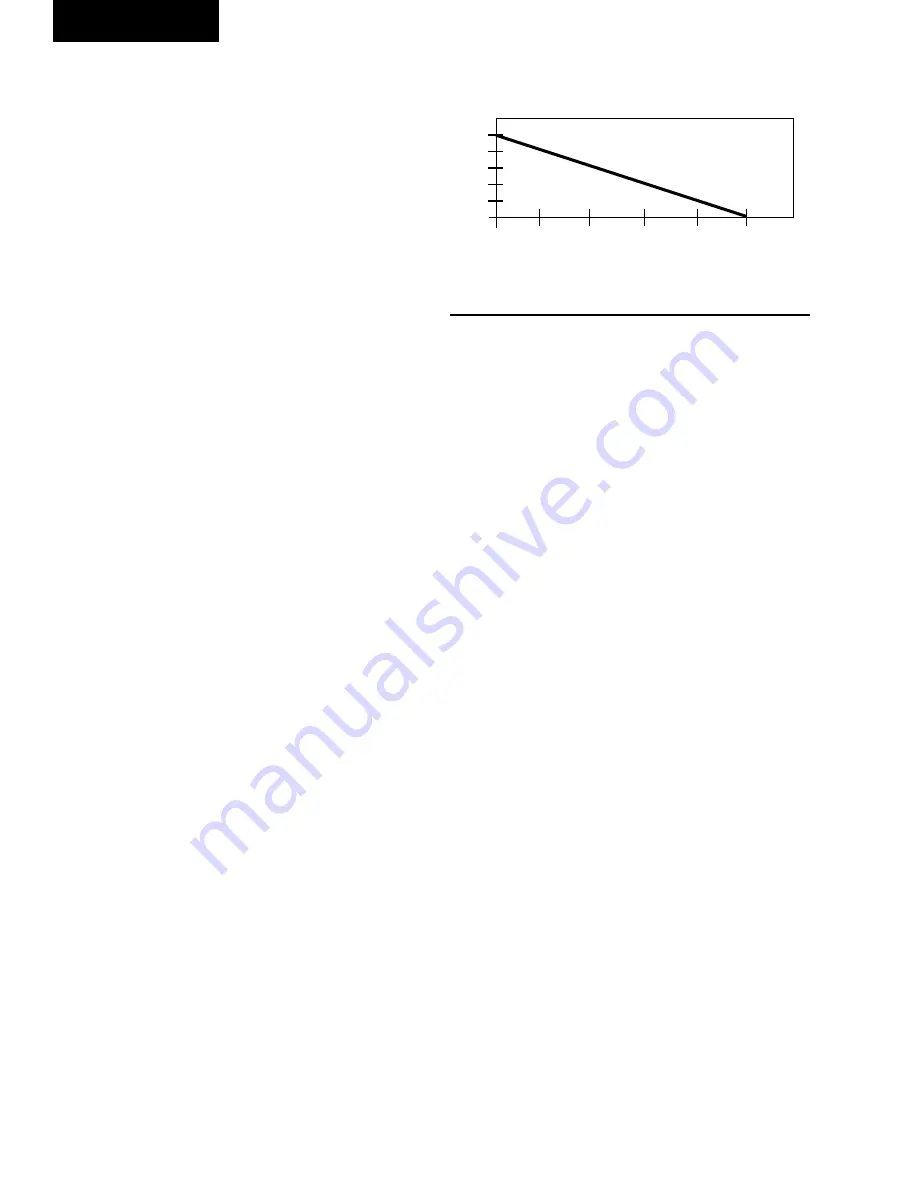
JOHNSON CONTROLS
156
FORM 150.72-NM1 (1020)
Unit Operation
0
1
2
3
4
5
6
LAST RUN TIME OF LEAD SYSTEM (MINUTES)
SETPOINT
ADJUST
(DEG. F)
6
5
4
3
2
1
0
FIG. 27 – SETPOINT ADJUST
LD11415
at a rate of 20 seconds. If the chilled liquid temperature
falls to a value greater than 1.5 °F (.83 °C) below the
Setpoint Low Limit, unloading occurs at a rate of 10
seconds. If the chilled liquid temperature falls below
1 °F above the low chilled liquid temperature cutout,
unloading occurs at a rate of 10 seconds if it is greater
than 10 seconds.
In water cooling mode on R-410A chillers, the minimum
low limit of the control range will be 40.0ºF. For leaving
chilled liquid temperature setpoint and control range
combinations that result in the low limit of the control
range being below 40.0ºF, the low limit will be reset
to 40.0ºF and the difference will be added to the high
limit. This will result in a control range the same size as
programmed but not allow the unit to run below 40.0ºF.
This control will not affect glycol chillers.
Hot gas, if present, will be the final step of capacity.
Hot gas is energized when only a single compressor
is running and LWT is less than SP. Hot gas is turned
off as temperature rises when LWT is more than SP +
CR/2. If temperature remains below the setpoint low
limit on the lowest step of capacity, the microprocessor
will close the liquid line solenoid, after turning off hot
gas, and pump the system down before turning off the
last compressor in a system.
