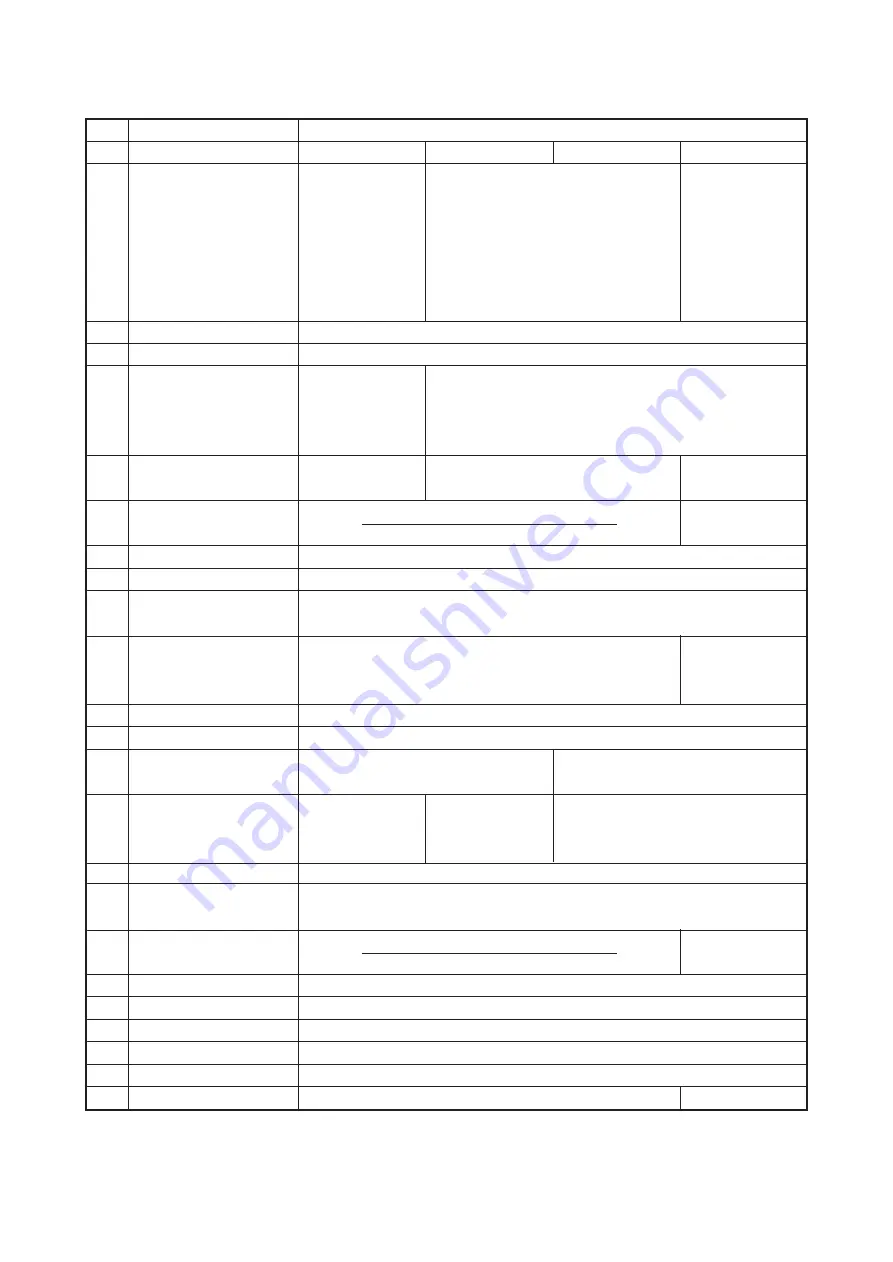
−
1
−
1. SPECIFICATIONS
No.
1
2
3
4
5
6
7
8
9
10
11
12
13
14
15
16
17
18
19
20
21
22
23
24
Item
Model
Model name
Application
Sewing speed
Needle
Thread possible to be
sewn
Thread possible to be
trimmed
Stitch length
Presser foot lift
Stitch length adjusting
mechanism
Reverse stitch adjusting
method
Thread take-up
Needle bar stroke
Alternate foot stroke
Hook
Feed mechanism
Top and bottom feed
actuation mechanism
Thread trimming
mechanism
Lubrication
Lubricating oil
Cylinder bed diameter
Free space for sewing
Size of handwheel
Motor
Specifications
LS-1341
LS-1342
LS-1342-7
Cylinder-Bed, 1-
Needle, Unison
Feed, Lockstitch
M a c h i n e w i t h
A u t o m a t i c
Thread Trimmer
(Large Hook)
Cylinder-Bed, 1-Needle, Unison
Feed, Lockstitch Machine
(Large Hook)
For heavy-weight materials
Max. 2,500 rpm
#50 to #8
#40 to #5
#30 to #5
#30 to #5
Max. 6 mm (normal/reverse feed)
Hand lifter : 9 mm Knee lifter : 16 mm
By dial
Lever type
Slide thread take-up
36 mm
Ellipse feed
Timing belt
Central oil wick lubrication by tank (partially by manual)
JUKI New Defrix Oil No. 2 (equivalent to ISO VG32)
72mm
255 x 100 mm
V belt effective diameter : ø93.3 mm Outer diameter : ø160 mm
4P, 400W
SC-380
SCHMETZ 135 X 17 Nm 100 to 180 Standard : Nm 160
Air cylinder type
(with touch-back
switch)
2.5 mm to 6.5 mm Slot adjusting type
1 mm to 6.5 mm Alternate foot stroke
adjusted by dial
Full-rotary vertical-
axis standard hook
(Latch type)
Full-rotary vertical-
axis 1.6-fold hook
(Cap type)
Full-rotary vertical-axis 1.6-fold hook
(Latch type)
Cam-driven
scissors type
LS-1340
Cylinder-Bed, 1-
Needle, Unison
Feed, Lockstitch
Machine
(Standard Hook)
SCHMETZ 135
X 17 Nm 100 to
180 Standard :
Nm 140
Summary of Contents for LS-1340
Page 53: ... 53 ...
Page 54: ... 54 ...