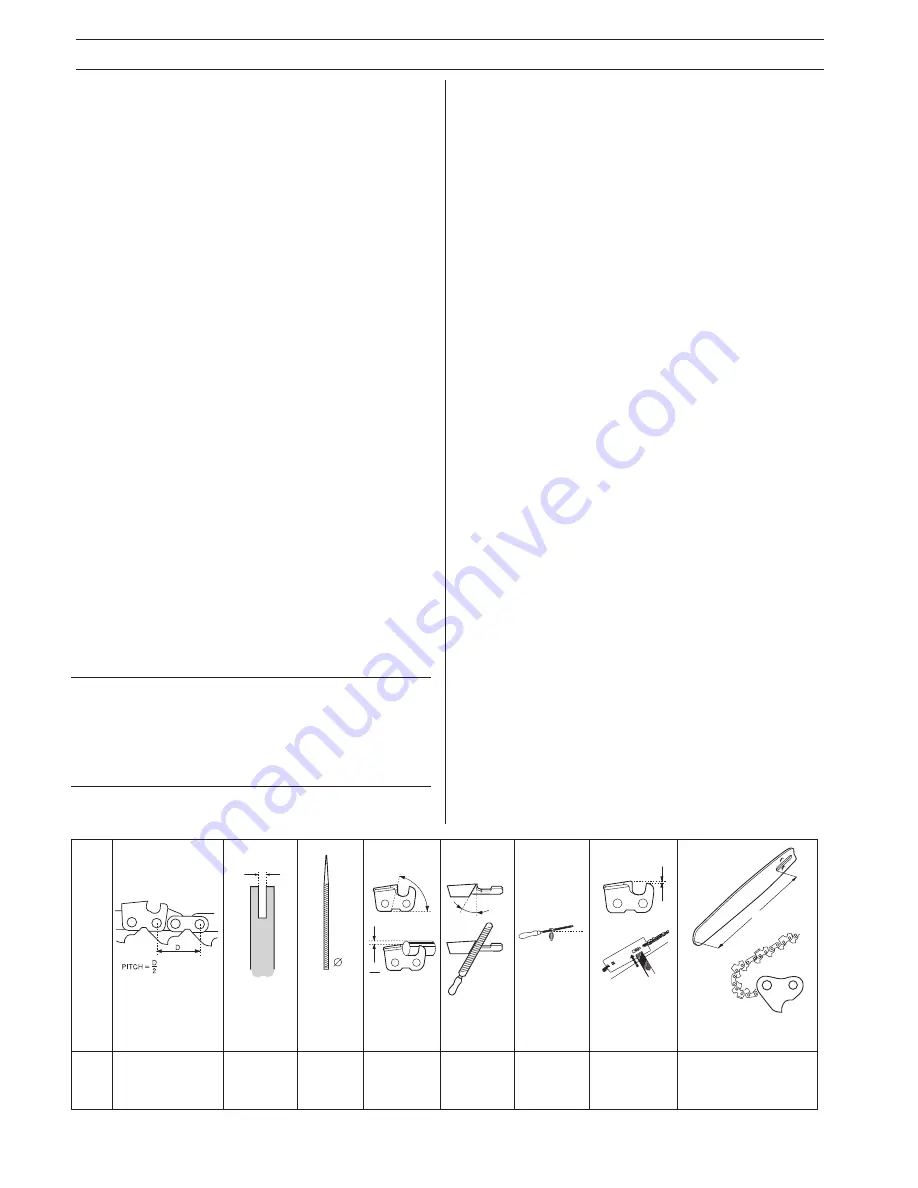
34
– English
Bar and chain combinations
The following combinations are CE approved.
Bar
Chain
Length,
Pitch,
Max.
inches
inches
tip radius
18
3/8
11T
Jonsered S42, Oregon 73VL
20
3/8
11T
Jonsered S42, Oregon 73VL
24
3/8
11T
Jonsered S42, Oregon 73VL
28
3/8
11T
Jonsered S42, Oregon 73VL
20
3/8
34mm
Jonsered S42, Oregon 73VL
24
3/8
34mm
Jonsered S42, Oregon 73VL
28
3/8
34mm
Jonsered S42, Oregon 73VL
Noise emissions
(see note 1)
Sound power level, measured
dB(A)
Sound power level, guaranteed
L
WA
dB(A)
Sound levels
(see note 2)
Equivalent sound pressure
level at operator’s ear,
measured according to relevant
international standards, dB(A)
Vibration levels
(see note 3)
Front handle m/s
2
Rear handle m/s
2
Chain/bar
Standard bar length,
inches/cm
Recommended bar lengths,
inches/cm
Usable cutting length
inches/cm
Chain speed at max.
power, m/sec
Pitch, inches
Thickness of drive link,
inch/mm
Number of teeth on drive
sprocket
Engine
Cylinder volume, cu. in/cm
3
Cylinder bore, inch/mm
Stroke, inch/mm
Idle speed, rpm
Recommended max.
speed, unloaded, rpm
Power, kW/rpm
Ignition system
Manufacture
Type of ignition system
Spark plug
Electrode gap, inch/mm
Fuel and lubrication
system
Manufacturer
Carburettor type
Fuel capacity, litre/US pint
Oil pump capacity at 6000 rpm,
ml/min
Oil capacity, litre/US pint
Type of oil pump
Weight
Without bar and chain, kg/LBS
TECHNICAL DATA
2095
5,7/93,6
0,22/56
0,15/38
2 400
13 000
4,9/ 9 000
Electrolux
ET
NGK BPMR7A/
Champion RCJ 6Y
0,020/0,5
Tillotson
H265A
0,87/1,8
9,0–22,0
0,65/1,4
Automatic
8,2/18
2095
114
115
101
5,3
10,3
20"/51
18"/46 20"/51 24"/61 28"/71
17"/43 19"/48 23"/91 27"/69
21,5
3/8
1,5
7
1
5
L
Type
Inch
Inch/mm
Inch/mm
Degree
Degree
Degree
Inch/mm
Inch/cm: dl
S42/
3/8
0,058/1,5
7/32 / 5,5
60°
25°
10°
0,025/0,065
18/46:68 20/51:72
73VL
24/61:84 28/71:92
Note 1: Noise emissions in the environment measured as sound
power (L
WA
) in conformity with EC directive 2000/14/EC.
Note 2: Equivalent sound pressure level, according to ISO
7182, is calculated as the time-weighted energy total for sound
pressure levels under various working conditions with the
following time distribution: 1/2 idling, 1/2 max. load.
Note 3: Equivalent vibration level, according to ISO 7505, is
calculated as the time-weighted energy total for vibration levels
under various working conditions with the following time
distribution: 1/2 idling, 1/2 max. load.
´*xsJ¶6!¨
Summary of Contents for 2077
Page 36: ...108 88 34 26 xsJ 6 2002W03...