The leaving chilled liquid setpoint is programmable from
40 °F to 70 °F (4.4 °C to 21.1 °C) in water chilling mode
and from 10 °F to 70 °F (-12.2 °C to 21.1 °C) in glycol
chilling mode. In both modes, the cooling range can be
from plus or minus1.5 °F to plus or minus2.5 °F (plus or
minus.83 °C to 1.39 °C).leaving chilled liquid control
LEAVING CHILLED LIQUID CONTROL
OVERRIDE TO REDUCE CYCLING
To avoid compressor cycling the microprocessor will
adjust the setpoint upward temporarily. The last run
time of the system will be saved. If the last run time
was greater than 5 minutes, no action is to be taken.
If the last run time for the lead system was less than 5
minutes, the microprocessor will increase the setpoint
high limit according to Fig 27, with a maximum value
allowed of 5 °F
.
If adding the setpoint adjust value to the setpoint high
limit causes the setpoint high limit to be greater than 50
°F, the setpoint high limit will be set to 50 °F, and the
difference will be added to the setpoint low limit.
Once a system runs for greater than 5 minutes, the
setpoint adjust will be set back to 0. This will occur
while the system is still running.
LEAVING CHILLED LIQUID SYSTEM LEAD/
LAG AND COMPRESSOR SEQUENCING
A Lead/Lag option may be selected to help equalize
average run hours between systems with 2 refrigerant
systems. This may be programmed under the OPTIONS
key. Auto Lead/Lag allows automatic Lead/Lag of
the two systems based on average run hours of the
compressors in each system. Manual Lead/Lag selects
specifically the sequence which the microprocessor
starts systems.
On a hot water start, once a system starts, it will turn on all
compressors before the next system starts a compressor.
The microprocessor will sequence compressors within
each circuit to maximize individual compressor run time
on individual compressors within a system to prevent
short cycling.
Each compressor in a system will be assigned an
arbitrary priority number 1, 2, or 1, 2, 3. The non-running
compressor within a system with the lowest priority
number will always be the next compressor to start. The
running compressor with priority number 1 will always
be the next to shut off. Whenever a compressor is shut
off, the priority numbers of all compressors will be
decreased by 1 with wrap-around. This control scheme
assures the same compressor does not repeatedly cycle
on and off.
Once the second system starts a compressor on a 2
system chillers, the microprocessor will attempt to
equally load each system as long as the system is not
limiting or pumping down. Once this occurs, loading and
unloading will alternate between systems, loading the
lead system first or unloading the lag system first.
Summary of Contents for YORK Tempo YLAA Series
Page 4: ...JOHNSON CONTROLS 4 FORM 150 72 NM1 1020 THIS PAGE INTENTIONALLY LEFT BLANK...
Page 12: ...JOHNSON CONTROLS 12 FORM 150 72 NM1 1020 THIS PAGE INTENTIONALLY LEFT BLANK...
Page 14: ...JOHNSON CONTROLS 14 FORM 150 72 NM1 1020 THIS PAGE INTENTIONALLY LEFT BLANK...
Page 18: ...JOHNSON CONTROLS 18 FORM 150 72 NM1 1020 THIS PAGE INTENTIONALLY LEFT BLANK...
Page 36: ...JOHNSON CONTROLS 36 FORM 150 72 NM1 1020 THIS PAGE INTENTIONALLY LEFT BLANK...
Page 49: ...FORM 150 72 NM1 1020 49 JOHNSON CONTROLS THIS PAGE INTENTIONALLY LEFT BLANK...
Page 71: ...FORM 150 72 NM1 1020 71 JOHNSON CONTROLS THIS PAGE INTENTIONALLY LEFT BLANK...
Page 73: ...FORM 150 72 NM1 1020 73 JOHNSON CONTROLS 5 5...
Page 75: ...FORM 150 72 NM1 1020 75 JOHNSON CONTROLS 5 5...
Page 77: ...FORM 150 72 NM1 1020 77 JOHNSON CONTROLS 5 5...
Page 79: ...FORM 150 72 NM1 1020 79 JOHNSON CONTROLS 5 5...
Page 81: ...FORM 150 72 NM1 1020 81 JOHNSON CONTROLS 5 5...
Page 83: ...FORM 150 72 NM1 1020 83 JOHNSON CONTROLS 5 5...
Page 85: ...FORM 150 72 NM1 1020 85 JOHNSON CONTROLS 5 5 LD13901...
Page 87: ...FORM 150 72 NM1 1020 87 JOHNSON CONTROLS 5 5...
Page 89: ...FORM 150 72 NM1 1020 89 JOHNSON CONTROLS 5 5 LD13232...
Page 91: ...FORM 150 72 NM1 1020 91 JOHNSON CONTROLS THIS PAGE INTENTIONALLY LEFT BLANK...
Page 92: ...JOHNSON CONTROLS 92 FORM 150 72 NM1 1020 Technical Data WIRING LD13238 FIG 22 WIRING...
Page 93: ...FORM 150 72 NM1 1020 93 JOHNSON CONTROLS 5 5 LD13239...
Page 176: ...JOHNSON CONTROLS 176 FORM 150 72 NM1 1020 THIS PAGE INTENTIONALLY LEFT BLANK...
Page 191: ...FORM 150 72 NM1 1020 191 JOHNSON CONTROLS 10 NOTES...