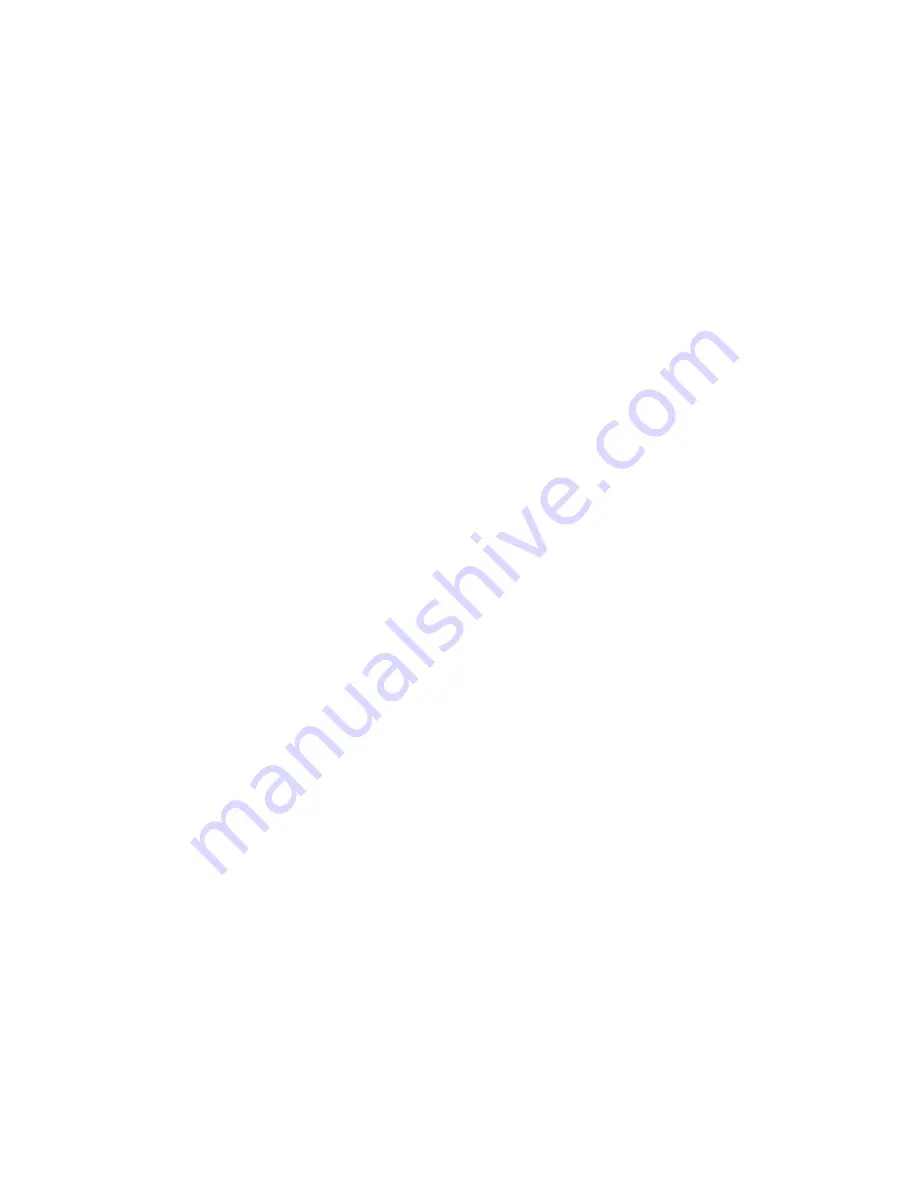
FORM 160.72-O1 (810)
JOHNSON CONTROLS
124
SECTION 4 - GENERAL OPERATING SEQUENCE
The PID Instruction is programmed to provide a
proportional plus reset response to deviations in
water temperature from the set point.
This control is forced to INACTIVE operation
with its setpoint tracking the chilled water out
temperature when the chiller is shutdown, dur-
ing ramp-up, and when the MAX-POWER DE-
MAND LIMITER, or the EVAP. LOW PRESS.
OVERRIDE, or the HIGH DISCHARGE PRES-
SURE OVERRIDE control signal is being used
to control the capacity of the chiller. See ramp-
up of capacity controls and override operation of
chilled water out temperature control found later
in this section for further details.
