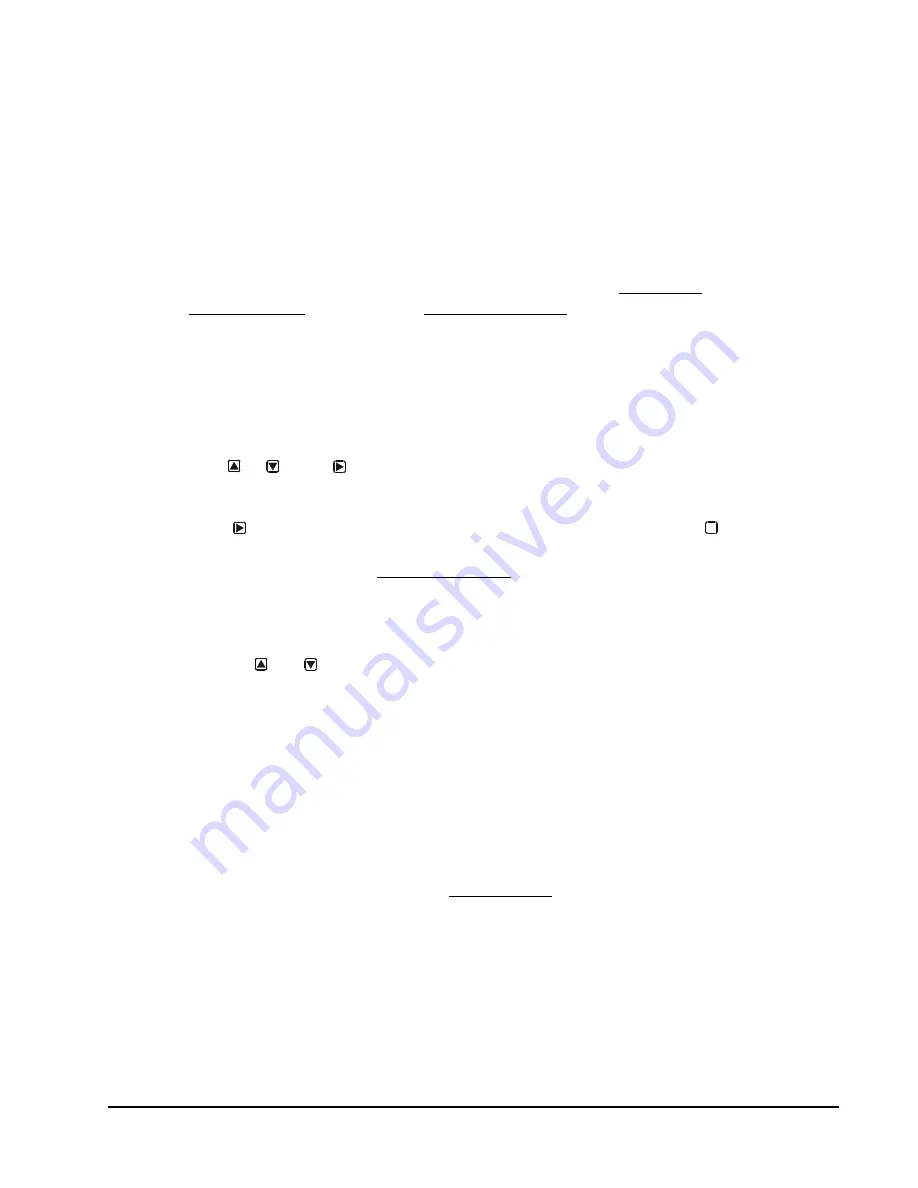
System 450™ Series Modular Control Systems with Standard Control Modules Technical Bulletin
47
After you have selected the correct Sensor Type for each sensor in your control
system, the sensors are set up in the UI and can be selected and referenced by
the outputs that you set up in the system.
Note:
Beginning with firmware Version 2.00, System 450 standard control
modules also provide for three functional sensors. When Sn-1 and Sn-2 are
set up as the same Sensor Type, the High Input Signal Selection functional
sensor (HI-2) and Differential Control functional sensor (Sn-d) are enabled
and available in the Sensor Selection screens for each output. When Sn-1,
Sn-2, and Sn-3 are the same Sensor Type, the High Input Signal Selection
functional sensor (HI-3) is also enabled and available. (See
information on these functional sensors and the associated control
features.)
5. If a temperature Sensor Type (
°F
,
°C
,
HI°F
, or
HI°C
) is selected for a sensor in
your control system, a
Select Temperature Offset (OFFS
x
)
screen is
displayed after the
Select Sensor 3 Type (Sn-3)
screen (for each temperature
sensor in your control system). Select the desired temperature offset by
pressing or . Press to save the offset value and go to the next screen.
6. After all of the sensors and temperature offsets are set up:
•
Press to return to the
Sensor Setup Start (SENS)
screen; then press
to scroll through the output setup start
screens and set up the outputs in
setting up outputs for your control module.)
•
Allow the UI to remain dormant for 2 minutes and the Main screens begin
to autoscroll. You may also return to the Main screens immediately by
pressing and simultaneously while a Setup Start screen is displayed.
Setting up Outputs
After setting up the sensors for your System 450 standard control system, you can
reference the hard-wired sensors (and any functional sensors that resulted from the
hard-wire sensor setup) as you set up the outputs.
Setting up a Relay Output
Relay Outputs provide single and multiple stage on/off control to controlled
equipment. A Relay Output can be set up to be a direct acting relay or reverse
acting relay (Figure 20 and Figure 21). See
information about System 450 Relay Output operation and the relay ON and OFF
states.
M