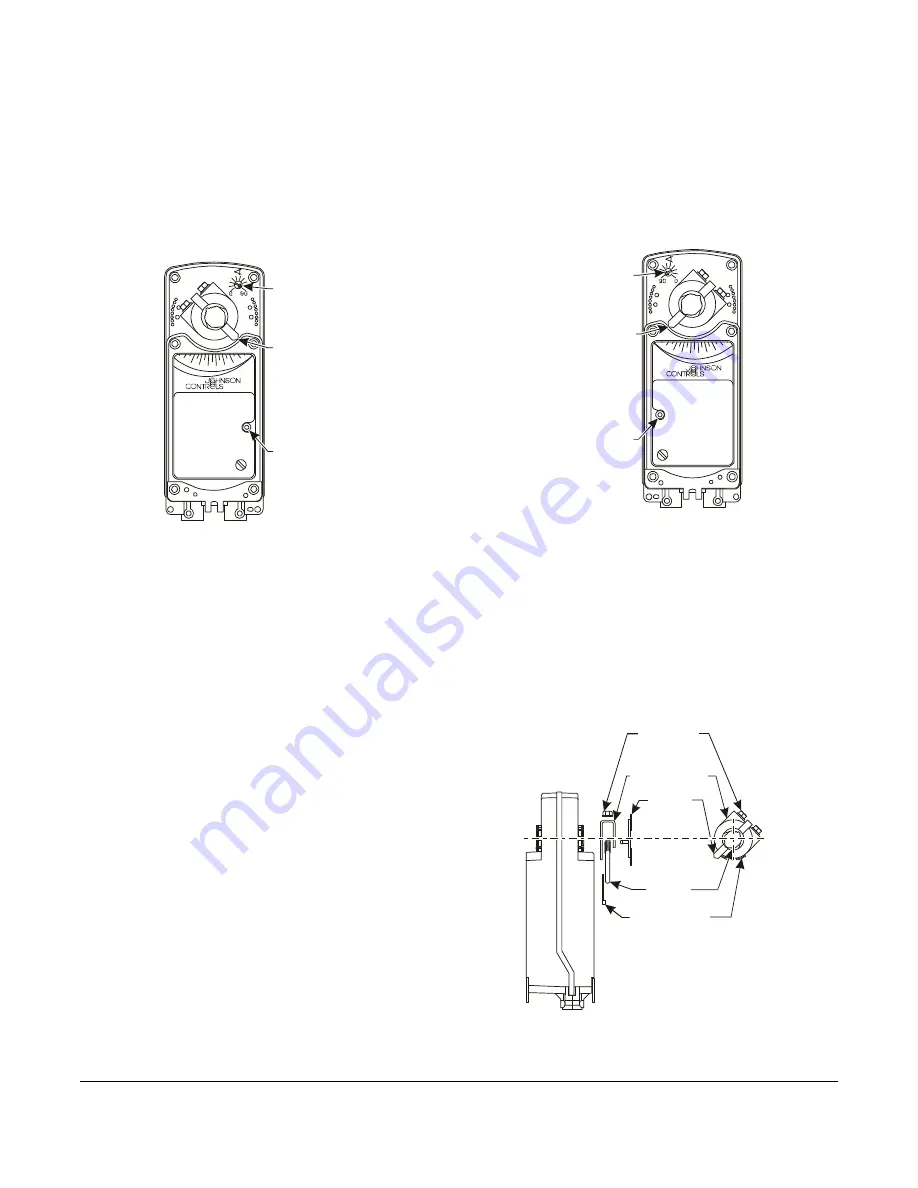
M9220-GGx-3 Proportional Electric Spring Return Actuators Installation Guide
5
Counterclockwise (CCW) Spring Return
Direction – Clockwise (CW) Powered
Operation
For CCW spring return direction, mount the actuator to
the damper shaft so that Side A of the actuator is away
from the damper as illustrated in Figure 2. With power
applied, the actuator drives CW from the 0° position,
and spring returns CCW.
Clockwise (CW) Spring Return Direction –
Counterclockwise (CCW) Powered Operation
To change the spring return direction to CW, mount the
actuator to the damper shaft so that Side B of the
actuator is away from the damper as illustrated in
Figure 3. With power applied, the actuator now drives
CCW from the 0° position, and spring returns CW.
Removable Coupler
The coupler may be installed on either side of the
output hub. If the damper shaft is less than 3-19/32 in.
(91 mm) long, insert the coupler in the face of the
actuator closest to the damper. If the damper shaft is
shorter than 1-5/32 in. (29 mm) long, a shaft extension
is required to mount the actuator.
Figure 2: Side A of Actuator
A
90
-5
10
20
30
40
50
60
70
80
Manual
Override
Pointer Showing
Actuator in the
Spring Return
Position
Auxiliary Switch
Adjuster Located
on the Right
FI
G
:s
id
ea
Side A: CCW Spring Return Direction
Figure 3: Side B of Actuator
B
90
-5
10
20
30
40
50
60
70
80
Auxiliary Switch
Adjuster Located
on the Left
Pointer Showing
Actuator in the
Spring Return
Position
Manual
Override
FI
G
:s
id
eb
Side B: CW Spring Return Direction
Figure 4: Changing the Position of the Coupler
Shaft Coupler
U-Bolt Nut
and Washer
(Qty Two)
Pointer
U-Bolt
Locking Clip
FIG
:ch
pos
Assembled View
of Coupler
Subassembly