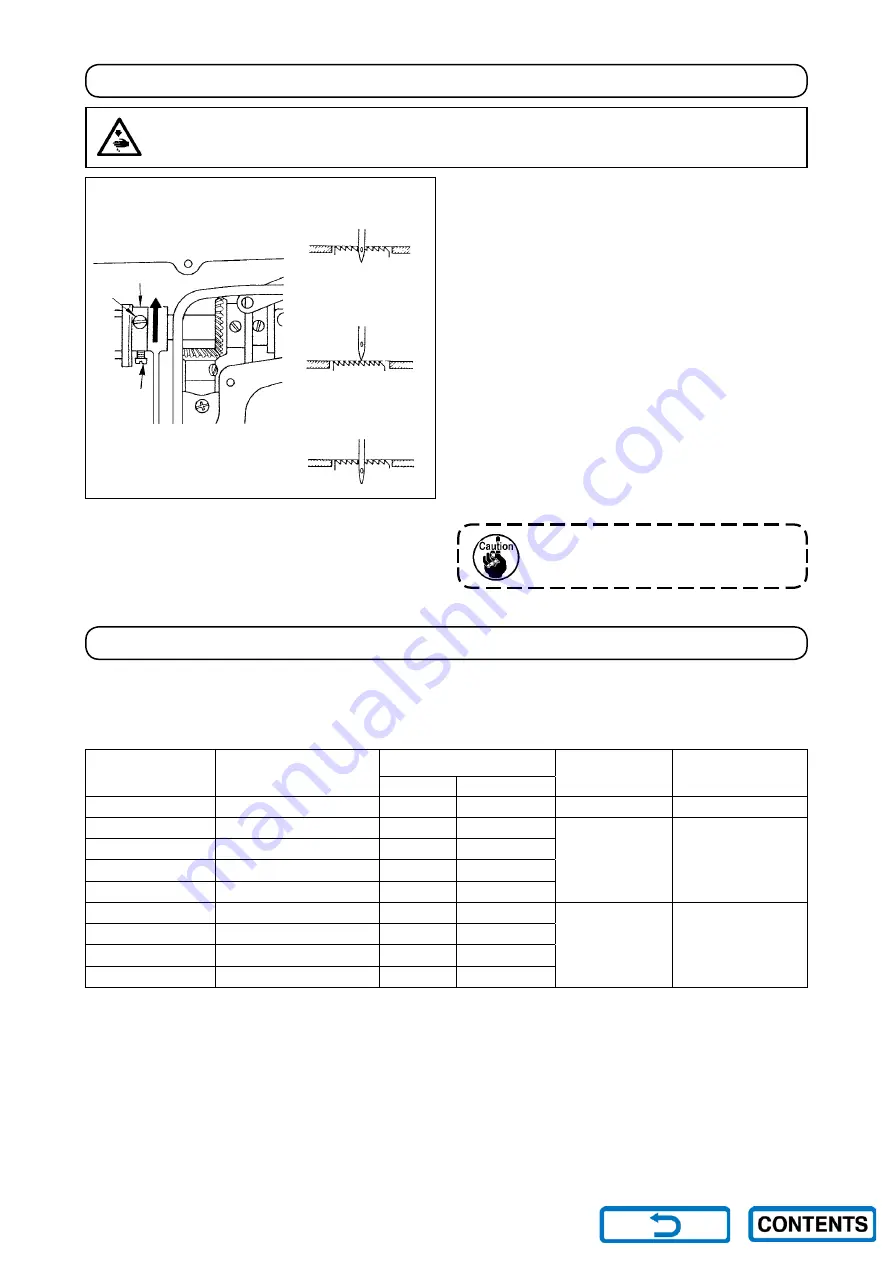
– 2 –
22. Motor PuLLEYs anD BELts
1) A clutch motor with 400W output (1/2 HP) is used as the standard motor.
2) An M-type V belt should be used.
3) The relatonshp between the motor pulleys, belt lengths and sewng speeds s shown n the followng
table :
* the effective diameter of a motor pulley is equivalent to the outside diameter minus 5 mm.
* the motor should rotate counterclockwise as observed from the handwheel side. Be careful
not to allow the motor to rotate in the reverse direction.
) Loosen screws
2
and
3
n feed eccentrc cam
1
,
move the feed eccentrc cam n the drecton of
the arrow or opposte drecton of the arrow, and
firmly tighten the screws.
2) For the standard adjustment, adjust so that the
top surface of feed dog and the top end of needle
eyelet are flush wth the top surface of throat
plate when the feed dog descends below the
throat plate.
3) To advance the feed tmng n order to prevent
uneven materal feed, move the feed eccentrc
cam n the drecton of the arrow.
4) To delay the feed timing in order to increase stitch
tghtness, move the feed eccentrc cam n the op
-
poste drecton from the arrow.
Be careful not to move the feed eccen-
tric cam too far,or else needle break-
age may result.
21. aDJustInG tHE FEED tIMInG
WarnInG :
to avoid possible personal injury due to abrupt start of the machine, turn off the power to the
machine and check to be sure that the motor has totally stopped rotating in prior.
standard feed timing
advanced feed
timing
Delayed feed timing
1
3
2
Motor pulley
o.D. (mm)
Motor pulley part no.
sewing speed (sti/min)
Belt length
Belt part no.
50 Hz
60 Hz
110
MTKP0105000
4,440
-
1092 mm (43")
MTJVM004300
105
MTKP0100000
4,250
-
1067 mm (42")
MTJVM004200
100
MTKP0095000
4,000
-
95
MTKP0090000
3,820
-
90
MTKP0085000
3,610
4,320
85
MTKP0080000
3,390
4,000
1041 mm (41")
MTJVM004100
80
MTKP0075000
3,160
3,790
75
MTKP0070000
2,950
3,520
70
MTKP0065000
2,740
3,260