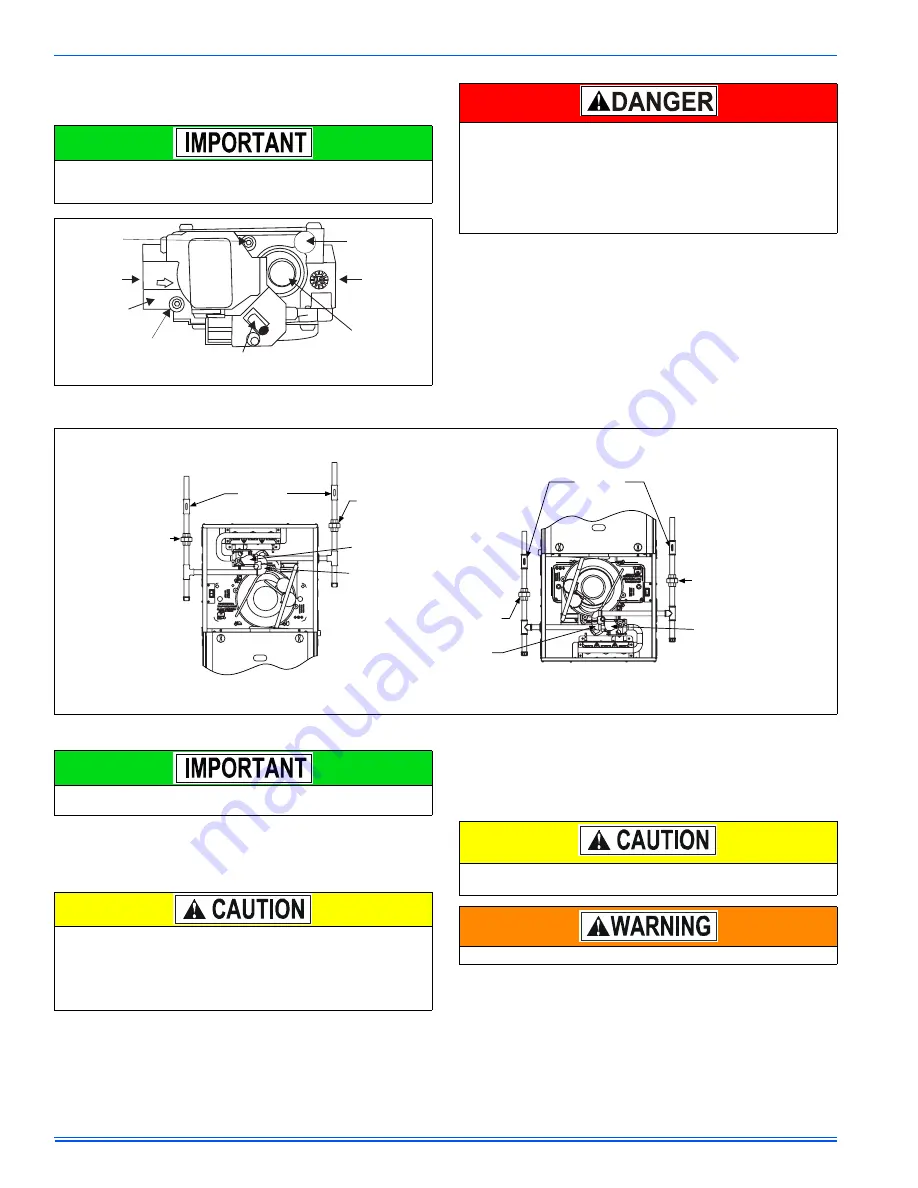
420705-UIM-C-0310
10
Johnson Controls Unitary Products
SECTION IV: GAS PIPING
GAS SAFETY
GAS PIPING INSTALLATION
Properly sized wrought iron, approved flexible or steel pipe must be
used when making gas connections to the unit. If local codes allow the
use of a flexible gas appliance connection, always use a new listed con-
nector. Do not use a connector that has previously serviced another gas
appliance.
Some utility companies or local codes require pipe sizes larger than the
minimum sizes listed in these instructions and in the codes. The furnace
rating plate and the instructions in this section specify the type of gas
approved for this furnace - only use those approved gases. The instal-
lation of a drip leg and ground union is required. Refer to Figure 15.
The furnace must be isolated from the gas supply piping system by
closing its individual external manual shutoff valve during any pressure
testing of the gas supply piping system at pressures equal to or less
than 1/2 psig (3.5 kPa).
Gas piping may be connected from either side of the furnace using any
of the gas pipe entry knockouts on both sides of the furnace. Refer to
Figure 12.
GAS ORIFICE CONVERSION FOR PROPANE (LP)
This furnace is constructed at the factory for natural gas-fired operation,
but may be converted to operate on propane (LP) gas by using a fac-
tory-supplied LP conversion kit.
1.
Shut off gas supply at valve upstream from furnace or at meter as
required.
2.
Disconnect gas supply piping from gas valve on furnace.
3.
Disconnect electrical wires from gas valve, noting which wires are
connected to which terminals
4.
Remove the screws that attach the gas manifold to the burner sup-
port box.
5.
Remove and discard natural gas orifices.
Plan your gas supply before determining the correct gas pipe entry.
Use 90-degree service elbow(s), or short nipples and conventional
90-degree elbow(s) to enter through the cabinet access holes.
FIGURE 14:
Gas Valve
INLET
WRENCH
BOSS
INLET
PRESSURE
PORT
ON
OFF
ON/OFF SWITCH
(Shown in ON position)
MAIN REGULATOR
ADJUSTMENT
OUTLET
OUTLET
PRESSURE
PORT
VENT PORT
An overpressure protection device, such as a pressure regulator,
must be installed in the gas piping system upstream of the furnace
and must act to limit the downstream pressure to the gas valve so it
does not exceed 0.5 PSI (14" w.c. (3.48 kPa). Pressures exceeding
0.5 PSI (14” w.c. (3.48 kPa) at the gas valve will cause damage to
the gas valve, resulting in a fire or explosion or cause damage to
the furnace or some of its components that will result in property
damage and loss of life.
FIGURE 15:
Upflow/Downflow Gas Piping
Upflow
Configuration
Downflow
Configuration
External
Manual
Shut-off
Valve
External
Manual
Shut-off
Valve
To Gas
Supply
To Gas
Supply
To Gas
Supply
To Gas
Supply
Drip
Leg
Drip
Leg
Drip
Leg
Drip
Leg
Gas
Pipe
Gas
Valve
Gas
Pipe
Gas
Valve
Ground
Union
Ground
Union
Ground
Union
Ground
Union
NOTE: Ground Union maybe installed inside or outside unit.
An accessible manual shutoff valve must be installed upstream of
the furnace gas controls and within 6 feet (1.8 m) of the furnace.
The gas valve body is a very thin casting that cannot take any
external pressure. Never apply a pipe wrench to the body of the gas
valve when installing piping. A wrench must be placed on the octa-
gon hub located on the gas inlet side of the valve. Placing a wrench
to the body of the gas valve will damage the valve causing improper
operation and/or the valve to leak.
The gas supply must be shut off prior to disconnecting the elec-
trical power, before proceeding with the conversion.
SHOCK HAZARD - Turn off electrical supply to furnace.