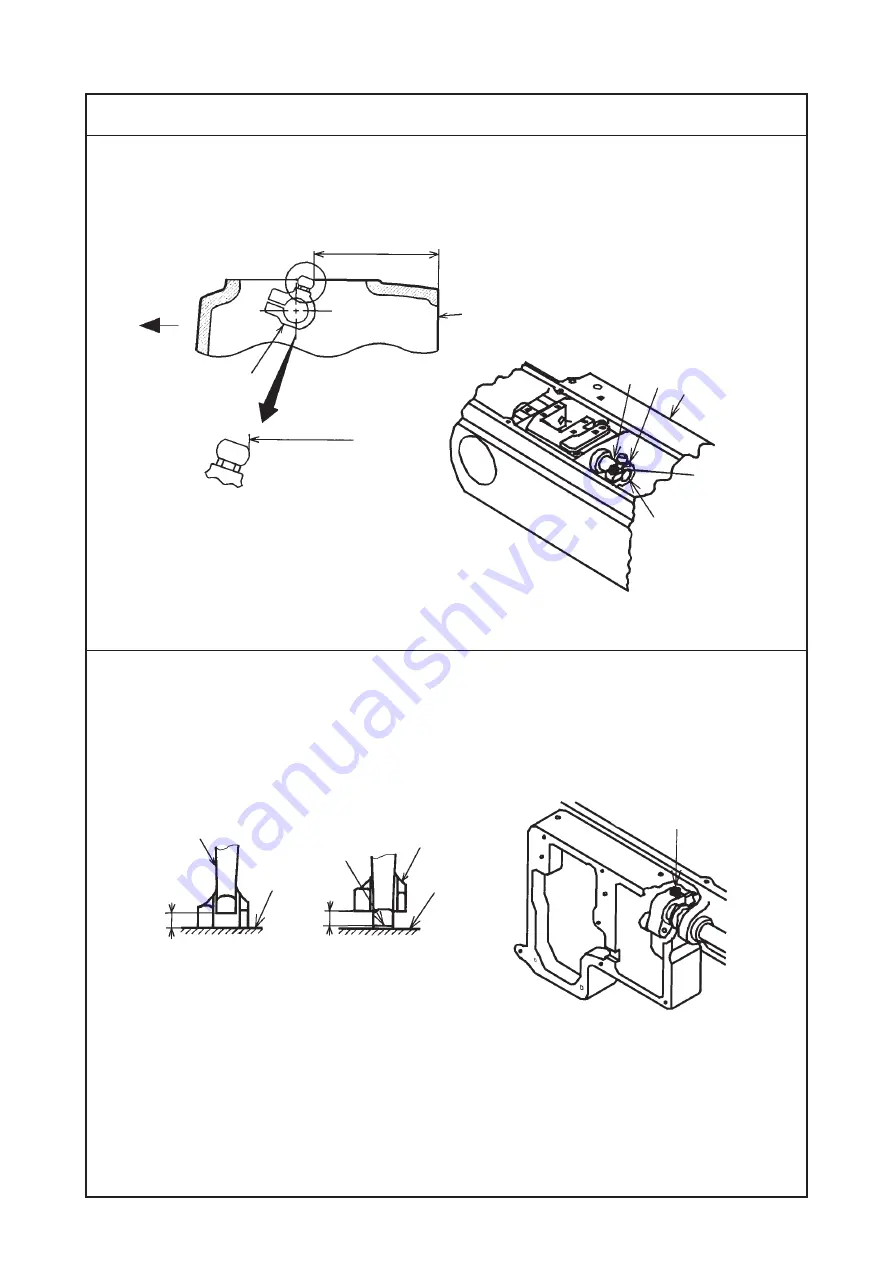
– 16 –
Standard Adjustment
(11) Feed motion
1) Amount of alternate vertical movement (position of the vertical adjusting arm)
1
2
2) Alternate momentum
1
2
3
A
B
Top surface of
feed dog
Top surface of
throat plate
Top surface of
throiat plate
Conditions
• Feed amount : 0 mm
• Amount of alternate vertical movement : standard
1
4
3
73 to 74 mm
Operator’s
side
Edge of
machine arm
To align
with edge
73 to 74 mm