Maximum Power Demand Limiter
3.
This demand limit override control function uses
the motor power input signal to limit capacity.
When the motor power exceeds the setpoint, the
control puts out a decreasing signal. The SS and
LSR will then pass this lower signal on to close
the compressor pre-rotation vanes, thus reducing
the demand on the motor and returning the motor
power to setpoint.
The PID instruction is programmed to provide a
proportional plus reset plus derivative response to
deviations in motor power from the setpoint.
The display will indicate if the chiller is currently
in this override mode of operation.
Evaporator Low Pressure Override / High Dis-
4.
charge Pressure Override
During startup, the condensing pressure may ini-
tially be low. This can cause the refrigerant to
back up ahead of the intercooler expansion float
valve. If this occurs, the low level of evapora-
tor liquid uncovers a portion of the tube bundle,
thereby reducing the heat exchanger performance,
and lowering the evaporator pressure.
The Evaporator Low Pressure Override Control
provides an output signal which decreases as the
evaporator falls below a set point which is slightly
below design. When a low evaporator pressure is
sensed, the lower output signal is passed on by the
LSR to override the capacity signal and keep the
compressor pre-rotation vanes closed.
During run, conditions may occur that elevate
the discharge pressure to near trip conditions. To
attempt to keep the chiller online, the High Dis-
charge Pressure Override control will decrease its
output signal when its setpoint is exceeded. When
a high condenser pressure is sensed, the lower
output signal is passed on by the LSR to override
the capacity signal and keep the compressor pre-
rotation vanes closed.
The PID instruction is programmed to provide a
proportional plus reset response to deviations in
evaporator pressure from the setpoint.
The display will indicate if the chiller is currently
in this override mode of operation.
Intercooler Float Minimum Differential Pres-
5.
sure Control
This control senses when the differential pres-
sure across the intercooler float valve is too low,
and acts to close the interstage valve at differen-
tial pressures below the setpoint. This raises the
intercooler pressure, and insures that the float
valve will have sufficient pressure drop to accom-
modate the flow of liquid being expanded to the
evaporator, thus ensuring that any refrigerant col-
lects in the subcooler upstream of the liquid level
control valve. Otherwise, if the refrigerant were to
back up in the intercooler, large amounts of liquid
could enter the compressor interstage connection
causing potential damage.
The PID Instruction is programmed to provide a
proportional plus reset response to deviations in
float differential pressure from the setpoint.
The Control Output Signal is sent to the interstage
valve at the conclusion of the programmed delay
(0 to 10 minutes) after start-up when the ramped
valve control signal has increased to equal the PID
instructions output signal. At shutdown, the out-
put signal to the valve will decrease to 0 to close
the interstage valve.
The display will indicate if the chiller is currently
in this override mode of operation.
Anti-surge (Minimum PRV Position)
6.
As the differential HEAD pressure falls, the com-
pressor is capable of stable operation with less
refrigerant gas flow (lower minimum compres-
sor pre-rotation vane positions). From an energy
standpoint, it is wise to use the compressor pre-
rotation vanes for capacity control rather than
hot gas bypass whenever possible. The anti-surge
output signal to HSR provides a minimum closure
Summary of Contents for YORK OM Titan
Page 4: ...FORM 160 72 O1 810 JOHNSON CONTROLS 4 This Page Intentionally Left Blank...
Page 26: ...FORM 160 72 O1 810 JOHNSON CONTROLS 26 Evaporator Screen This Page Intentionally Left Blank...
Page 52: ...FORM 160 72 O1 810 JOHNSON CONTROLS 52 Setpoints Screen This Page Intentionally Left Blank...
Page 78: ...FORM 160 72 O1 810 JOHNSON CONTROLS 78 Options Screen This Page Intentionally Left Blank...
Page 80: ...FORM 160 72 O1 810 JOHNSON CONTROLS 80 Drive Options Screen This Page Intentionally Left Blank...
Page 96: ...FORM 160 72 O1 810 JOHNSON CONTROLS 96 History Screen This Page Intentionally Left Blank...
Page 104: ...FORM 160 72 O1 810 JOHNSON CONTROLS 104 Custom Screen This Page Intentionally Left Blank...