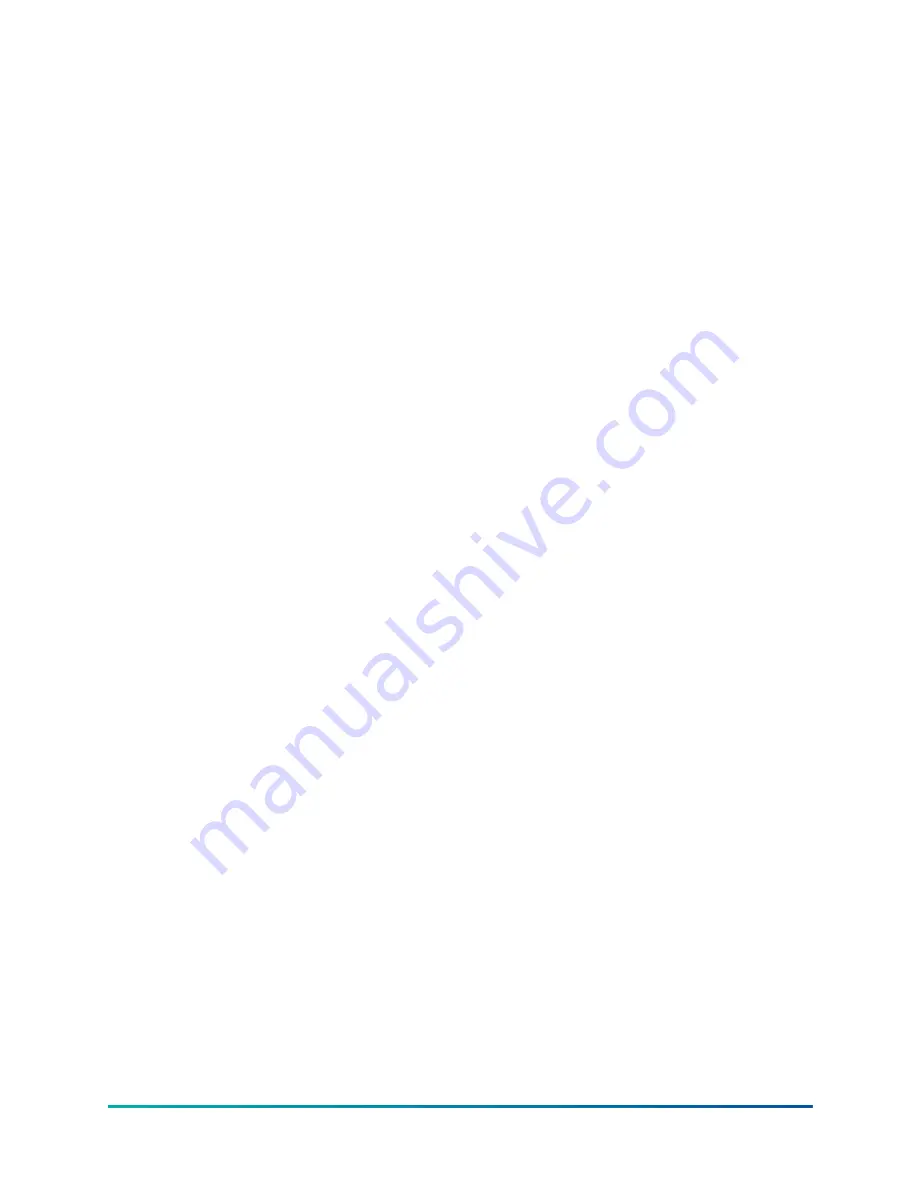
Oil heater
During long idle periods, the oil in the compressor oil reservoir tends to absorb as much refrigerant
as it can hold, depending upon the temperature of the oil and the pressure in the reservoir. As
the oil temperature is lowered, the amount of refrigerant absorbed increases. If the quantity of
refrigerant in the oil becomes excessive, violent oil foaming results as the pressure within the
system is lowered on starting. This foaming is caused by refrigerant boiling out of the oil as the
pressure is lowered. If this foam reaches the oil pump suction, the bearing oil pressure fluctuates
with a possible temporary loss of lubrication. This causes the oil pressure safety cutout to actuate
and stop the system. Refer to
OptiView™ Control Center – Operation and Maintenance (Form 160.54-
O1)
.
Motor driveline
The compressor motor is an open-drip-proof, squirrel cage, induction type constructed to YORK
design specifications. 60 Hz motors operate at 3570 rpm. 50 Hz motors operate at 2975 rpm.
The open motor is provided with a D-flange, cast iron adapter mounted to the compressor and
supported by a motor support.
The motor drive shaft is directly connected to the compressor shaft with a flexible disc coupling.
This coupling has all metal construction with no wearing parts to assure long life, and no
lubrication requirements to provide low maintenance.
For units using remote Electromechanical starters, a terminal box is provided for field connected
conduit. Motor terminals are brought through the motor casing into the terminal box. Jumpers are
furnished for three-lead type of starting. Motor terminal lugs are not furnished. Overload and over
current transformers are furnished with all units.
Heat exchangers
Evaporator and condenser shells are fabricated from rolled carbon steel plates with fusion welded
seams.
Heat exchanger tubes are internally enhanced type.
The evaporator is a shell and tube type with customer process fluid flowing inside the tubes and
refrigerant removing heat on the shell side through evaporation. Evaporator codes A* to K* utilize
a hybrid falling film design. It contains a balance of flooded and falling film technology to optimize
efficiency, minimize refrigerant charge, and maintain reliable control. A specifically designed spray
distributor provides uniform distribution of refrigerant over the entire length to yield optimum heat
transfer. The hybrid falling film evaporator design has suction baffles around the sides and above
the falling film section to prevent liquid refrigerant carryover into the compressor.
Evaporators codes M* to Z* are flooded type, with a liquid inlet distributor trough underneath
the tube bundle which provides uniform distribution of refrigerant over the entire shell length to
yield optimum heat transfer. Flooded evaporator designs have a suction baffle on M* shells with
H9 compressors and an aluminum mesh eliminator on K* to Z* shells with K compressors located
above the tube bundle to prevent liquid refrigerant carryover into the compressor.
A 1 1/2 in. (38 mm) liquid level sight glass is conveniently located on the side of the shell to aid
in determining correct refrigerant charge. The evaporator shell contains a dual refrigerant relief
valve arrangement set at 180 psig (12.4 barg) on H and K compressor models; 235 psig (16.2 barg)
on P and Q compressor models; or single-relief valve arrangement, if the chiller is supplied with
optional refrigerant isolation valves. A 1 in. (25.4 mm) refrigerant charging valve is provided. The
condenser is a shell and tube type, with a discharge gas baffle to prevent direct high velocity
impingement on the tubes. The baffle is also used to distribute the refrigerant gas flow properly
for most efficient heat transfer. An optional cast steel condenser inlet diffuser is offered, on M
and larger condensers, in lieu of the baffle, to provide dynamic pressure recovery and enhanced
23
Model YK Style G R-134a or R-513A