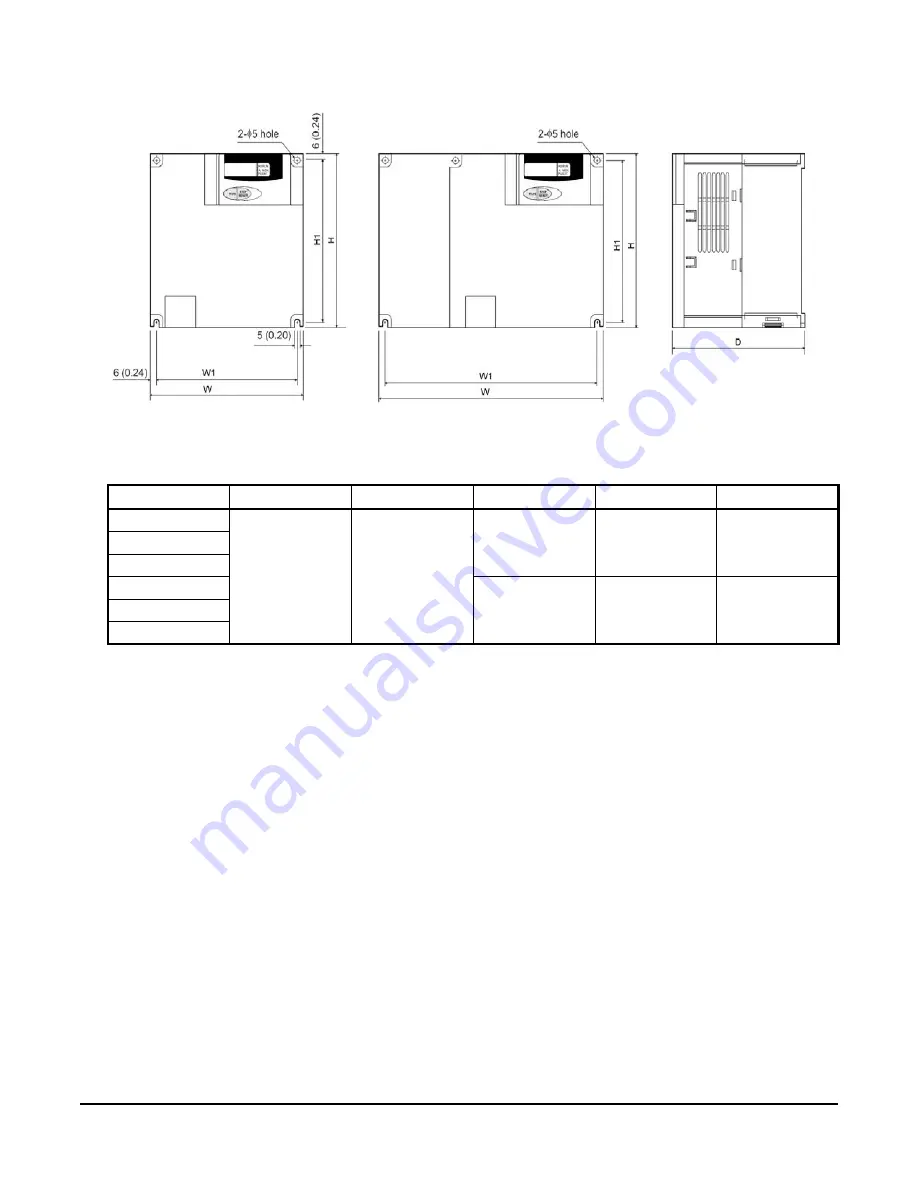
VFD68 Variable Frequency Drives
12
Dimensions for VFD68Dxx Drives
Table 9: Dimensions for VFD68Dxx Drives, mm (in.)
VFD Model
H
H1
W
W1
D
VFD68DFM
150 (5-15/16)
138 (5-7/16)
140 (5-1/2)
128 (5-1/16)
136 (5-3/8)
VFD68DGM
VFD68DHM
VFD68DJN
228 (8-11/16)
208 (8-3/16)
148 (5-13/16)
VFD68DKN
VFD68DLN
Figure 4: Dimensions for VFD68Dxx Drives, mm (in.)