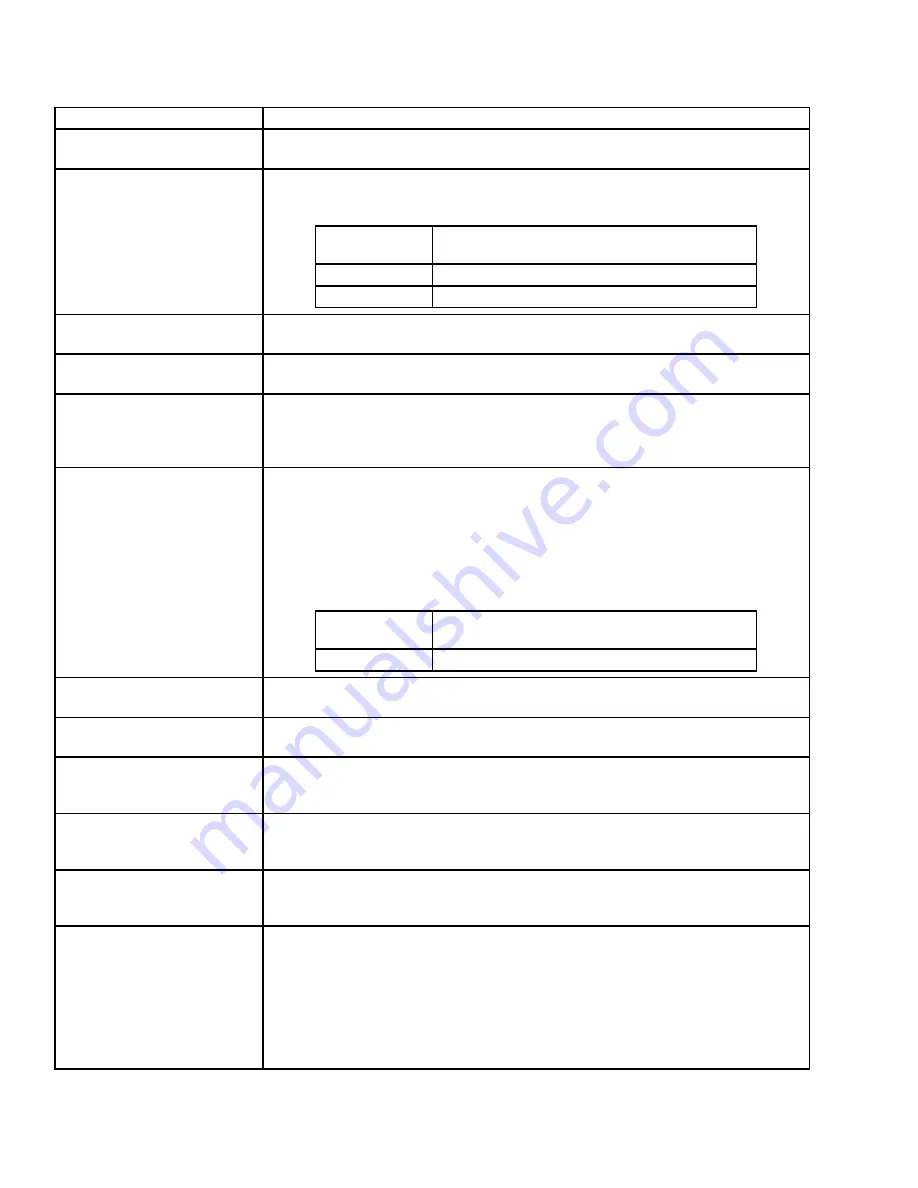
JOHNSON CONTROLS
16
FORM 160.00-O10
ISSUE DATE: 8/24/2020
SECTION 2 - SAFETY SHUTDOWNS
MESSAGE
DESCRIPTION
VSD – HIGH PHASE C INPUT
BASEPLATE TEMPERATURE
See “VSD – HIGH PHASE A INPUT BASEPLATE TEMPERATURE” message preceding.
VSD – HIGH PHASE A MOTOR
BASEPLATE TEMPERATURE
The chiller has shutdown because the motor baseplate temperature exceeded the
shutdown value for the given model of drive listed below. After the unit trips, the VSD
fan(s) and water pump(s) shall remain energized for 2 minutes after the fault occurred.
DRIVE MODEL
HIGH PHASE A MOTOR BASEPLATE
TEMPERATURE SHUTDOWN VALUE
1100
160°F (71.1°C)
1300
150°F (65.5°C)
VSD – HIGH PHASE B MOTOR
BASEPLATE TEMPERATURE
See “VSD – HIGH PHASE A MOTOR BASEPLATE TEMPERATURE” message
preceding.
VSD – HIGH PHASE C MOTOR
BASEPLATE TEMPERATURE
See “VSD – HIGH PHASE A MOTOR BASEPLATE TEMPERATURE” message
preceding.
VSD – HIGH TOTAL DEMAND
DISTORTION
This shutdown indicates the input current to the VSD is not sinusoidal. This shutdown will
occur if the Total Demand Distortion (TDD) exceeds 25% continuously for 45 seconds.
The displayed TDD is the sum of the harmonic currents up to the 50th harmonic supplied
by the main power to the VSD divided by the Full Load Amps.
VSD – INPUT CURRENT
OVERLOAD
The input current overload value is variable based on the Input Job Full Load Amps value
programmed at the Control Panel. The input current overload value is 1.16 times the
Input Job Full Load Amps value, but not to exceed the value for the given model of drive
listed below. This calculation takes into account installations where the input line voltage
could be up to 10% below the nominal value. An additional 5% of current is added to
reduce nuisance shutdowns due to power fluctuations. To provide addition time for the
chiller too unload, the input current overload value must be greater than the shutdown
value for 10 continuous seconds for this shutdown to occur.
DRIVE MODEL
INPUT CURRENT OVERLOAD MAXIMUM
SHUTDOWN VALUE
1100/1300
1305 Amps
VSD – INPUT DCCT OFFSET
LOCKOUT
If three consecutive VSD – Phase A, B or C Input DCCT Offset cycling faults occur, this
safety shutdown is generated to require investigation and manual reset.
VSD – INVERTER PROGRAM
FAULT
The VSD software contains a verification process to ensure that the correct set of
software is installed in the VSD logic board for the application.
VSD – LINE VOLTAGE PHASE
ROTATION
The input voltage to the VSD is not phase rotation sensitive, but the VSD must be able to
determine the correct input phase rotation. If the VSD logic board cannot determine the
correct phase rotation, then this shutdown is generated.
VSD – LOGIC BOARD
HARDWARE
After power is applied to the chiller, the VSD logic board performs several internal tests to
ensure proper operation of the input power device. If the tests fail, then this shutdown is
generated.
VSD – LOGIC BOARD PLUG
A jumper is located in the rectifier and inverter current transformers connectors that
indicate the connector is properly installed. If either connector is not installed, then this
shutdown is generated.
VSD – MOTOR CURRENT
IMBALANCE
Each phase of motor current is compared against the average of the three phases of
motor current to determine the current imbalance value. If the current imbalance value is
greater than 32 amps for a period of 45 seconds, then this shutdown is generated. For
example: The three motor current RMS values are 200, 225, and 240 amps. This would
calculated to an average current of (200 + 260 + 240)/3 = 233 amps. Subtract the real
current value from the average value. 200 – 233 = 33, 260 – 233 = 33, 240 – 233 = 7. If
this condition or worse were maintained for 45 seconds, then this shutdown is generated,
because the motor current imbalance is 33 amps.
TABLE 2 -
SAFETY SHUTDOWNS MESSAGE (CONT'D)