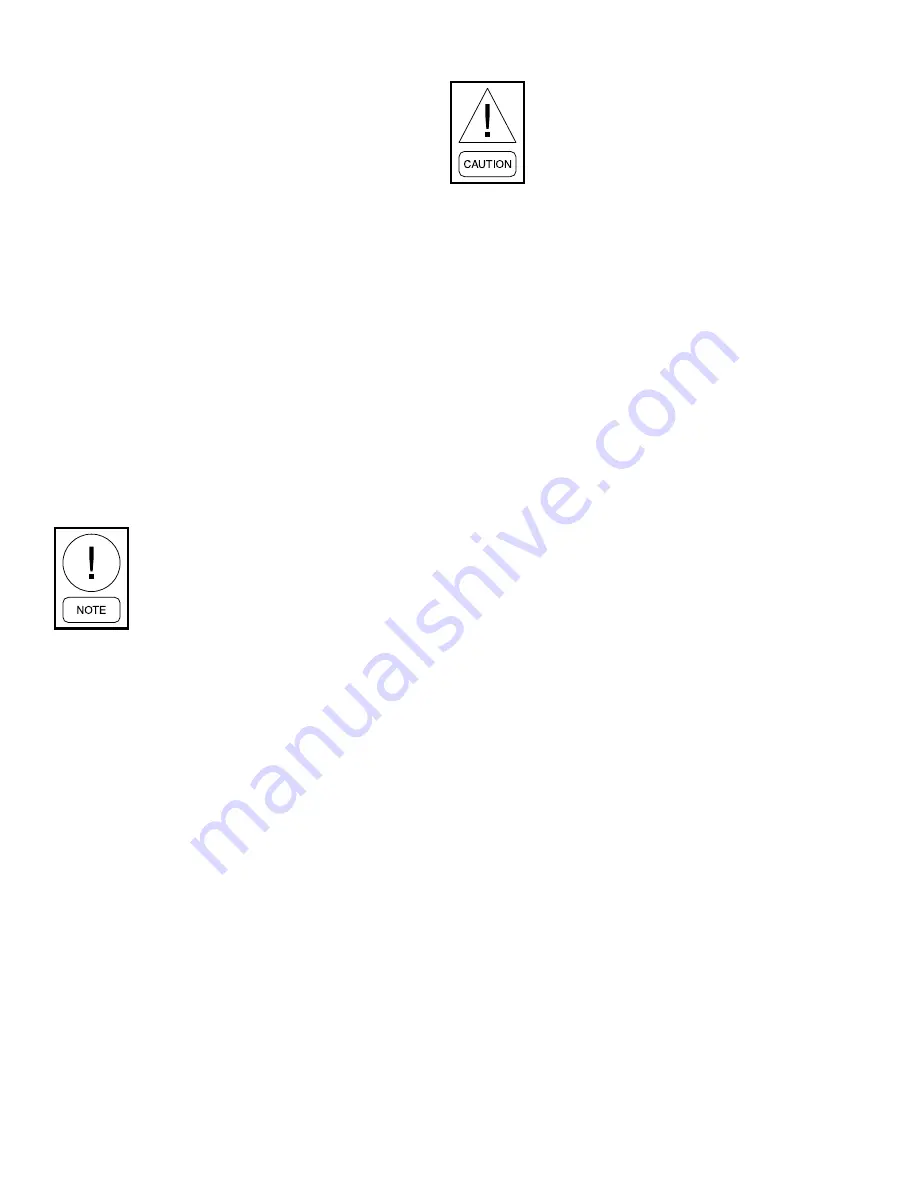
JOHNSON CONTROLS
34
FORM 150.27-NM1
ISSUE DATE: 09/30/2015
SECTION 4 – INSTALLATION
The concrete base must capable o f supporting 150% of
the operating weight. In case of upper floors, the unit
and piping should be isolated from walls and ceiling.
The unit may be bolted to the foundation using 1/2"
(13 mm) dia. holes in the base of the framework. When
lower transmitted vibration levels are required optional
anti-vibration isolators can be supplied loose for site
installation.
INSTALLATION OF VIBRATION ISOLATORS
An optional set of vibration isolators can he supplied
loose with each unit
(
refer to
CAL DATA for details).
CHILLED LIQUID PIPEWORK CONNECTION
General Requirements
The following piping recommendations are intended
to ensure satisfactory operation of the unit. Failure to
follow these recommendations could cause damage to
the unit, or loss of performance, and may invalidate the
warranty.
The maximum flow rate and pressure drop
for the cooler and condenser must not be
exceeded at any time. Refer to Section 5
Technical Data for details.
The water must enter the heat exchanger(s) by the in-
let connection. Refer to
DATA for details.
A flow switch or differential switch must be installed
in the customer pipework at the outlet of the exchang-
ers as shown in the arrangement diagrams, and wired
back to the control panel using screened cable. There
should be a straight horizontal run of at least five diam-
eters on each side of the switch. Adjust the flow switch
paddle to the size of the pipe in which it is to be in-
stalled
(see manufacturer’s instructions furnished with
the switch).
The switch is to be wired to terminals 13
– 14 of CTBl located in the control pane1, as shown on
the unit wiring diagram. This is to prevent damage to
the exchanges caused inadequate liquid flow.
The flow switch used must have gold
plated contacts for low voltage/current op-
eration. Paddle type flow switches suitable
for 150 PSIG (10 barg) working pressure
and having 1" N.P.T. connection can be
obtained from Johnson Controls as an
option for the unit.
•
The liquid pump(s) installed in the pipework
system(s) should discharged directly into the unit
heat exchanger section of the system. The pump(s)
require an auto-starter (by others) to be wired to
the control panel.
For details refer to “Electrical
Connection”.
•
All chilled liquid piping should he thoroughly
flushed to free it from foreign material before
the system is placed into operation. Use care not
to flush any foreign material into or through the
cooler.
• Pipework and fittings must he separately support
-
ed to prevent any loading on the heat exchanger(s).
Flexible connections are recommended which
will also minimize transmission of vibrations to
the building. Flexible connections must he used
if the unit is mounted on anti-vibration mounts
as some movement of the unit can he expected in
normal operation.
• Pipework and fittings immediately next to the heat
exchangers should he readily de-mountable to en-
able cleaning prior to operation, and to facilitate
visual inspection of the exchanger nozzles.
•
Each heat exchanger must be protected by a
strainer, preferably of 40 mesh, fitted as close as
possible to the liquid inlet connection in both the
evaporator and condenser water lines and provid-
ed with a means of local isolation.
•
The heat exchanger(s) must not he exposed to
flushing velocities or debris released during flush
-
ing. It is recommended that a suitably sized by-
pass and valve arrangement is installed to allow
flushing of the pipework system. The bypass can
he used during maintenance to isolate the heat ex-
changer with-out disrupting flow to other units.